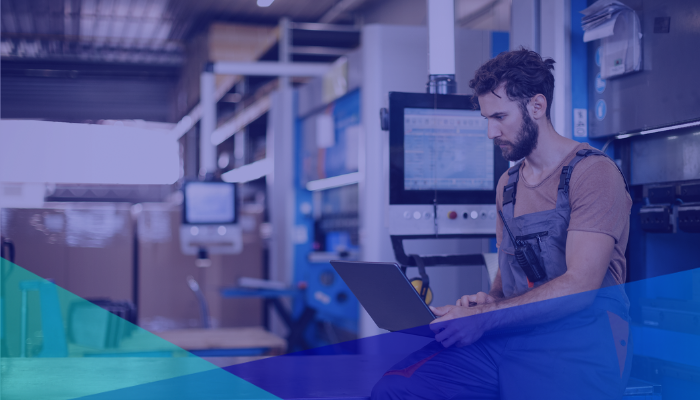
The reactive approach to maintenance in most factories isn’t working. Manufacturers spend 40% or more of their operating budget on maintenance. Yet breakdowns are still common — so much so that ineffective maintenance can lower plant productivity by up to 20%. Scale those losses across multiple facilities and maintenance can cost manufacturers a fortune.
The reactive approach to maintenance in most factories isn’t working. Manufacturers spend 40% or more of their operating budget on maintenance. Yet breakdowns are still common — so much so that ineffective maintenance can lower plant productivity by up to 20%. Scale those losses across multiple facilities and maintenance can cost manufacturers a fortune
Manufacturers have long needed a new approach to maintenance — one that reduces both planned and unplanned downtime and the labor involved in making repairs while improving overall equipment effectiveness (OEE) metrics across the board.
Machine Health and Condition-Based Maintenance
Condition-based maintenance relies on leading indicators — the vital signs of machine health like vibration and temperature — rather than lagging ones. Augury’s machine health data reveals the condition of equipment in real time, and our alerts provide prescriptive insights to tell you how to correct any detected malfunctions. Decision makers can use this data to prevent costly equipment breakdowns, schedule repairs in advance, and ultimately turn unplanned downtime into planned downtime (or eliminate it altogether).
Condition-based maintenance addresses the two main priorities of OEE. First, it reduces the amount of downtime overall — planned or unplanned. Addressing issues early means they’re still small; they require a fast, easy, and inexpensive fix compared to a complete breakdown. Basing maintenance decisions on actual machine health data also prevents unnecessary maintenance on equipment that doesn’t need it.
Second, condition-based maintenance helps with improving productivity in manufacturing while simultaneously lowering cost. With unplanned downtime eliminated, maintenance and production can effectively coordinate their efforts so necessary maintenance doesn’t affect deadlines or quotas. And by maximizing OEE, prescriptive maintenance helps manufacturers extract the highest ROI from equipment.
Condition-Based Maintenance in Action
This approach delivers quick time to value that grows over time. As manufacturers collect more machine health data from more sensors spread throughout a factory, they gain the ability to identify trends, anticipate failures, and quantify the remaining lifespan and production capability of any piece of equipment.
Once condition-based maintenance becomes the standard, manufacturers can use OEE to their advantage. For example, if a production line needs to speed up to meet a tight deadline, machine health monitoring data can help users know whether their equipment can rise to the occasion or whether it’s likely to break down and make the situation worse. Knowing that upfront, managers can then address maintenance preemptively or divert production to other lines. Either way, outcomes improve significantly.
It’s no wonder condition-based maintenance and prescriptive insights driven by machine health data are quickly becoming best practices for OEE. To see how Augury can help you reduce downtime and increase productivity, schedule a demo today.