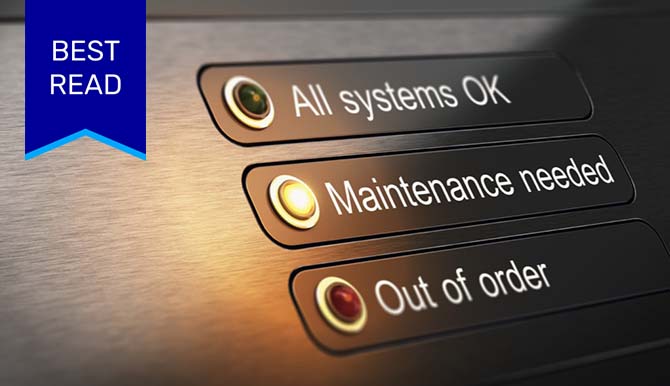
Condition-based monitoring is the most effective approach to machine maintenance. A reactive maintenance approach only comes in after something has already gone wrong. However, a preventive approach happens at pre-scheduled intervals with condition-based monitoring giving maintenance managers oversight of machines at all times. This way, they can send in technicians only when it’s necessary and before an issue leads to machine downtime.
A version of this post was originally published on May 4th, 2021.
Fitbit your Factory
Condition-based monitoring is like putting a health tracker on a piece of industrial equipment. Sensors attached to equipment assess aspects of machine health through various methods – ultrasound, thermography, specialized electrical testing, oil analysis, and vibration analysis. In turn, maintenance teams can use that data to identify patterns and predict machine failure. As a result, three essential workflow transformation occur:
- Reactive to proactive maintenance
- Negative to positive reward reinforcement
- Open- to closed-looped controls
Vibration analysis is an especially important form of condition-based monitoring because it provides the deepest insights into a machine. By monitoring vibration through sensors, manufacturers can note changes to detect the full spectrum of machine faults.
In an earlier era, vibration analysis required expensive equipment, complicated software, skilled analysts, and lots of manual effort to gather and interpret data. That’s why factories knew relatively little about machine health and had to rely on reactive or predictive approaches to maintenance.
Vibration Analysis For All
With the advent of new and innovative technologies, however, vibration analysis and other forms of condition-based monitoring have never been easier, cheaper, or more perceptive than they are today.
What’s more, Augury’s accessible and holistic machine health solutions take maintenance a step beyond predicting failure to providing prescriptive insights. Augury’s sensors perform condition-based monitoring and then feed data into advanced algorithms that accurately diagnose faults and suggest corrective actions. Manufacturers can receive prescriptive insights on every machine.
This accessibility means condition-based monitoring and prescriptive maintenance are no longer the next big things in manufacturing — they’re already here, and soon they will be table stakes.
A Paradigm Shift in Progress
Now that machine health data has become easier than ever before to monitor, analyze, and act upon, maintenance will never be the same. As innovative approaches become the norm in manufacturing, we’re seeing the following paradigm shifts in the industry:
1. Reactive to proactive maintenance
Once manufacturers gain the ability to track machine health in depth and in real time, they don’t have to wait for breakdowns to realize there’s a problem. They know well in advance and can send technicians on-site at the earliest warning sign.
A condition-based monitoring program built on quality machine health data makes proactive maintenance a reality for the first time ever. Manufacturers can act early and effectively so that machine downtime and a host of other issues have less risk of disrupting production.
2. Negative to positive reward reinforcement
A reactive approach to maintenance leads to negative reinforcements. When maintenance teams are always reacting to emergencies, somebody ends up in the hot seat — someone is too slow, unprepared, making mistakes. In this kind of high-stress environment, motivation comes from all the wrong places; people work against each other rather than with each other.
On the contrary, a condition-based monitoring approach to maintenance can encourage the exact opposite kind of reinforcement. Instead of focusing on placing blame for the catastrophe that did happen, you focus on celebrating the successes — or the catastrophes you avoided. For example, if a technician goes in to repair a machine and sees damage that surely would have led to failure, they know they have actually prevented that failure.
It’s easy to envision how expensive and time-consuming the repair would have been. Finding the wins to celebrate is easy with a condition-based approach. Now, instead of being motivated by a fear of failing or being called out, maintenance teams are motivated by the opportunity to achieve their best.
3. Open- to closed-looped controls
Two common control schemes that everyone experiences in their daily lives are open loop and closed loop. Open-loop control means performing a series of predefined actions and hoping they have the desired outcome, though the final outcome is fraught with uncertainty.
If only one ceiling fan needs to be cleaned, for instance, why clean them all?
This is analogous to managing a plan using only planned maintenance. You do maintenance tasks based on a schedule but not based on the unique needs of your equipment. This could mean you miss important maintenance tasks on some items or do unnecessary ones on others. If only one ceiling fan needs to be cleaned, for instance, why clean them all?
Condition-based monitoring and machine health, on the other hand, serve as the feedback mechanisms necessary to enable closed-loop control. This control scheme sets specific targets and measures progress against those targets so fine corrections can be made to keep them on track.
If your target is a healthy machine, for example, you can make repairs until the desired outcome is achieved. If a machine starts to deteriorate, you can identify the problem early and make small corrections to make it healthy again. All precision maintenance programs should be led by closed-loop control.
Condition-Based Monitoring: A Foundation for Transformation
Each of these shifts is pivotal on its own, but together, they form a strong foundation for the transformation of maintenance and reliability best practices. With a condition-based approach and predictive insights, you can leave outdated schedules and unexpected fire drills in the past and lean into the future of maintenance with more data and better insights.
Learn more about enabling condition-based maintenance.