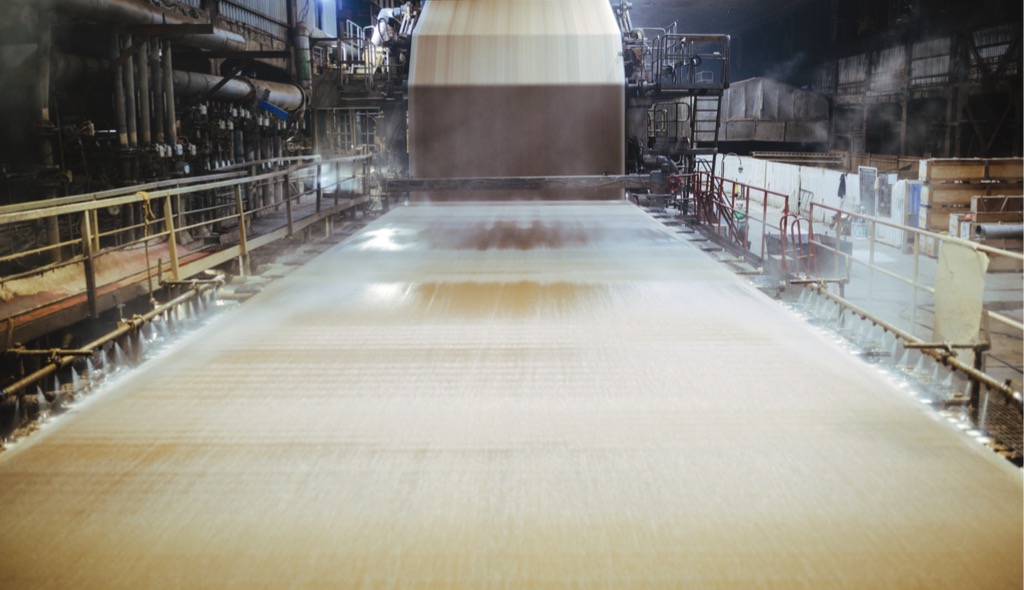
Shane Hopkins is Augury’s Senior Enterprise Account Executive for Pulp & Paper. While industry heavy-hitters such as Essity have now embraced Augury’s full-stack solution, they first needed to be convinced this was the right partnership to accomplish their short- and long-term goals. In this article, Shane explains and bullet-points the main reasons industry leaders have found Augury to be uniquely positioned to provide the most impact throughout their enterprises.
Unplanned Downtime Can Be Eliminated
IoT sensors are not new or unique in the Pulp & Paper industry – nor are predictive maintenance (PdM) softwares, VA teams, and all the rest. But even if you already have these resources, you are probably still experiencing unplanned mechanical downtime. So what’s that costing you?
Ten years ago, Augury took a unique approach to reliability with a vision of enabling manufacturers to always rely on the machines that matter. Early on, we learned that the only way of truly accomplishing this is by providing companies with a fully integrated, end-to-end, Digital Machine Health Monitoring solution. This approach eliminates the question of “How many sensors can we fit into the budget?” and starts the conversation around “Which machines would have the biggest impact if they never unexpectedly failed on us again?”
Proven Approach: Giving A Full Dam
Some of the world’s largest Pulp & Paper companies, including Essity, are realizing millions of dollars in annual savings, and scaling Augury throughout their enterprise. This level of large-scale success is the result of clearly aligning with Augury on the desired business outcome, having a realistic view on operational and financial impact, and defining success metrics prior to implementation.
Based on these clear goals, we then provide you with all the required resources. A partially-built dam will continue to leak. To eliminate all unplanned mechanical downtime, you have to have all the right hardware, software and services necessary to catch all problems on your critical equipment before they happen. You need the full dam!
I know you probably hear from vendors all the time who promise the world. But then they end up offering more of the same. So let’s just line up some of the ways Augury takes a different approach from anyone else in the market:
1) A Simple Solution: Machines Talk, We Listen
Have you ever used the mobile app, Shazam? It listens to the song you are playing and then tells you the name of the artist and song. Similarly, Augury captures information about your machine and provides automatic details about upcoming issues and how to fix them before they happen. This ability to go beyond the limitations of threshold-based sensors enables Paper & Pulp companies to get world-class insight into the health of your machines – with over 99% accuracy.
2) Largest Machine Health Database in the World
Throughout the past decade, we’ve collected over 100 million hours of machine health recordings. Especially given our experience with some of the largest Pulp & Paper companies in the world, we likely know your machines already. So if we notice something we’ve caught with other equipment in the past, we’ll know what the issue was and be able to give you the actionable insight to fix it.
3) Preventative Is Good. Predictive Is Great. Prescriptive Is Next-Level!
My background is in maintenance management software, from CMMS to EAM. I’ve seen companies significantly improve productivity by transitioning from “fire-fighting” to preventive maintenance. But then unplanned mechanical failures still happen! By going one step further to predict problems before they happen, does work to give you an important heads-up. But then your techs or VAs still need to figure out the actual problem. So machines still fail unexpectedly.
Now imagine if you have immediate access to actionable insight regarding the upcoming machine problems, what’s causing them, how to fix it, and the level of urgency? What if your maintenance planners could schedule maintenance based on the actual likelihood of machine failure, rather than OEM-based PM recommendations? What if your techs could walk up to a machine with tools-in-hand, rather than first needing to figure out the problem?
Digital Machine Health Monitoring is not out to replace your CMMS or EAM softwares. But it can help you optimize your PM scheduling and decision making capabilities. As a result, you can experience massive impact in a short period of time.
4) Augury Sensors Can Take The Heat – And The Cold and The Wet
Whether it’s the wet cold conditions of pulping or the dry heat needed to make paper, our sensors can take the abuse.
5) You Don’t Need A Lot Of Downtime To Cut Downtime
You don’t have to lose revenue installing our product. Our sensors are non-invasive, which means we can install with little or no disruption to your production. We’ll do it either while the plant is still running, or during a previously scheduled planned downtime.
6) Streamline Planned Downtime
Speaking of planned downtimes… Say, you have 50 assets but only have time to do PM on 25? How do you prioritize? Well, if you are monitoring the real-time condition of the equipment, you’ll know which 25 are the most likely to fail.
7) It’s Plug-And-Play (With Speedy-Time-To-Value-And-ROI)
No long learning curve required. Your team doesn’t have to take endless training courses. It’s up, running and creating value fast. On average, new Augury customers see between 3- to 10-times ROI within their first year.
Did your eyes light up? To ensure your success, we’d love to go through your unique business case and undertake an asset analysis to highlight the potential financial impact.
Reach out by email or phone me directly at +1-(239) 464-6692. Let’s jump into your details and build the full dam!