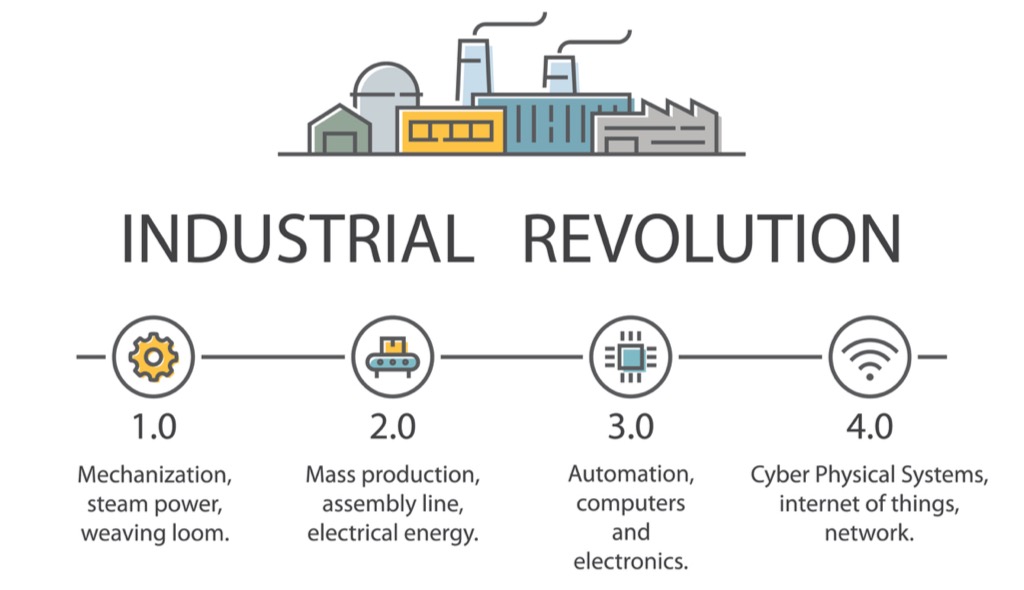
From an early case of industrial espionage, to a 1920s robot visionary, through to Machine Health… We chart the fascinating history of manufacturing and the lessons we learn from its successive revolutions.
Industry 1.0: Taking Manual Out Of Labor
The first industrial revolution allowed goods to be made by machines instead of manual labor. Also referred to as ‘Industry 1.0’, it’s often described as originating in England around 1760 and being largely coal-powered. However, if we excavate further, we actually find older stories – ones perhaps more relevant for our present challenges.
Beacons of Sustainability and Collaboration
For instance, the plucky Dutch in their battle against the sea had been using windmills since the 1400s to create land from bog. One game-changer arrived in 1593 when Cornelis Corneliszoon van Uitgeest patented a crankshaft that converted the horizontal power of wind into a vertical sawing motion. As a result, his saw mill could now convert logs into planks 30 times faster than previously. By the 1600s, the Netherlands had over 10,000 windmills, many of which had diversified to embrace a whole range of mechanized chores – from grinding flours and pigments, to making paper and fibers.
Over time, business flourished particularly along just 11 kilometers of the river Zaan near Amsterdam, where by the 18th century over 900 windmills were pumping out a whole rainbow of different products. Now Zaanse Schaans is recognized as the oldest industrial area in Western Europe, and was paramount in helping jumpstart Holland’s Golden Age.
While the early Dutch entrepreneurs were known to be fiercely independent, they were also deeply collaborative. This trait had likely evolved from having a shared enemy in the sea. Not only uniting to keep the waters at bay, they were also known to freely share mutually-beneficial innovations, as well as share risk through windmill fire insurance.
A Very Early Case Of Industrial Espionage
Meanwhile in Italy, textile innovators had ensured that water power was being used for spinning since the early 15th century. It was only in 1716, that an Englishman called John Lombe visited Piedmont and sneaked into a workshop to sketch and steal the technology to start his own mill back in Derby.
But while inspiring England with “his” invention, Lombe met a very early death. It’s said he was poisoned by a female assassin paid by Italian competitors. (Is there a moral to this story?)
Finally… The English Make Their Contribution
But yes, we must give credit where credit is due. The British did revolutionize cotton spinning and turned it into a volume industry. In 1769, Mr. Richard Arkwright patented the spinning frame for cotton and soon built the world’s first water-powered mill.
Arkwright is regarded as the “father of the modern industrial factory system”. He iterated endlessly while chasing the most efficient processes. Along the way, he built the first factory housing development to put up the extra workers he needed to scale his efforts. He also formulated the two 13-hour shift work day. And he cut corners in less elegant ways: two-thirds of his workers were children.
(There are definitely many lessons in this story.)
Letting Off Steam
Another major English power play was the invention of the first truly effective steam engine by James Watt. Patented in 1775, it soon powered ships, locomotives and machinery. Factories no longer had to be located near water or wind. With steam, they could be anywhere…
But yes, not everyone was happy. By the 1800s, the incomes of weavers were halved while the cost of living skyrocketed. When the negotiations between factory owners and a group of frustrated workers called Luddites fell apart, mechanized looms and spinning machines were destroyed. Troops were sent to crush the uprising. There were no winners.
The establishment of the telegraph and railway meant that ideas and people could scurry around much faster.
The Vroom-Vroom Of Industry 2.0: Electrifying Growth
The Second Industrial Revolution – aka the Technological Revolution – took place between 1871 and 1914. The establishment of the telegraph and railway meant that ideas and people could scurry around much faster. Electricity meant factories could embrace the modern production lines, with the automotive industry being pioneers.
In 1901, Ransom E. Olds, patented the first stationary production line – boosting his production from 425 to 2,500 cars within a year. Henry Ford went on to append this system with moving platforms and a conveyor system – so the cars came to the workers instead of the other way around. By 1926, Buick took it a further step with the Unified Assembly Line – pumping out 1,300 cars a day.
Things were booming: productivity, economies, unemployment.
Industry 3.0: Lean, Mean, Digital Machines
Also known as the Digital Revolution, the Third Industrial Revolution began in the second half of the 20th Century with the application of computer technologies. The innovation cycle accelerated as computers became more powerful – and, later, as internet speed and mobile connectivity increased. New processes had to be embraced, and endlessly fine-tuned, to deal with all these changes.
From Toyoda Looms to Toyota Cars
Leading the way was Toyota’s development of “Lean Manufacturing” (aka the Toyota Total Production System). While now largely known as an automotive company, it was originally more known for automatic textile looms. Its founder Sakichi Toyoda invented the concept of jidoka (automation with a human touch) by incorporating a device on the looms that would halt the loom whenever a thread broke – boosting quality while decreasing the need for quality control. Later, his son Kiichiro Toyoda would develop the concept of just-in-time (JIT) manufacturing to eliminate the need for excess inventory.
As the key elements of lean manufacturing, jidoka and JIT meant that by the 1970s Toyota had halved the man-hours needed to build a car. People noticed and developed their own lean approaches and applied them to other industries – from electronics to healthcare to construction.
In time to come the only work to be done by men and women will be that which requires faculties of discernment, discretion, and judgement. All other work – anything repetitive, routine, standardized – can better be done by machines.
I, Robot
Meanwhile in the endless drive to increase efficiency, automation and robotics developed in tandem. In 1926, R.J. Wensley had already invented a robot called Televox that could obey a human voice. Wensley also had a vision: “In time to come the only work to be done by men and women will be that which requires faculties of discernment, discretion, and judgement. All other work – anything repetitive, routine, standardized – can better be done by machines.”
In the 1940s, the first numerical control (NC) machine was developed by another visionary, John Parsons, by which a computer could automatically control machining tools such as drills, lathes, mills and (much later) 3D printers. Parson’s ultimate proof of concept came in 1948 when his company was awarded a military contract to make tapered wings for an aircraft. His system could not only formulate the complex 3D structure of the wings but also the required 800 manufacturing steps. However, due to the initial costs of the NC machines, Parsons was fired from his own company and only rehired when the patent royalties started rolling in. Sound familiar?
Meanwhile, progress marched on. By the 1980s General Motors tried to fully automate car factories. But despite $90 billion dollars over 10 years, the company could not be as efficient as its Japanese rivals. Critics said it was a case of too fast, too soon. And while the robots were indeed efficient, the old system on which they were grafted was not. An important lesson was learnt: know your problem before you set out to solve it.
It’s time to fully embrace the Imagination Age. Creativity is now the real driver of economic growth.
Industry 4.0: Welcome To The Future (Now)
Some argue that Industry 4.0 is just an extension of 3.0, and it certainly builds on the past just as with previous phases. But in terms of speed, scope and societal impact, the coming together of current innovations is worthy of its own revolution. And with our current challenges in terms of COVID and climate, the stakes are much higher.
Cloud computing, AI and IoT technologies are now being leveraged in a way that will enable manufacturers to fully digitally transform themselves in the short-term – maximizing production, while minimizing monetary and environmental costs.
At Augury, we believe the Information Age is behind us, and it’s time to fully embrace the Imagination Age. Creativity is now the real driver of economic growth. However, we won’t get far if we forget the lessons from the past. In short, we must follow a vision and push ourselves to respectfully collaborate and iterate on every step of the journey.
Reach out if you believe your manufacturing operation is in need of some Machine Health revolution.