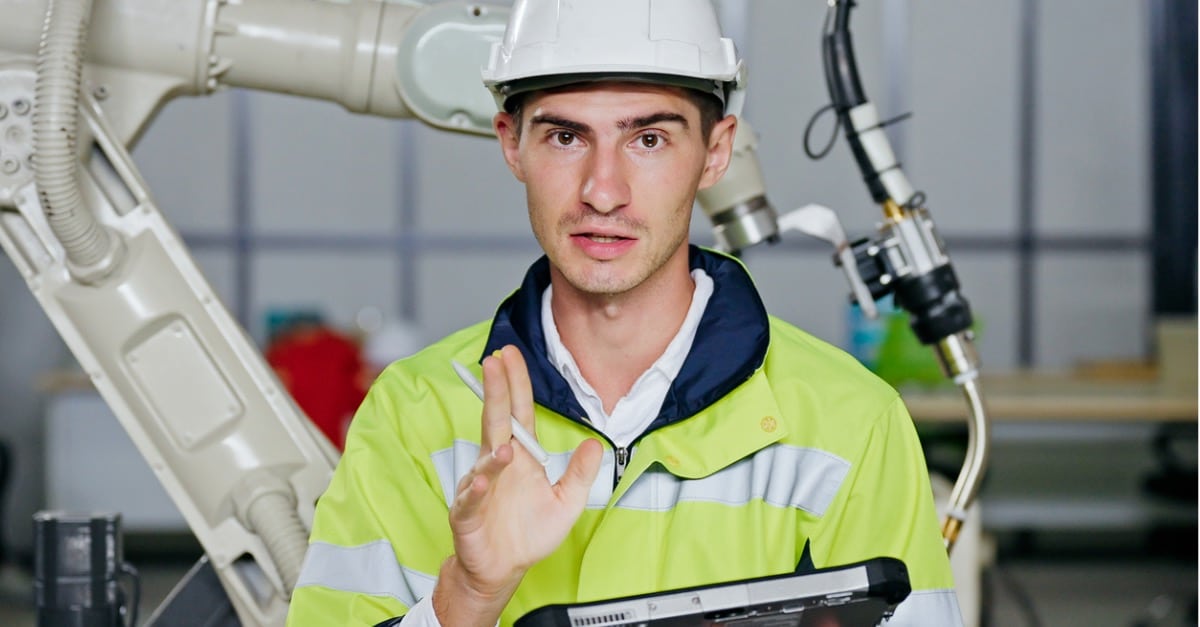
Are you on the market for a machine health solution? At first glance, it seems that there are countless options. But on closer inspection, many so-called AI-powered condition monitoring companies are still offering a solution that’s still very much routine-based or threshold-based.
Last week, the post ‘Beware Of Fake AI: Look Under The Hood Before You Buy’ sparked an in-house discussion on what are the best questions for manufacturers to ask when they are out to invest in an AI-driven manufacturing solution. After all, with few regulations and shifting vocabularies, many vendors are using whatever terms to make a sale – when in fact their AI is weak or non-existent.
So here are some questions to help you probe beneath the marketing fluff and really understand what you’re buying:
What is the quality of data and level of insights they are able to generate?
Today, a combination of high-bandwidth wireless protocols, hourly sampling and purpose-built Industrial AI can work to detect and diagnose a wide range of faults – both acute and gradual. However, many solutions typically collect and send much lower quality data, which severely limits their ability to provide timely and accurate diagnostics. In addition, other algorithmic approaches like ISO and adaptive-thresholds result in high false alarms (70%) and misses (15%) which puts you at risk of unplanned downtime.
How accurate are the alerts? And are these alerts predictive and prescriptive?
Ideally, the accuracy of the alerts should be dependable, scalable, and guaranteed. And such accuracy is further verified and made stronger if these alerts are predictive and prescriptive.
Only a true prescriptive diagnostics platform – one that loops in both machine and verifying human intelligence (Hybrid Intelligence) – can achieve consistent accuracy metrics that are dependable at scale. With offshored back office manual analysis there is too much variances in the quality of analysis to make guaranteed outcomes possible.
How many levels of AI and human intelligence do they employ for their condition monitoring?
To get deep, specific and reliable insights into your machines, you need different levels of Hybrid Intelligence (AI and human) running in tandem, such as:
- Anomaly detection (such as an algorithm focussed on where the issue is, and when did it happen)
- Fault detection (such as an algorithm focussed on what’s the issue and cause, and how can it be fixed)
- Severity analysis (such as an algorithm focussed on time until failure and how bad it will be)
- Expert intelligence (actual humans, such as vibration analysts and/or reliability engineers, providing an additional layer of support and interpretation for customers)
How quickly does their AI detect and diagnose machine failures? What is their rate of misses and false alarms?
Direct pattern recognition of equipment behavior can accurately deduce failure mode and root-cause with an accuracy that leans as close as possible to 100%. If you combine this type of AI with a Category III and IV vibration analysis team, you can detect and be alerted of failures rapidly from day one, even from machines less than 24 hours away from failure.
In comparison, threshold-based systems generate a significant volume of false alerts which when combined with slower response times from the back office analyst team, makes it harder to focus on the machines that are actually failing.
Are fault diagnostics reliable and accurate enough to be backed with an insurance policy?
When it comes to reliability, you need reliable diagnostics. Without that, your team would be flying blind and prone to make expensive mistakes. A lot of AI solutions are great, but almost always stumble with edge cases, misses, or inaccuracies.
To be sure that the AI solution you are buying is reliable, look for those that come with a diagnostics guarantee – in other words, if the diagnostics are wrong, you can file an insurance claim for any related losses.
Can they provide accurate diagnostics immediately after deployment or do they need to custom-build an AI model for you after the first failure?
If a solution already has hundreds of millions of hours of recorded machine data across hundreds of asset types and failure modes, the vendor won’t have to wait until your machine fails in order to create an algorithm. So be sure to understand what it means to “set the baseline” before you deploy. In other words, if the solution is learning and diagnosing from a large data set, value can happen faster. If that solution needs to start at zero, you have a longer road ahead of you before you start seeing value.
In conclusion…
There are more and more options out there and it can be daunting. But by asking these questions, you can be more sure you are choosing the best option that can drive value and scale across your company. Because when new technologies fail or are too difficult to adopt, it just sets everything back.
Of course, perhaps you’ve picked up that the best answers to all these questions should lead you to Augury. But if you have to shop around anyway, these questions will get you the answers you need to select the right machine health solution.
To learn more about Augury’s AI read our white paper ‘The Power of Augury’s AI’ or the post ‘10 Reasons Why Augury’s AI Is Exciting More People Than Just Manufacturers’.
To learn more about Augury’s AI read our white paper ‘The Power of Augury’s AI’ or the post ‘10 Reasons Why Augury’s AI Is Exciting More People Than Just Manufacturers’.