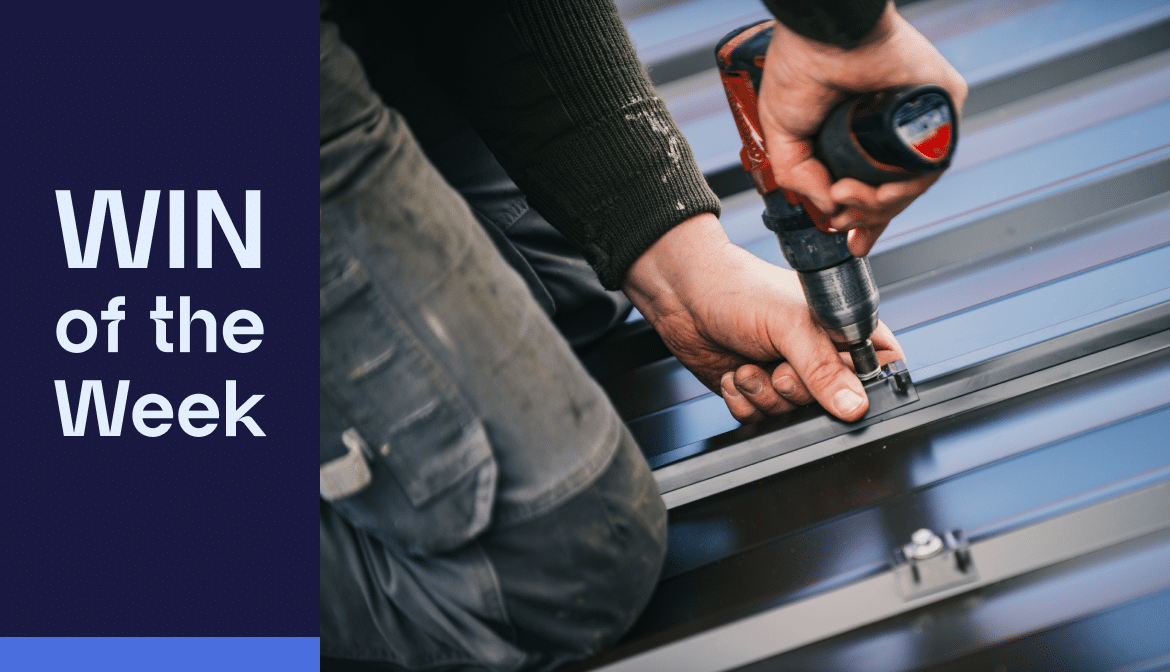
Industry: Building materials
Machine: Comerio calendar drive
Fault type: Bearing wear
Outcome: Saved more than $6M in downtime/maintenance and achieved 94x ROI
Setting the stage for success
A prominent building materials manufacturer adopted Augury’s Machine Health in February of 2023 with the goal of reducing downtime on key assets at their roofing facility. The company’s previous tool–a hand-held device – had proven ineffective at detecting failures, resulting in both high hopes for a more advanced continuous monitoring solution, as well as some skepticism among the maintenance team.
Following installment of Machine Health at the plant, Augury representatives kept in frequent contact with the company’s resource owners, maintenance managers, and schedulers, informing them of monitoring updates and checking in on the status of assets.
In March 2023, following two months of baseline monitoring and data collection, Augury detected two faults, one of which was for a comerio calendar drive–a critical piece of plant machinery that ensures high – quality output, allowing for a higher degree of accuracy in rubberizing. Augury’s Reliability Success Manager (RSM) knew that preventing a breakdown was paramount for the company, and followed up with the maintenance team on the alerts. Based on previous experience with similar machines, he recommended they investigate the drive, and warned that a failure could cost them three weeks of production across two shifts, on top of overtime maintenance costs.
A second alert and machine repair establishes trust
Believing they could continue running the machine safely, on-site teams decided to delay repairs while they continued watching the machine for deterioration. At the same time, another machine went into alert – a cooling fan also vital to the entire production line. Drawing on past experience, the RSM recommended the maintenance team investigate the machine for possible bearing wear. The inspection confirmed the theory and the bearings were replaced on an outage day, saving over $200k in downtime and repair costs.
Following two more months of monitoring of the comerio drive, the RSM grew increasingly concerned about a catastrophic failure. Showing them data that suggested a further spike in vibration levels, he urged the maintenance team to act immediately. The maintenance manager agreed and instructed his team to perform an investigation, which confirmed Augury’s finding that the machine was close to failure.
AI data, human insight, and collaboration pays off
Despite having delayed the repair, the maintenance team still had time to acquire the spare part and locate a specialist in time to perform the work – a scenario made possible by the early Machine Health monitoring detection and continual RSM guidance.
The bottom-line savings for the business equaled nearly $6.5 million from avoided downtime, maintenance costs, and lost production – a figure representing a colossal 94x return on investment.
How much can Augury save you? Crunch the numbers with our value calculator and discover how much time and money you can save with our proven approach to machine health.