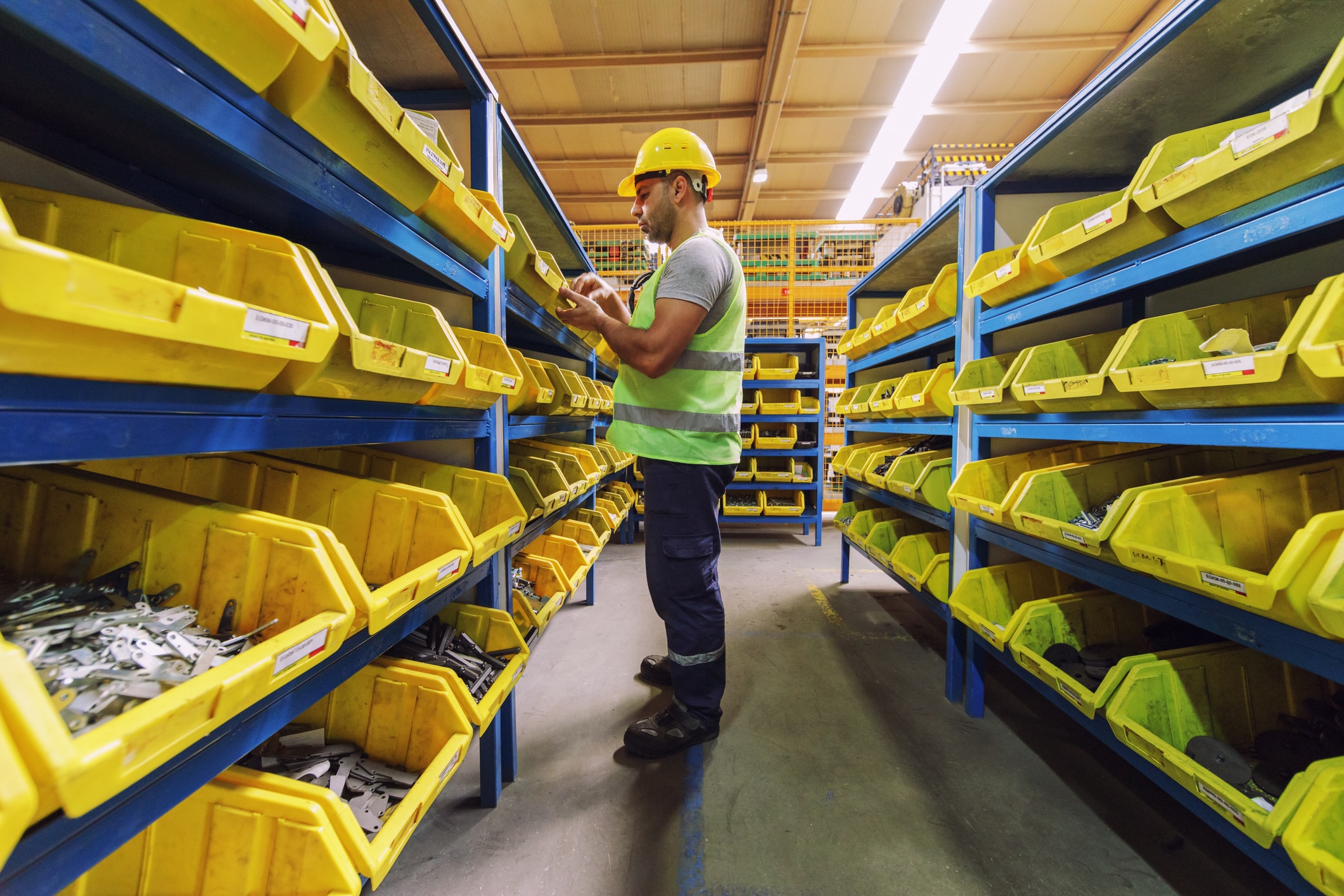
In the world of manufacturing, a well-organized storeroom is the unsung hero of production efficiency. Why? Because a strong program will help you lower inventory and reduce reliance on “hidden” stores and just-in-case parts. It’s also a critical part of any reliability improvement effort, ensuring that maintenance teams get the right parts in the right quantity in the right condition and at the right time.
How is your storeroom contributing to operational success at your plant? Managed strategically, a spare-parts storeroom will help maintenance teams become more efficient, improving OEE, raise safety standards, and boost morale.
As an Augury Presales Solutions Architect, I’ve had the privilege of interacting with many manufacturing sectors and stakeholders at every level, and I’ve seen the good and bad – from plants that lack any kind of storeroom strategy to those leveraging machine health data to streamline inventory efforts and parts ordering.
No matter where you are in your journey, these best practices will set you on the road to success.
1. Build a storeroom team
- The primary goal of storeroom operation is to balance spare part inventory levels to protect against lost production, with the storeroom team providing for the efficient and effective delivery of parts.
- Access to the store must be limited to authorized persons: The storeroom should have roles that align with the main functions of ordering, receiving, and issuing parts. While various organizations have different structures, these main functions must be covered to enable the smooth functioning of the storeroom.
2. Optimize the storeroom environment
- Be sure the storeroom gives you enough room to avoid congestion–the ability to find parts should be easy and include a defined catalog and storage process.
- The area should be well lit and have designated working areas that enable the storeroom team to effectively execute their work tasks.
- Employ a regular process to support the 5S conditions in the storeroom.
3. Prioritize spare-part organization and upkeep
- Be sure spare parts and tools/equipment are inventoried, controlled, and available, and regularly inspect and replace them as needed; regularly review inventory levels to ensure they are accurate and in compliance–no hidden stashes of parts in remote locations or technician tool boxes/lockers.
- Establish an area that can help spare parts avoid degradation and maintain like-new condition, i.e., bearings stored to prevent damage, belts stored to prevent exposure to UV lights or from physical storage, shafts on motors and gearboxes should be rotated regularly, reduce humidity to prevent rust on metal components.
- Label hazardous cabinets designated for flammable items.
4. Establish inventory controls
- Establish inventory management practices such as cycle counts, obsolete part removal, non-moving-part level reviews. Document receiving practices with inspection to verify parts match specs.
- Put practices in place to maintain the integrity of the parts and bill-of materials (BOM) lists; implement a process for creating, updating, and maintaining BOMs for new equipment, new parts, and obsolete parts.
- Create an automatic reordering processes, after-hours support, and ordering for emergency work.
- Use machine health data to supplement usage and stocking levels.
5. Create a planned-work staging process
- Create a process to kit spare parts for planned work and pre-stage part kits and tools for planned work.
- Create a process to return unused parts to stores within 24 hours of work completion and a process to dispose or restock parts.
- Use machine health data to plan what work to do and when to do it based on machine and parts condition.
By having the right structure and management practices in place, the storeroom can help ensure the reliability performance for the site. Implementing the techniques listed above can help achieve those ends and make the storeroom a trusted component in the journey to production excellence. You can even start to utilize a partnered solution like Augury’s Parts as a Service (PaaS) program with DSV to get the right parts when needed.
If you’re looking for more great resources on machine health, join The Endpoint, Augury’s free online community. You can interact with or learn from other manufacturing pros, comb through knowledge base articles, and take online courses to keep your skills sharp. I hope to see you there!