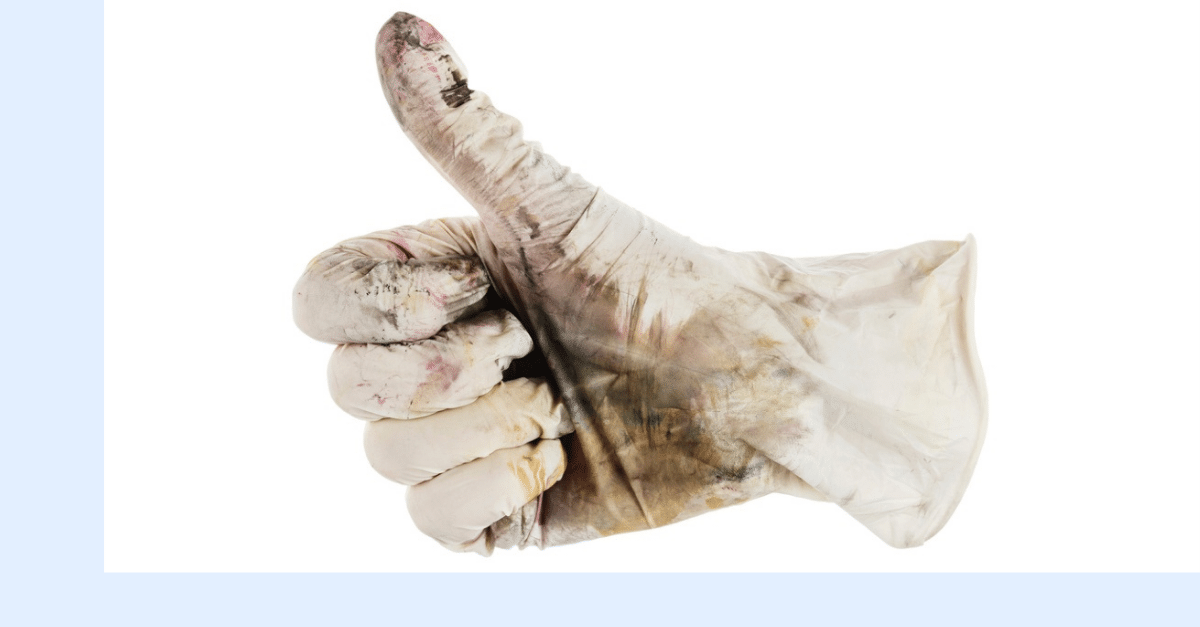
Forbes has published an article by Augury CEO Saar Yoskovitz about how American manufacturers can once again drive efficiency and profitability by deploying AI-driven tools. “AI has the potential to ease more than just the talent shortage – like increasing factory capacity and solving production challenges – but only if those on the factory floor have the exposure to AI and the needed proficiency to support these efforts,” according to Saar.
“American manufacturers are at a crossroads, needing to decide between evolution and obsolescence. The tools that historically drove profitability and efficiency are no longer having an impact,” according to ‘The AI Revolution With Grease Under Its Fingernails’ by Augury Co-Founder & CEO Saar Yoskovitz.
“Labor is hard to find and harder to keep. The National Association of Manufacturing projects that 2.1 million manufacturing roles will go unfilled by 2030. This hard truth is compounded by findings in Augury’s ‘State of Production Health’ report, which reveals that 91% of manufacturers say that the mass exodus of industry veterans will worsen the knowledge gap.”
Keeping Machines And Processes Healthy
To combat this “brain drain,” forward-thinking manufacturers are turning to AI solutions. These systems can preserve and digitize decades of industry expertise, effectively transferring knowledge from retiring experts to newer workers. For example, in predictive maintenance, AI systems trained on millions of hours of machine data can detect potential failures through changes in vibration, sound, and temperature – often before even experienced human operators would notice.
The article also highlights how AI is optimizing production lines by learning from historical data to establish ideal operating parameters. This technology helps operators identify when variables deviate from optimal levels and suggests corrective actions, improving quality, yield, throughput, and waste reduction even with fewer experienced staff.
Attract And Retain Valuable Talent
The manufacturing sector is also positioning itself to attract new talent, particularly as universities like Cornell University and Carnegie Mellon University develop AI programs. Importantly, the industry recognizes the need to train workers without college degrees in AI technology, as research shows these workers often have more optimistic views about AI adoption. The technology is also helping improve work-life balance by enabling planned maintenance during regular hours instead of emergency calls, making manufacturing jobs more attractive to younger generations.
Empower Existing Talent With Upskilling
Upskilling existing workers has become crucial in this AI transition. The article emphasizes that successful AI implementation requires intuitive technology that solves real problems for site teams. When workers see clear value in the technology, they’re more likely to embrace training opportunities.
This cultural transformation not only improves operational efficiency but also helps retain talent by creating new opportunities for strategic thinking and career advancement.
Find The Right Tech Partners – And In-House Mentors
Saar concludes the article by advising manufacturers to act now and partner with appropriate technology experts for successful AI implementation. Another essential step includes involving experienced team members in upskilling and mentorship programs. While AI can address the talent shortage, its broader benefits – such as increased factory capacity and improved production – can only be realized if factory floor workers have proper AI exposure and proficiency.
This technological evolution represents a crucial step for manufacturers to remain competitive while addressing the industry’s pressing workforce challenges. It’s a truly win-win scenario.
Read the full article at Forbes: ‘The AI Revolution With Grease Under Its Fingernails’.