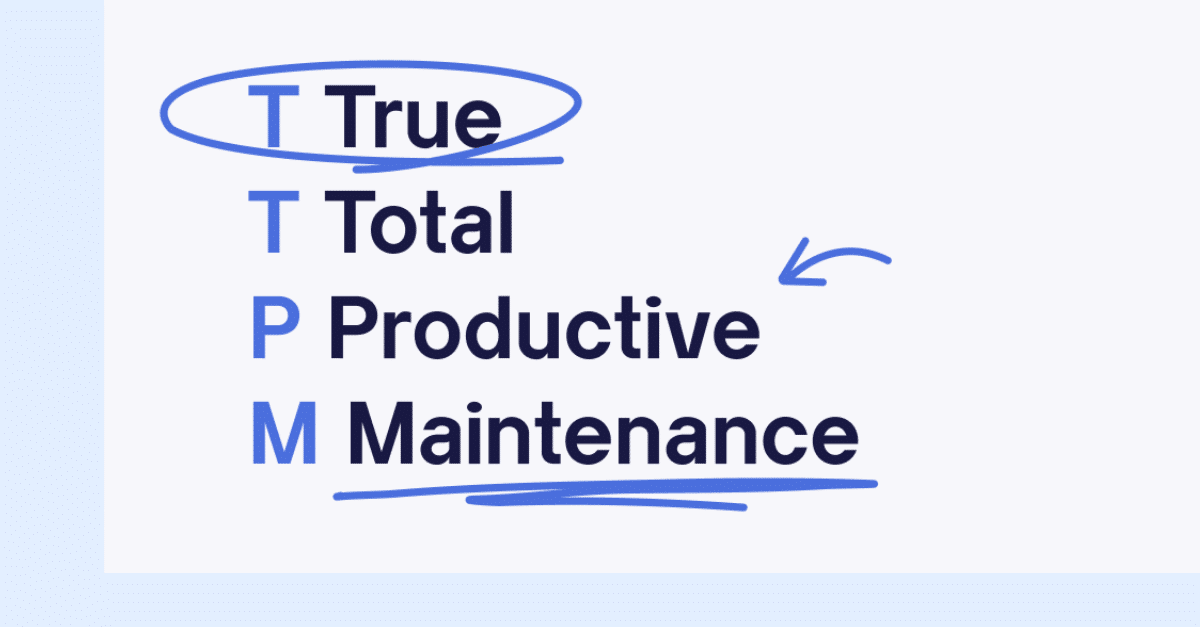
The journey to perfect production has long been a challenging quest for manufacturers. Total Production Maintenance (TPM) has been a path for many – and many get lost. But now, finally, the knowledge and Industry 4.0 tools exist to make it viable, according to James Newman, Augury’s Principal Solutions Evangelist. A Production Health approach is set to be the unlocking agent for helping organizations empower their people to work ever smarter.
The journey to perfect production has long been a challenging quest for manufacturers. Total Production Maintenance (TPM) has been a path for many – and many get lost. But now, finally, the knowledge and Industry 4.0 tools exist to make it viable, according to James Newman, Augury’s Principal Solutions Evangelist. A Production Health approach is set to be the unlocking agent for helping organizations empower their people to work ever smarter.
A Short History Of Continually Making Manufacturing More Efficient
Once upon a time, a statistician named William Edwards Deming observed the United States’ remarkable ability to rapidly build a comprehensive war machine fueled by innovative industrial practices – including preventative maintenance.
“Companies like Toyota embraced Deming’s innovative ideas while adding their own special sauce: continuous improvement and employee engagement.”
After WWII, Dr. Deming was sent to Japan to help rebuild its manufacturing industry and thereby help steer it away from communist influence. With the country leveled, the Japanese were willing to think outside the box. Companies like Toyota embraced Deming’s innovative ideas while adding their own special sauce: continuous improvement and employee engagement – including the somewhat radical idea of empowering operators to perform routine maintenance on their own machines.
Spreading The Love
Japan became a manufacturing powerhouse and began offering its learnings globally. Seiichi Nakajima crystallized these ideas in his seminal book Introduction to TPM: Total Productive Maintenance (1988), which introduced the now-famous Eight Pillars: Autonomous Maintenance, Planned Maintenance, Quality Integration, Focused Improvement, Early Equipment Management, Training and Education, Safety and Environment, and Administrative TPM.
TPM became the gold standard for operational excellence – demonstrating how maintaining machinery required a holistic, scalable approach that transformed entire organizations.
The missing ingredient? Comprehensive, real-time information.
Why TPM Fails: It’s More Than Just Machine Care
While some companies succeeded with TPM, many more stumbled. Alternative approaches emerged to better suit European and American cultures: 6 Sigma, Lean, etc. Yet most organizations, regardless of their success with these principles, eventually hit a wall.
The core challenge wasn’t technical but human: truly engaging employees and transforming company culture. The missing ingredient? Comprehensive, real-time information. TPM assumed everyone had the necessary data to make optimal decisions. Reality showed most manufacturers operating with fragmented, incomplete information.
The “T” in TPM stands for Total – assuming everyone has the information needed to make the best business decisions at any time. Meanwhile, the “M” for Maintenance is actually a misnomer. It’s not just about maintenance. Nor is it about maintenance and operations. Ideally, you also want to know what’s happening in downstream and upstream supply chains. Basically, you want to know everything that might influence making the best decision, no matter how seemingly trivial.
Enter Industry 4.0: The TPM Enabler
The rise of Industry 4.0 technologies has finally created the infrastructure to realize TPM’s full potential. Smart sensors, IoT devices, and advanced analytics provide unprecedented visibility into manufacturing operations. When employed correctly, the benefits quickly reinforce TPM’s Eight Pillars: improved OEE, enhanced quality and productivity, increased safety, improved knowledge transfer, a truly empowered workforce, etcetera.
But we can’t repeat past mistakes: you must take your people on the complete journey.
“It’s about escaping multiple myopic views and creating a panoramic perspective.”
Uniting Silos And Going Panoramic
At Augury, we’re building a complete Production Health ecosystem to enable True TPM (TTPM) – providing information at the right time so the right people can make the right decisions. It’s about escaping multiple myopic views and creating a panoramic perspective.
It begins with our bread and butter, Machine Health, helping solve maintenance issues. But that’s not enough. So we’ve established Process Health to help Operations optimize processes and outcomes in real-time. Still not enough.
“When maintenance managers make decisions, they’ll do so with the complete context of their line or plant’s activities.”
The next horizon, Fusion Diagnostics, solves the interface between Maintenance and Operations, bringing them together on the same screen – a TPM step change. When maintenance managers make decisions, they’ll do so with the complete context of their line or plant’s activities.
Yet this, too, is just part of the journey… Decision-making will only improve as the Production Health platform grows – incorporating new partners, capabilities, and data streams. Each addition becomes another stepping stone to TTPM.
While achieving the perfect factory might not be realistic, in the spirit of continuous improvement, we can at least get closer every day.
What do you think? Are you ready for the big picture? Are you ready to achieve TTPM? See all the ways Augury is doing it differently.