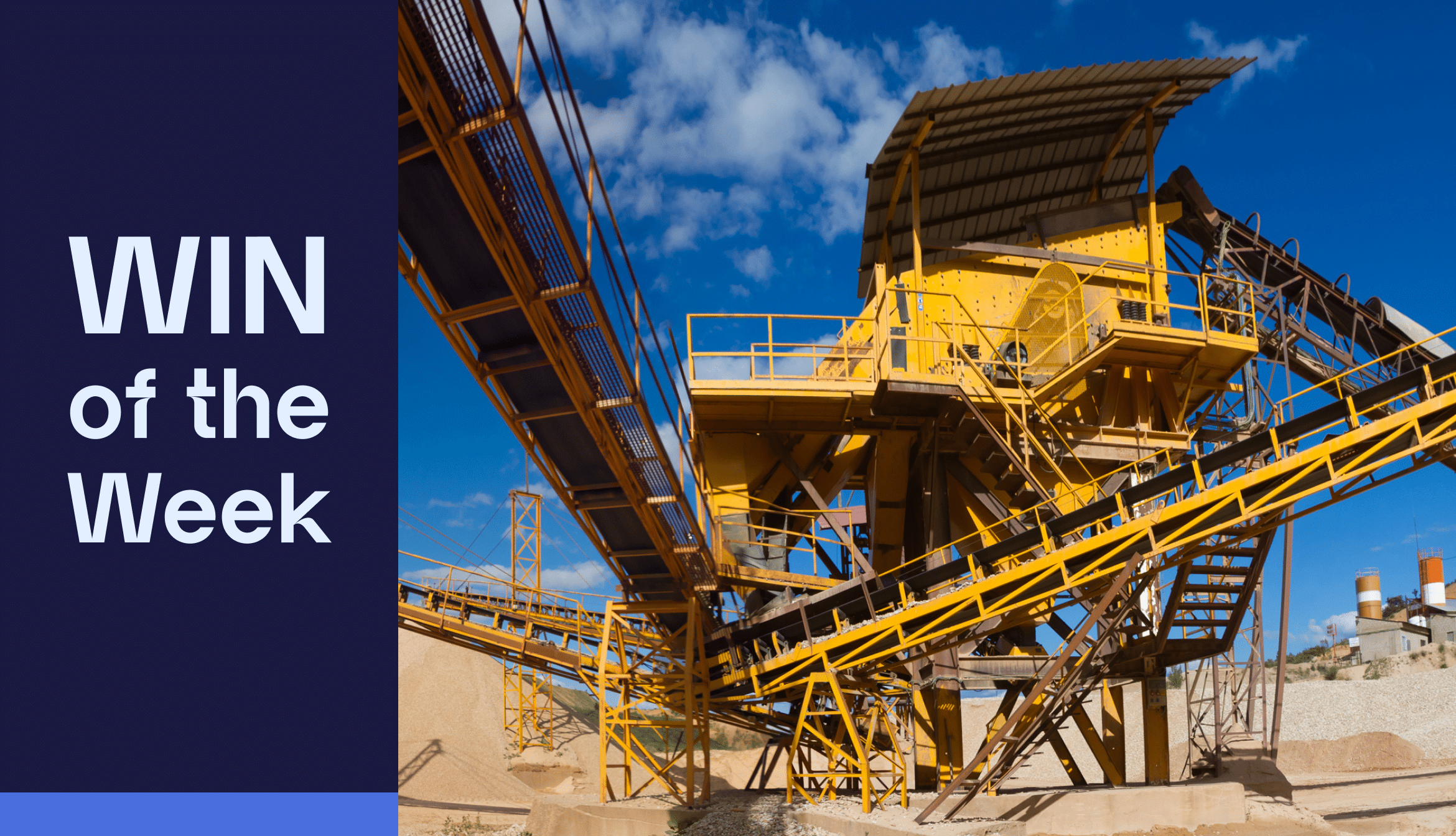
“Issues and disruptions we thought were inevitable, we now know are avoidable with Machine Health Ultra Low. This changes everything.” -Regional Reliability Engineer, leading metals and mining manufacturer
Industry – Metals and Mining //
Machine – Rotary kiln //
Fault Type – Impacting //
Big Machines, Big Risks
For a leading metals and mining manufacturer—a provider of sand and sand-based products—keeping their massive operations running efficiently is highly dependent on industrial kilns. These giant, high-heat machines that process minerals and ores are the backbone of production, and when they fail, everything grinds to a halt.
Because these industrial kilns operate at extreme temperatures, they rely on a critical layer of refractory bricks to prevent structural damage. Kiln failures, and even other more minor issues, can lead to catastrophic downtime that’s costly for the business. This puts enormous pressure on maintenance teams, who are tasked with repairs when something goes wrong but also with monitoring the machines to head off problems before they impact production. Complicating matters is the fact that traditional vibration monitoring is ineffective on such equipment, due to the kilns’ extremely slow rotation speed—sometimes reaching 20 RPM or lower—leaving teams to rely on thermal imaging, which is a lagging indicator that often detects problems too late.
“When a kiln goes down, it’s not a quick fix,” explained the manufacturer’s Plant Manager. “We’re talking days or even weeks of lost production, impacting everything from supply chains to revenue.”
Innovation Leads to a Smarter Way to Monitor Ultra Low RPM Equipment
Looking for a new approach to the costly problem, the manufacturer partnered with Augury. Its Machine Health Ultra Low solution—an innovative, industry-first approach to monitoring slow-moving, mission-critical equipment—uses structural ultrasonic sensors and AI-powered algorithms to detect issues earlier than ever before in equipment operating at extremely low speeds (down to 1 RPM), where traditional methods fail. Instead of waiting for visible signs of damage, maintenance teams can leverage Augury technology to capture subtle ultrasonic shifts before failure happens.
A Game-Changing Moment
Not long after the solution was installed, Augury sensors detected unusual impacting patterns inside one of the kilns—an early warning that the refractory’s bricks were coming loose. The maintenance team ultimately confirmed what Augury’s Machine Health Ultra Low solution had identified and remedied the potentially catastrophic issue. Because no other system (including thermal imaging) was able to detect the malfunction, the manufacturer’s experience with Augury proved that early intervention is possible for ultra low RPM machines.
The company and the maintenance team now have the insights and the confidence they need to prevent future shutdowns. “Issues and disruptions we thought were inevitable, we now know are avoidable with Machine Health Ultra Low,” remarked the company’s Regional Reliability Manager. “This changes everything.”
Better Together: A Partnership that Strengthens an Industry
While the manufacturer is seeing positive impact from this partnership, the deeper power of the success story goes beyond one company and will serve as a blueprint for the entire industry. The combined efforts of both companies show how predictive AI is unlocking new ways to eliminate risk and increase uptime, and lessons from one kiln’s near failure is shaping smarter, safer operations across the sector. Plus, the manufacturer’s leadership in embracing AI-driven maintenance to page the way for a more reliable, efficient future.
“We’re not just fixing problems,” said the Director of Maintenance and Reliability, “we are changing how the industry thinks about reliability.”
Learn more about Augury’s Machine Health Ultra Low solution.
Want to learn more? Just reach out and contact us!