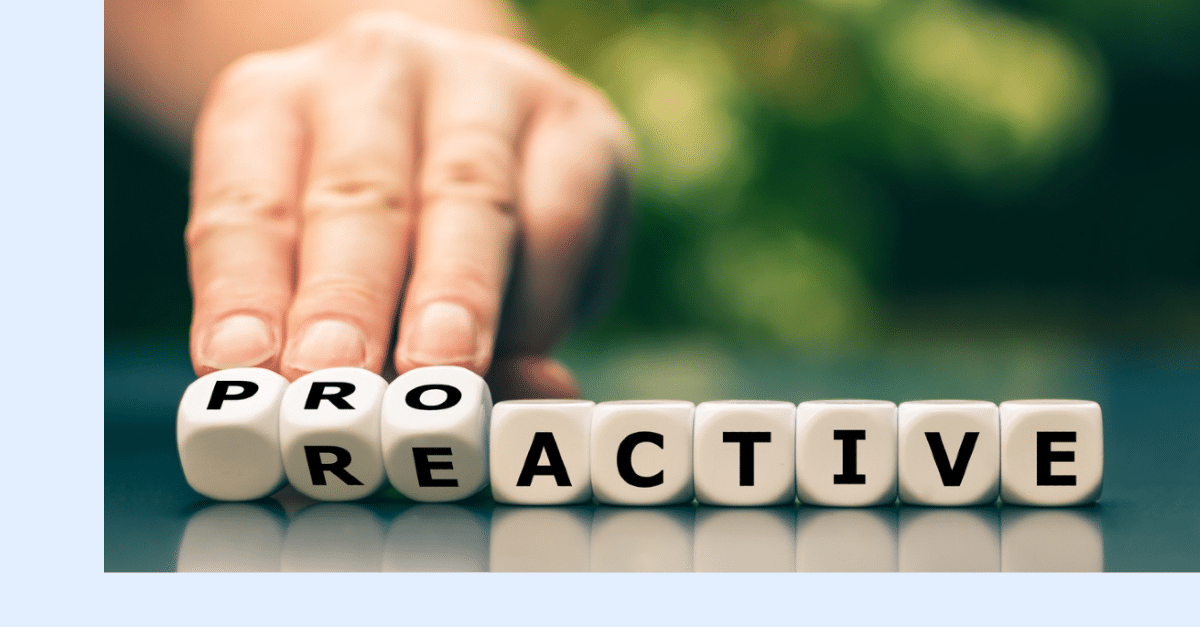
In a world of supply chain disruptions, labor shortages, and volatile markets, manufacturers face one thing that is certain: uncertainty. Yet within this unpredictable landscape, one strategic decision offers a rare island of stability—shifting a larger share of your non-critical assets from reactive maintenance to a continuous condition monitoring system. While markets fluctuate and consumer demands shift, the laws of physics governing your equipment remain constant and predictable. Happily, proven IoT tools now allow you to get aboard the PdM train in a much cheaper (and jargon-free) manner—with immediate benefits that only amplify with age.
Looking To Enhance Agility And Resilience?
When juggling competing investment priorities, predictive maintenance often resembles that ambitious home renovation project you keep meaning to start—recognized as valuable but perpetually postponed. Yet unlike that kitchen or garage makeover, this particular procrastination is quietly draining your P&L statement every quarter, and driving you evermore into tech debt—all those aging systems and habits that only make it increasingly difficult to get ahead, the longer you maintain them.
Read ‘Manufacturing – The News: How Do You Deal With A Wacky World?’
Happily switching a more significant proportion of your assets to predictive has never been easier. It is now a well-worn path by manufacturers who have recognized the fiscal and strategic value of breaking away from what financial analysts might call a “high-risk maintenance strategy”—otherwise known as “wait until it breaks”.
And yes, a rainbow of vendors offer all-in shiny solutions. But you don’t have to chase them all. Look at it more as an evolution than a revolution by focusing and prioritizing your own specific problems that you want to solve. Then see who has the best solution for your particular needs and price class.
Count The Many Ways Money Gets Sucked Away
But let’s backtrack a bit first… We all know the numbers around sticking to reactive—especially when it comes to downtime. It’s estimated that unplanned downtime is costing the process industries about $1 trillion per year in lost production and revenues,” according to a report from ARC Strategies. Another report states that $3.3 billion in waste is created through unplanned downtime alone due to defects in product. Won’t this money be better spent on dealing with whatever curveball may be coming around the corner?
“Within just eight months, we achieved a 2.5x payback, significantly reducing downtime and maintenance costs. The decision to scale this solution across our 16 plants was a no-brainer, given the impressive results and the seamless integration into our existing systems.”
— Director of Manufacturing Intelligence Systems, Home and Security Product
But there are other numbers… Relying on reactive maintenance on your noncore assets doesn’t just cost you during breakdowns; it’s more like a cascading financial virus that spreads throughout your operation:
- The “Just in Case” Inventory Cache: One study found that companies that move beyond reactive mode see the costs of inventory hold go down 20-50%, turning dusty working capital into shiny returns.
- The Overtime Epidemic: Reactive organizations spend 2-5 times more on maintenance labor than ones following a more proactive methodology. Remember those weekend emergency repair premiums? Fun times.
- The Energy Efficiency Gap: The U.S. Department of Energy found that properly maintained equipment uses 7-15% less energy. Don’t you already pay enough taxes?
- The Customer Apology Tour: Reactive organizations experience almost 4 times in lost sales. And, what are your contractual penalties when you miss a delivery? These aren’t just financial penalties; they’re reputation penalties with compounding interest.
- The Quality Tax: Research shows that sticking to reactive maintenance translates into 16 times more defects. Ouch.
But enough depressing numbers. Here’s a happier one: predictive maintenance can slash machine downtime by 30-50%.
“This not only helped make improvements across other plants, but also helped me build relationships with my peers from across the country and globe.”
— Maintenance & Processing Planner, Global Snack Manufacturer
Predictive Maintenance Is Not A Ponzi Scheme
The most successful investors look for investments with sustainable competitive advantages. Hence, they would naturally be all-in on a predictive maintenance solution since properly executed programs can result in up to a 5-20x ROI. (And no, PdM is not a Ponzi scheme.)
Do the ROI math for your own facilities.
These returns materialize through multiple value streams—both measurable and more ephemeral—that would make any private equity firm salivate:
- Maintenance Cost Reduction: Research shows that organizations implementing predictive maintenance reduce maintenance costs by 10-40% compared to reactive strategies.
- The OEE Opportunity: Countless studies show a significant improvement of OEE improvements following implementation—essentially “unlocking a whole shadow factory”.
- Asset Longevity Bonus: Moving beyond reactive maintenance can extend machine life by 20-40%. Who can’t love the equivalent of free machines?
- The Sustainability Lift: With 10-20% less waste compared to reactive approaches, this is not only good for the bottom line, but also the planet—and we like both.
- Workforce Enablement: This is a harder metric to measure but one that contributes heavily to a company’s success. We all know a happy and engaged worker is a more productive worker. No math needed.
- Untangled Supply Chains: Predictive maintenance creates production stability that enables more reliable forecasting, inventory optimization, and on-time delivery performance. One study shows the switch increases supply chain optimization by a third.
The Competitive Edge That Keeps Giving
While ROI and cost savings get attention, the strategic advantage may be most compelling. Studies show manufacturers with mature predictive maintenance capabilities respond much faster to market changes and new product introductions than competitors relying on reactive maintenance.
Remember, in these crazy times: agility is a competitive advantage.
Portfolio Performance: Case Studies From the Field
Skip the theoretical and let’s look at the real world:
- The Food & Beverage Home Run: PepsiCo avoided over 4,500 hours of unplanned machine downtime across over 900 downtime events in 38 Frito Lay manufacturing sites.
- The Chemical Touchdown: In less than a year, DuPont achieved 7x ROI at their proof-of-concept sites and is continuing to improve operations by rolling out a Machine Health solution across all their businesses.
- The Consumer Packaged Goods Slam Dunk: Colgate-Palmolive saved 2.8 million tubes of toothpaste by avoiding a single machine failure.
“The benefits of having real-time access to machine health analytics have been so powerful, we’re going to roll out this technology across our global supply chains.”
— VP of Global Engineering Services, Colgate-Palmolive
To have your own solid success story, you need to implement without breaking a sweat or the bank. Happily, the most speedy and successful implementations follow a typical pattern—like the vibration of a misaligned machine.
Fast Track Mavericks on rapidly scaling digital innovations across an organization:
Dave Penrith: ‘If People Feel Safe, They Fly’
Alvaro Cuba Simons: ‘Be Open. Be Curious. Bring The Best Of Yourself To The Team
Scott Reed: ‘Going Beyond The Firefighting And Really Solving Something’
“In just a few months, we reduced waste by 37%.”
— VP Global Technical Development, Food Manufacturer
Certainty in Uncertain Times: The Only Logical Path Forward
For manufacturing leaders evaluating maintenance strategies, the key questions revolve around not if but when you increase the percentage of assets from reactive to predictive. By focusing on specific operational challenges, selecting appropriate technologies, and developing the necessary organizational capabilities, companies can realize significant operational and financial benefits while building more resilient manufacturing operations.
While the physics underlying equipment failure remain consistent—bearings fail in predictable ways, vibration patterns reveal developing issues, and early intervention prevents catastrophes—organizational capabilities may need time to develop. So, initially, a measured, strategic approach typically yields better results than rapid, comprehensive deployment.
However, once trust and confidence in the technology is established: “Nobody said you can’t move fast”—in the name of improved business outcomes and enhanced agility.
Let’s do this.
Read more about how Augury is a leader in post-reactive maintenance.