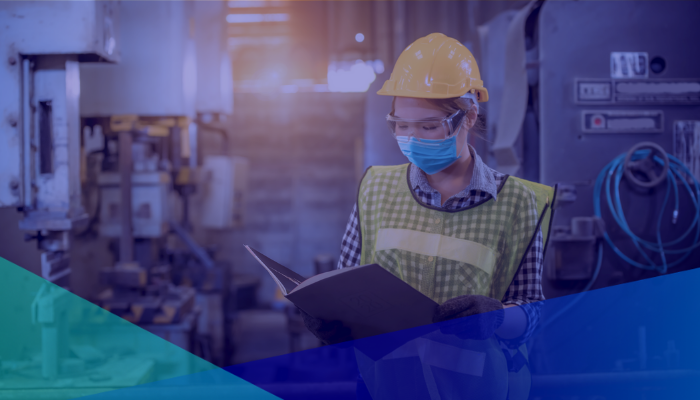
It’s safe to assume that every company wants the maintenance performed on its production and manufacturing equipment to be precise. After all, who would want imprecise maintenance? But assuming that maintenance is being performed to the highest standards possible and actually taking the steps to assure that it is are two different things. The difference in equipment performance can be night and day.
Let me give you the flat tire example. Imagine if all the tools you had to change a tire were a hammer, a pair of pliers and a rusty jack. Could you change the tire? Maybe… you could try to loosen the lug nuts by using the pliers and the hammer. The rusty jack might lift the vehicle enough to change the tire. You can use the hammer and pliers to tighten the lugnuts and hope for the best as you head down the road.
The “precision” approach would have the person use a proper lug nut wrench which would easily loosen the nuts. The correct jack would raise the vehicle safely until the flat tire could be replaced by the spare. The spare would be inflated to its correct pressure with clean, dry air and checked by a tire pressure gage. The lug nut wrench would be used to tighten the lugnuts in a star pattern to make sure proper seating and that the rim isn’t bent. Finally, a torque wrench would be utilized to make sure all the nuts are at the correct torque setting. Which tire do you think would run the longest without an issue?
Incorporating what’s come to be known as “precision maintenance” into a company’s standard operating procedures requires establishing and enforcing four basic criteria:
1. Training
First, technicians performing maintenance must be highly trained. Just explaining how a function is to be performed or merely showing someone what to do and then handing them the tools is not enough. Formal training in maintenance techniques and the particularities of each piece of equipment a technician will be working on are a must. For example, have you been taught that you should loosen lug nuts while the tire is still on the ground so the tire doesn’t rotate?
2. Best Practices
Second, best practices must be defined and followed. For example, there are many ways of tightening lug nuts when replacing a spare tire, but the established best practice is to tighten them in a star pattern. Similarly, each maintenance step to be performed should be outlined in a step-by-step way according to accepted best-practice procedures — or those that are developed and instituted for each job. These practices should also include specific settings or specifications. Under or over inflated tires can cause premature wear, poor performance and catastrophic failure.
3. Best Materials
Third, the best-available materials should be used for all work. This is where many attempts at precision maintenance run aground, either through attempts to cut costs or through complacency by failure to seek out and use the best possible materials and tools. For example, do you choose premium, contaminant-free lubricants or ones that merely meet requirements? Do you use laser-guided tools when high-precision work must be done or do you rely on a ruler? Do you mandate the use of calibrated torque wrenches or do you allow staff to use whatever tools they like? Most importantly, do you have procedures in place to ensure that the correct tools are being used for each job? Is the air you are using to inflate the tire clean or is it contaminated with water or other impurities that can cause premature failure? Did you use the correct size wrench or did you round out the nuts because you used a wrench that was “good enough”?
4. Maintaining Records And Having Data
Make the fix; move on to the next problem. That’s the general approach to maintenance on many plant floors. But without documentation of the fixes or changes, the reasons for them, and exactly how the changes were made, it’s difficult to improve a process and perform maintenance more precisely.
Many new technologies automatically collect data. Augury, for example, continuously gathers mechanical data from machines, uses it to automatically diagnose machine health and reports signs of incipient trouble. Incorporating that data into plant floor operations permits preemptive actions that make maintenance more precise, cuts downtime and often avoids more expensive and extensive repairs.
While precision maintenance has been discussed and its practices refined over the past decade, acceptance has been gradual for a variety of reasons. One factor is cost. Using better tools and higher-quality supplies involves greater upfront costs, even if there are savings in the long run. Another factor is time. Sometimes it takes just a bit longer to get the fix right, this may mean more downtime to execute the correct fix.
Another stumbling block is human nature. Maintenance people, like almost everyone else, are resistant to change. They like performing maintenance tasks in the ways they’ve always performed those tasks — especially if maintenance stays under the radar of those higher up the corporate ladder and doesn’t seem to cause any issues.
But with all the evidence confirming that high-quality manufacturing leads to more satisfied customers and greater profitability, it’s time that maintenance efforts adopt the same outlook. Like high-quality manufacturing, precision maintenance is essentially about reducing variability. And reducing variability in maintenance leads to greater production, more efficient use of equipment and capital, and greater safety. Think about this amazing stat: it takes an experienced pit crew less than 5 seconds to change a tire on a race car. Without question, they are following precision maintenance practices.
It’s time to get more precise.
Want to learn more? Just reach out and contact us!