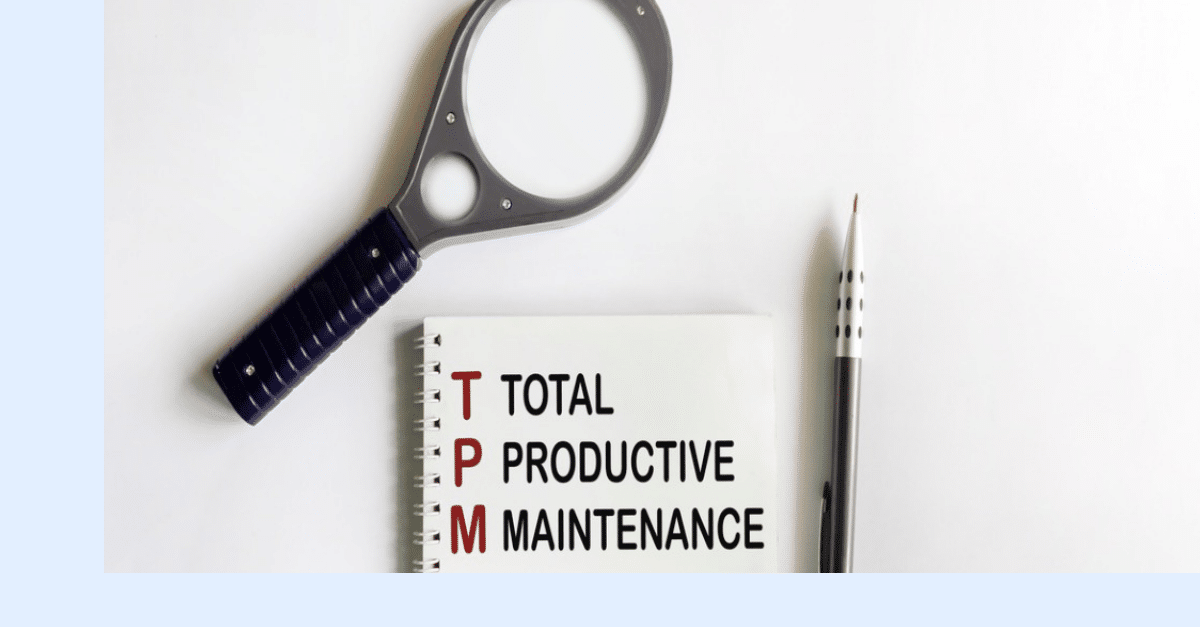
Many see Total Productive Maintenance (TPM) as a process to improve machine and operational efficiency by involving all employees in equipment care and improvement. But sadly, it doesn’t seem to work for everyone…
The Mixed Results of TPM Implementation
One of the things I love about my job as Solutions Architect at Augury is the engagement with customers across a range of industries. I’ve visited countless manufacturing facilities—from soda bottlers to pet food makers to building materials sites to ice cream packers to seeing big rocks made into little rocks. One common sight at these facilities is TPM program boards. Some are actively used, while others have clearly been abandoned—”zombie boards” collecting dust.
These abandoned efforts always make me wonder: what happened? Having seen TPM transform organizations, it’s disheartening to witness where implementations have failed.
My Journey with TPM
My interest in TPM began years ago as I was working at a Kimberly-Clark facility in Arkansas. We implemented the program to improve equipment health and appearance while engaging operators in maintenance. The results were remarkable. Seeing frontline operators empowered and supported by a formal steering committee process sparked my passion for TPM methodology.
As reliability and continuous improvement programs evolved within K-C, we morphed the concepts of TPM (Operator Driven Reliability, Focused Work Teams, Maintenance Excellence & Early Equipment Care) into new programs.
I was proud to help the LATAM region in Kimberly-Clark roll out the new reliability and continuous improvement initiatives to enable the frontline operators and leaders to improve the equipment health and the culture of the sites. We were able to achieve over $30 million in gross savings across the region using these programs based on the concepts of TPM.
The “Wow Moment” That Reveals TPM’s Power
My career’s most significant “wow moments” have come from watching frontline operators become engaged and empowered through TPM. When operators are fired up, equipped with the right tools, and supported by leadership, the transformation can be astonishing. I’ve walked into facilities a year after implementation and barely recognized them—the improvements were that dramatic.
Why TPM Succeeds or Fails: Critical Success Factors
Through years of experience, I’ve identified several key elements that determine whether TPM efforts thrive or wither:
1. Leadership Vision and Commitment
TPM cannot be a “flavor of the month” initiative. Leadership must demonstrate unwavering commitment to the process, viewing it not as an 18-month project but as a fundamental lifestyle change for the organization.
I often tell clients, “It’s no different than going to the gym. Whether you’re on a treadmill, lifting weights, or taking a class, it’s about creating healthier habits that last.”
2. Robust Steering Teams
Successful programs maintain active steering committees that:
- Keep efforts moving forward
- Remove barriers to implementation
- Celebrate wins to maintain momentum
- Provide a forum for operators to share improvements
3. Organizational Connectivity
TPM thrives when it connects the entire organization in collaborative problem-solving. Breaking down silos between operations, maintenance, engineering, and management creates powerful interactions that drive continuous improvement.
4. Maintenance Evolution
As operators take on more equipment care responsibilities, maintenance teams must evolve their practices to support this new dynamic. Without this evolution, the new ways of working quickly become unsustainable.
How Technology Enhances Modern TPM
Today’s TPM implementations can leverage advanced technologies like Machine Health monitoring to amplify results. Augury’s predictive maintenance solutions, for instance, fit naturally into TPM’s maintenance excellence and problem-solving aspects.
The data and insights from these systems help operators:
- Identify emerging issues before they cause failures
- Problem-solve more effectively with objective data
- Feed insights to equipment designers to improve reliability
- Make informed decisions closer to the work itself
The Human Element Remains Central
Despite technological advances, TPM’s power still comes from human engagement. As one plant manager told me, “The technology gives us better data, but it’s the pride of ownership that transforms how people care for equipment.”
TPM is fundamentally about giving operators and technicians the tools, authority, and responsibility to care for their equipment—creating a sense of ownership that drives performance beyond what management alone could achieve.
Beyond Appearances to Performance
A common pitfall in TPM implementation is focusing too much on how the equipment looks rather than how it performs. While clean, well-organized equipment is essential, we must remember the ultimate goal: “We don’t build equipment to look good. We want to run equipment to produce what it needs to produce at the most efficient level possible.”
Successful TPM programs balance appearance with performance metrics, using data to identify areas for improvement even after initial optimization.
The Path Forward
If your organization has struggled with TPM implementation, don’t abandon hope. Consider whether you’ve established the fundamental elements for success:
- Is leadership genuinely committed to the long-term journey?
- Have you empowered frontline operators and technicians with both responsibility and authority?
- Are you breaking down silos between departments?
- Are you balancing equipment appearance with performance metrics?
When these elements align, there’s nothing that will slow progress except perhaps poor leadership decisions. So get your frontline teams fired up about TPM, provide clear direction and the tools they need, and remove the barriers to enable the transformation to unfold.
Join the discussions at The Endpoint and share your experiences around TPM deployment. Where did it succeed? Or what caused it to fade away?
Or read about how Augury is making it easier to achieve true TPM.