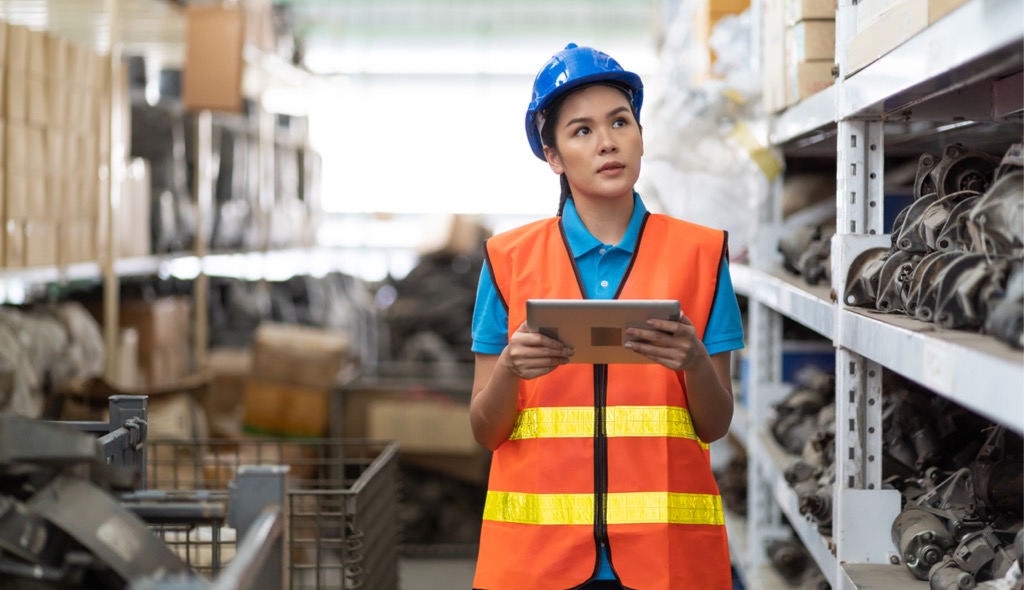
Supply chains will not get unsnagged anytime soon. As prices and shipping times continue to rise, it will only become more challenging to have the spare parts you need for the next scheduled maintenance. Happily, Augury customers can apply our long-view insights to have everything on hand to fix whatever needs to get fixed – on time, and without any unplanned downtime.
This article was originally published on June 16th, 2022. Edited on October 10th, 2023.
The Pain of Spare Parts Ordering
“Metal is horrible. It’s just horrible to get right now,” says the technical team leader of a large auto-related manufacturer in Europe. “In fact, it’s not just metal: the costs for all spare parts are exploding. It’s crazy.”
Spare parts delivery prices have more than doubled over the last two years, and lead times have ballooned to between 28 and 50 weeks. “And it’s only getting worse. It’s not just about Covid. Now there’s Ukraine. And then we had parts coming in from Russia that we can no longer get. It’s just getting more complicated.”
Meanwhile, most companies, including our auto-related manufacturer, have active policies to minimize the amount of on-site stock – especially when it comes to expensive spare parts like gearboxes. While this is a sensible approach to putting a cap on CapEx, it doesn’t make the technical team leader’s job any easier. “For each part, you have to factor in not only the increased costs of transportation and general price increases, but also where a part is coming from – or if it’s even still available at all. Again, I have to say: it’s crazy.”
Game-Changer Strategy: Agility Planning
Augury knows that “crazy” environments are no good for business. Now, by leveraging the insights from Augury’s Machine Health platform, the technical team leader can finally take control.
“Using the Augury platform, reliability teams can forecast spare part availability and plan their repair shutdowns months in advance,” says Shay Shitrit, the Customer Success Team Lead at Augury who is advising the team leader. “And if a particular machine shows an unexpected decline in health, we’ll be able to flag that fast, so the team can reschedule or change prioritization.”
Since Shay has already worked with another facility of the same manufacturer, he has plenty of best practices to share with the technical team leader. “Another great thing is how the Augury platform aggregates all the information and monitors your progress. For instance, we can track KPIs around shipments, lead-times, and spare parts and see how this relates to improved machine health over time,” says Shay.
Already, the other facility has seen a steady decline in a machine entering alarm mode. “And over time, we can also see what the most common issues are with particular machines – for instance bearing wear with mixers, or mechanical looseness with extruders,” says Shay.
By being aware of the potential problems and the timelines, reliability teams can be better prepared to fix these problems – in terms of spare parts inventory, maintenance scheduling, resource planning, and other outcomes. “And you’ll be able to do this in an efficient, justifiable, and predictable way,” adds Shay.
The Bigger Picture: Maintaining Competitive Advantage
We all know snags in the supply chain have a direct impact on revenue. As this and other supply chain challenges have become common talking points throughout the industry, many point to collaborating with a diverse set of partners as a viable way forward. But we should also be looking at supply chain challenges as part of a larger issue.
“While Augury insights provide value by dealing with current supply chain challenges, this is nestled into our wider aim of extending asset life and avoiding catastrophic failures,” explains Shay.
“Spare parts management really falls under Augury’s focus on optimizing asset care – so machines have longer, healthier, and more reliable working lives. And a fundamental part of this approach involves avoiding any unnecessary over-maintenance that works to drain not only inventory but also your human resources,” says Shay.
“Optimized planned maintenance cycles allow for better forecasting that works to minimize supply chain costs. But they also help to keep deliveries to customers consistent, which means avoiding late penalties and loss of business.”
In short: the craziness stops here.
Read more customer success stories about getting the most of their machine health program.