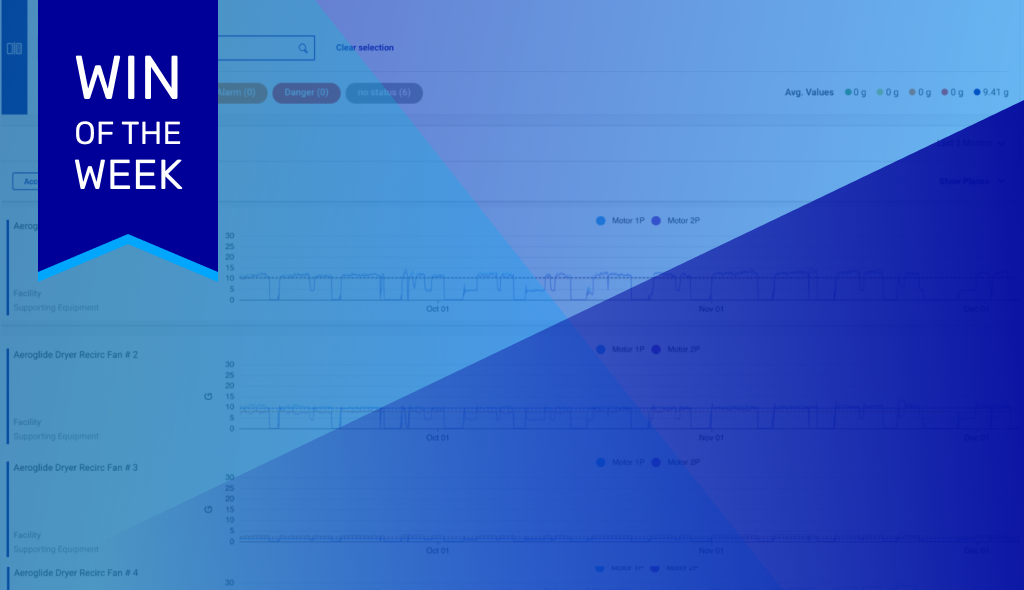
This second Win of the Week for Machine Health for Supporting Equipment (MH SE), features a well-known pet food manufacturer, which experienced an important win with Augury’s new product offering. The manufacturer is using MH SE to monitor several second tier assets, including a very large dryer. The dryer has six recirculation fans that move air to dry the pet food.
Industry – Pet Food //
Machine – Dryer Recir Fans //
Fault Type – Bearing Wear //
The recirculation fans are great candidates for Augury’s MH SE solution due to their hard-to-reach location and potential to fail risk implications. While losing one of these fans does not take down the dryer, it does hurt the machine’s efficiency – resulting in reduced output and potential quality issues that ultimately lead to loss of revenue.
Augury’s AI detected and directly alerted the onsite team of developing faults on not just one of the dryer’s fan motors, but on all six! Augury’s system indicated advanced bearing wear was the leading fault across each fan. The team reviewed the data from the Augury platform and recommendations to replace each of the motors. Such extensive repairs would naturally require planning and a large investment of time and money.
Image 1:
Machine Health SE’s user-friendly Compare Machines tool allowed the onsite team to compare Acceleration P2P on the motors for all six fans to determine the highest priority repair.
Image 2:
Detectors Confidence level (fault probability) for bearing wear at the time of the alert was over 85%. Post-repair, vibration and detector confidence levels returned to normal (around 25%), confirming the success of the repair.
With M&R resources stretched thin, the team decided to start with one fan to confirm the findings. They leveraged the easy to use Compare Machines tool in MH SE to help them prioritize which of the six fans needed to be addressed first. They prioritized the fan where Augury’s Detectors Confidence for bearing wear was highest. After replacing the motor the data showed significant improvement, verifying the issue and confirming the success of the repair.
With the early insights and guidance from MH SE, the team gained valuable time to order parts and schedule replacement of the five remaining fan motors during a planned holiday outage. To mitigate the risk of failure, they will likely replace all the motors at the same time, possibly hiring a contractor to save internal resources.
Without Augury’s MH SE solution in place, the site relies on operators to identify and counteract malfunctioning equipment in order to manipulate certain variables like heat and moisture to keep the line running. This introduces additional risks into the production process. In instances where this type of corrective action is not enough, the team is required to scrap whatever product is not up to the company’s quality standards. If all six fans were to fail and the dryer went down for 30 minutes, the site would lose 12,000 lbs of product – equating to $6,000 in lost revenue.
Augury’s findings across all six fans has prompted the facility team to explore if the issues are systemic and the best long-term maintenance plan moving forward. One possibility includes extending an existing mezzanine to make servicing these fans, which are located 15-18 feet in the air, quicker, easier, and more safely accessible when needed. Because of Augury’s insights across more of their equipment, the team is able to surface important health trends to determine the most cost-effective and impactful strategy.
Want to learn more? Just reach out and contact us!