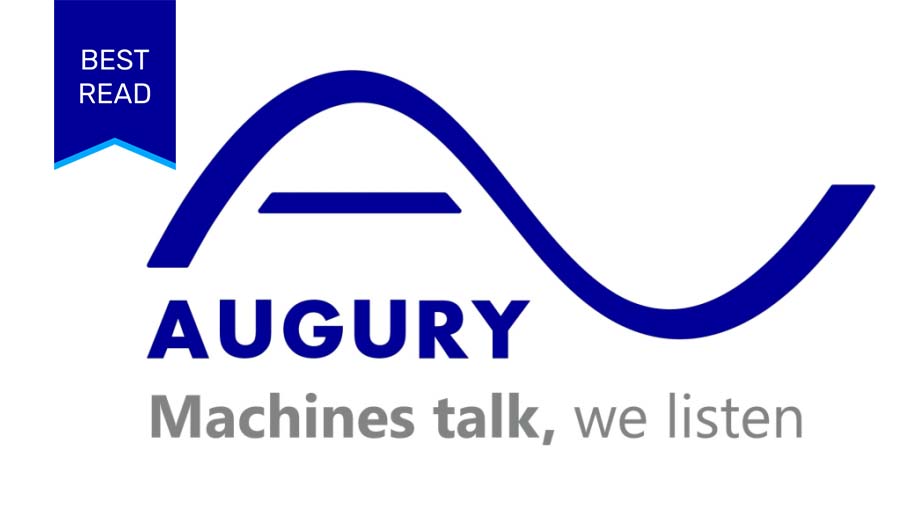
As a vibration analyst (VA) for Augury, Andrew Pry combines the practical with the theoretical: years of engineering experience across countless factory floors, backed by a Master’s degree in data analysis. He’s perfectly equipped to keep manufacturing machines running for the least amount of cost – and all from the comfort of his home. “Actually, Augury’s tech takes me directly to the factory floor. I still get to use all my senses as I dive into the data.”
This article was originally published on March 29th, 2022.
Andrew Pry apologizes for being less than two minutes late for our Zoom chat. Obviously, he’s a precision-oriented guy. “The clock I checked earlier had stopped. I’m guessing the batteries are low. And funny enough, this situation is sort of the story of my working life,” says Andrew.
“It’s very much like condition-monitoring. Say there are four clock batteries and only one is empty. I can find the empty one using a battery tester and replace it. Most people would just throw out all four batteries and replace them all. I just replace the one – and that’s kind of one part of what Augury does,” explains Andrew. “But yeah, my girlfriend still thinks I’m crazy for owning a battery tester,” he chuckles.
It’s safe to say Andrew brings the office – or rather: the factory – home with him.
Optimizing Factories From The Comfort Of Home
In fact, as a vibration analyst for Augury, Andrew is monitoring the vibration on rotating equipment – as well as other factors such as temperature and magnetic fields – from the comfort of his home. He also does very more than telling you whether a battery is dead or dying. He tells you exactly when an element of your manufacturing machine will die and why – so you can work to prevent your machine from stopping when you need it most.
Previously, Andrew was a manager at a pump company’s monitoring center. “But when a coworker told me about Augury, I looked into them and saw they were doing it a lot better than where I was at. So, I decided to take a demotion and jump ship.”
Originally, Andrew entered manufacturing after being a submarine officer in the US navy. “I wanted to get my hands dirty so I became a Control Room Operator. I did 12-hour shifts, alternating days and nights, over a couple of years. I am certified to operate 18 different plants around the US. So, I did learn a lot of different systems. But at one point I started looking for a change.”
Deep Dive Into Data
Andrew decided to go into reliability. “That’s when I really started learning vibration. I’d go into the field with a bunch of equipment and conduct tests over an afternoon, a day, a week or a couple of weeks. And then I’d take all this data home to study it to see where customers could get more value. And I really enjoyed that.”
But he also always knew this kind of data collection had an end-date. “At one point, condition monitoring would become more about collecting a lot of data points constantly – and analyzing that. It would stop being about manual collection. That’s why I wanted to move in this direction of data analysis. So, a few years ago, I enrolled in school and last fall I got my Master’s degree. The passion just keeps growing.”
I am still getting to use all my senses. Except for taste, which is fine by me.
On The Floor With Augury
But doesn’t he miss the hands-on work? “At first, I missed the little things like how a machine sounds. But then Augury came along. It’s part of our platform. I can actually press play and listen to a clip for a few seconds while already zooming into the data and starting my analysis. It’s like how I used to troubleshoot a pump in the field: start by listening to it. Plus, people on site can share their observations and pictures. So, I am still getting to use all my senses,” says Andrew. “Except for taste, which is fine by me.”
Since he can no longer derive job satisfaction from fixing the problems himself, he now gets it from seeing the customer realize how much value they are getting. “At first, they might be sceptical – or just following orders from above. But at one point, they always get excited. And there’s another aspect for my job satisfaction: having some pride in knowing that keeping these machines running is important for society.”
At one point you do need to get very hands-on with the assets. Only then can you really appreciate them in a hands-off manner.
Hands-On To Be Hands-Off
The job of an Augury VA is not just about continual monitoring but also continual improvement. “Yes, I review data to help the customers. But a big part of my job is actually looking at the data and sending precise feedback to our algorithm team so they can use this to help us predict better in the future,” says Andrew.
So, what exactly makes a good VA? “You want to be a good engineer and make sure what you are saying is correct. Patience and wanting to explore are also key. You also need to be able to explain your findings in a way that makes sense for people who might not understand vibration,” says Andrew. “Most importantly, at one point you do need to get very hands-on with the assets. Only then can you really appreciate them in a hands-off manner.”
Our chat time is over. Andrew waves goodbye – with his battery checker in hand.
Read the rest of the ‘Life of a Vibration Analyst’ series:
‘Aiming to Be Obsolete: Behind the Scenes with Augury’s Manager of Reliability Operations’
‘A Trade Transformed: 20 Years Of Vibration Analysis’
‘A Fitbit For Machines: With Vibration Analysis, The Goal Is To Extend Life’
Or learn more about Augury’s machine health and reliability solutions: reach out!