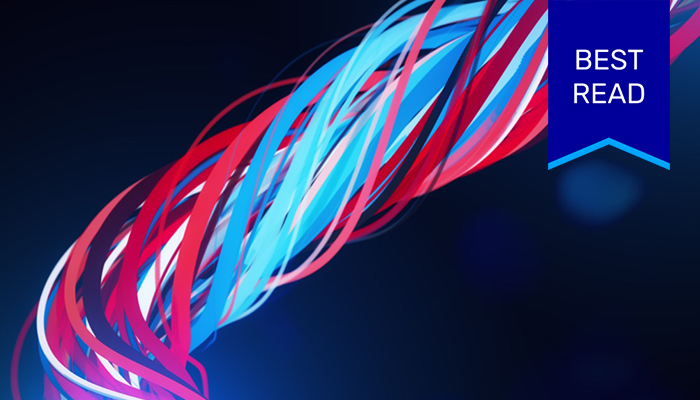
Colgate-Palmolive’s Gary Binstock has a vision to leverage his company’s ambitious machine health program not only to cut costs and amplify quality but as a springboard to a fully digitized manufacturing universe. “Once we have everything connected in one digital thread, the sky will be the limit.”
This article was originally published on 31 August 2021.
The Colgate-Palmolive Company was an early adopter of predictive maintenance. “When the opportunities of AI and IoT became apparent around four years ago, we started looking into it,” says Gary Binstock, Director of Technology for Strategic Innovation and Alliances. “And it set us on a journey…”
In a recent interview during Worldwide Business Research’s Connected Manufacturing Forum virtual event hosted on April 6-7, 2021 with Senior Conference Producer Maureen Azzato, Gary outlined his company’s path as they set out to improve supply chain reliability by promoting machine health for their manufacturing equipment.
“There’s already an acceptance and it’s being used by the people on the floor. But there are also higher-level expectations of how we can integrate with the rest of our systems to create a full digital thread,” says Gary. “And that’s still an ongoing job.”
Seeing Is Believing
Originally, Colgate-Palmolive started with a few slightly different use cases. “We had some quick wins right off the bat with Augury in this one facility with around 40 machines. We found a big event almost right away. If it had happened, we would have been down for a very long time and really impact our operations. And this became a very well-publicized story,” recalls Gary.
“So, getting these wins up front and early is very important. The news spreads like wildfire around the company. People start saying, ‘Hey that’s neat, we need that at our facility!’”
“Of course, we were also collecting KPIs from the beginning, and not only on whether we prevented equipment failure. We also covered time to reaction, time to getting a notification, time to taking action… We’re tracking all of those. And once we saw they were all tracking the right direction, it gave us the confidence to move forward,” says Gary.
Innovation and Domain Knowledge at Scale
Early on, Gary saw the advantage of teaming up with younger companies. “Originally, we tried to work with our legacy maintenance company to bolt on these IoT/cloud solutions but it didn’t work out. And in the end, it’s with these digitally-native companies we’re scaling with,” says Gary.
External parties can also bring in specialty knowledge. “Colgate is not an expert in these IoT techs. We also have very few vibration experts. And these parties are not only working with Colgate. They are working with energy, food, and many other sectors. We might have 10 mixers in a plant while they might be following 10,000. So, they are building domain expertise across all these assets. And that’s really powerful. They know how to set the triggers, train the models, and where to look for the anomalies.”
We’re leasing so they are doing all the heavy-lifting in that respect. And as a subscription service, it’s easy to standardize and easy to scale.
Gary also appreciates the bottom-line advantage of working with third parties: “Most of these companies follow a SaaS model, where there’s really very limited upfront capital. So, it’s fairly low-risk. All the hardware and related equipment – sensor, gateways, etcetera – are not owned by us. We’re leasing so they are doing all the heavy-lifting in that respect. And as a subscription service, it’s easy to standardize and easy to scale.”
Next Steps
Based on the proven benefits, Colgate-Palmolive continues to move ahead. “Short-term, we want to scale the vibration analysis network. There is power to connect it to all facilities,” says Gary. “You can look for anomalies not only at a particular unit but across units and see why one unit is not operating as well as another. And we can integrate this into our PM so we don’t have to rip apart equipment every half year.”
Currently Colgate-Palmolive is only applying the technology to their critical assets – the ones that are expensive or take a long time to repair. “We’re looking into how we can expand and add more and more assets. It’s ongoing work.”
Gary sees a time when sensors are inexpensive enough that all Colgate facilities and equipment around the world can be brought together into a unified data infrastructure. “Why not monitor everything?”
Towards Full Integration and the Great Beyond
However, he sees a time when sensors are inexpensive enough that all Colgate facilities and equipment around the world can be brought together into a unified data infrastructure. “Why not monitor everything?” says Gary.
“This idea of a digital twin is quite involved but very neat. Eventually we will be able to link all this machine data with lab data, visual data, environmental data – as much data as you want to pump in. And why not link all this to our workflows?”
“Eventually all the digital systems can be integrated. And once we have everything connected in one digital thread, the sky will be the limit.”
In short: onward and upward.