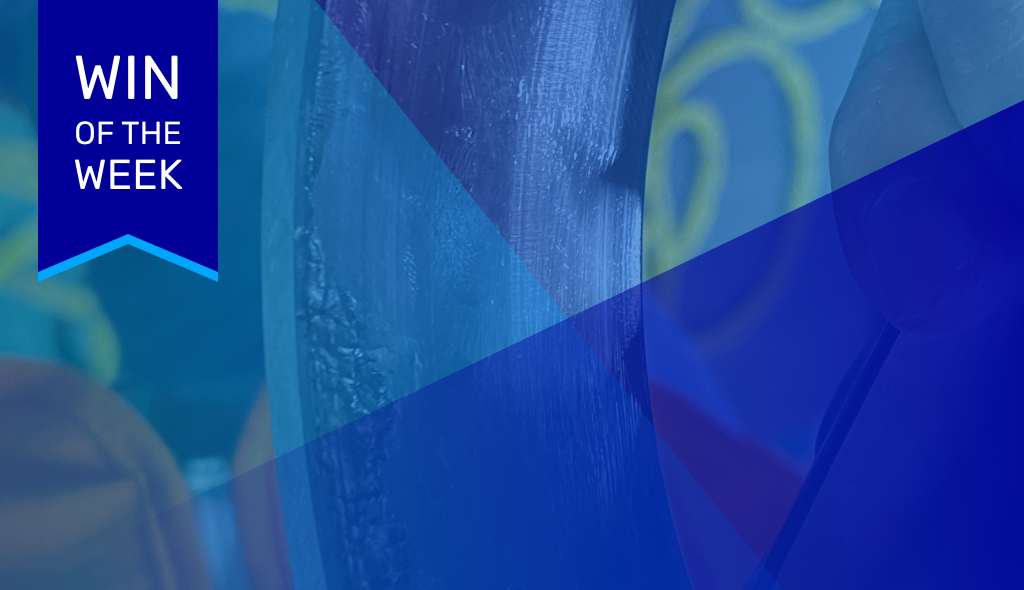
A busy maintenance and reliability team can’t be everywhere at once, especially one that is strapped for resources, but they can breathe a little easier knowing they can rely on Augury and their vibration analyst to monitor their critical machines for them 24/7. This Win of the Week highlights the important role an Augury vibration analyst played in supporting the onsite team at a leading pet food manufacturer in identifying and helping them prioritize the urgent repair of a critical extruder exhaust blower.
Image 1:
Machine Health status and alerts are tracked, logged, and visible to the Augury vibration analyst and on-site teams in the Augury platform as issues are detected and addressed.
The vibration analyst has worked closely with the manufacturer ever since they deployed the Augury solution, developing an excellent partnership with the onsite team and a deep understanding of their critical equipment and environment. He was aware that the blower’s normal velocity RMS was high and had set the machine health level to monitor the status. When Augury’s AI detected rapid increases in the axial vibration levels for the blower, which triggered two consecutive cliffs (rapid change alerts), the vibration analyst downgraded the machine’s health to Alarm then to Danger, and directly alerted the onsite team.
Image 2:
Augury’s algorithms analyze over 840 unique feature sets. Shown below are the Velocity RMS trends for fan shaft vibration as the machine’s health status changes from Monitor, to Alarm, to Danger (when two cliffs were triggered), indicating structural looseness in or around the driven fan.
Knowing the onsite team is understaffed with limited time, he emphasized to them that these new levels were unprecedented, recommending that they immediately check the fan for imbalance and structural looseness. The onsite team scheduled a planned repair, but when levels kept rising, the vibration analyst continued following up with them to ensure the repair had been performed.
When the team was able to record the repair in the platform, they reported finding a crack in the structural base of the blower. The base also supports a motor, which could have been impacted as well if the repair hadn’t been addressed so quickly. Post-repair, the blower axial levels decreased to previous normal levels, confirming the detection and the success of the repair, and the health status was returned to Monitor.
Image 3:
Following the recommendation from the Augury vibration analyst, the onsite team discovered a crack in the exhaust blower/motor mount (below, left) which they welded as quickly as possible (below, right) after completing a batch of product that was in progress.
Want to learn more? Just reach out and contact us!