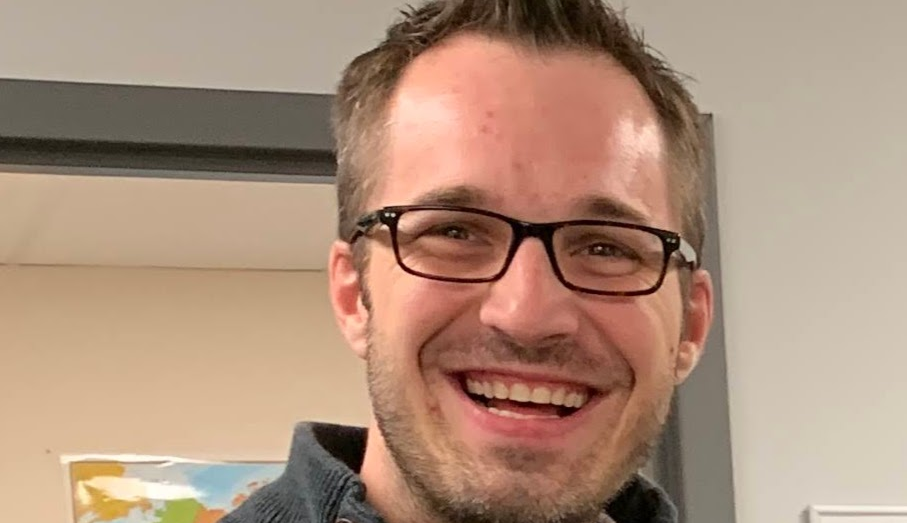
Henkel, the chemical and consumer goods multinational, has always been a pioneer. As Augury expands its partnership with this iconic company, we speak to Global Maintenance Engineering Manager, Tyler Beckett, about his varied career and how Henkel’s predictive maintenance program is pushing the company forward. “There’s always room for improvement!” enthuses Tyler.
Founded in 1876, Henkel is an established German company with beloved brands across adhesive technologies, beauty care, and laundry & home care. So, how does a 140-year-old company like Henkel discover and execute on manufacturing innovations internally?
In 2020, Henkel turned to Augury’s Machine Health platform for cutting-edge machine health monitoring service as a solution. However, it’s really employees like Tyler Beckett – Global Maintenance Engineering Manager at Henkel and outdoor-loving father of five – who drive innovative improvements.
Our team at Augury caught up with Tyler to learn more about his layered journey from academia to plant to corporate. And it certainly showcases what’s possible with an engineering degree – but that’s just the tip of the iceberg. While built on essential education and hard skills training, Tyler’s successful career and dynamic contributions to Henkel really demonstrate the power of drive.
Tyler, we’d love to learn about your background. Can you tell us how you got started as a maintenance engineer?
Tyler: Sure! Well, originally I had my eye on studying marine biology, but I switched majors and earned my Mechanical Engineering degree in 2008. Then I worked in Caterpillar’s transmissions facility for a few years before going to work at a university on an oil research project.
I was interested in making machines last longer through lubrication contamination control. My research consisted of burning fuel oil in a reactor, recreating the combustion conditions found inside land-based gas turbine engines. So, I collected and studied the morphology of the ash to determine how certain fuel additives reacted and affected the combustion characteristics.
Eventually, I realized I really preferred maintenance and engineering to academia, and that led me to Carpenter Technology Corporation. I found a job at one of their steel mills based in South Carolina. I worked there as a plant engineer for five years, eventually progressing to mechanical engineering and reliability manager. At Carpenter, I gained broad experience – from reliability and intensive lubrication work to machine design calculations, project management and heat treating.
So, what led you to Henkel?
Tyler: I loved living in South Carolina but wanted to move closer to the upstate area. I really like rock climbing and outdoor activities in the mountains. And so there’s a lot more of that there. When I started looking for a job in Greenville, I found Henkel.
I’ve had a three-pronged idea of where I’d like to see my career go: I wanted to work in manufacturing, which I did at Caterpillar, Inc. I wanted to work in heavy industry, which I did also during my time with Carpenter Technology Corporation. And next, I wanted experience in the chemical industry. That’s where I am right now at Henkel and I’m very happy.
When I was at Carpenter I wore many hats, including project management, machine and tool design, and reliability. I became especially interested in condition-based monitoring and predictive maintenance. So, I started with lubrication, which I was most interested in, and ended up earning three levels of certification in oil analysis and lubrication.
We took the plant from a zero state of lubrication and brought it up to regularly monitoring, sampling, and filtering 168 lubricated assets. This provided significant savings to the company. We didn’t have a single hydraulic or gear-based lubrication failure in the following two and a half years once the project was completed.
When I moved to Henkel, I continued to build upon the success I had at Carpenter Technology, but without the project management part.
Wow, so your role at Henkel is really focused in comparison.
Tyler: Yes, I was primarily focusing on maintenance engineering. I converted all the gearboxes to accept offline filtration and oil sampling. Then I began focusing on sustainability, working on our steam and compressed air systems. As part of that, I performed a compressed air leak survey and found $90,000 worth of air leaks.
The predictive maintenance work I was doing at the plant attracted the attention of the global maintenance team based in Europe.
We also acquired devices and equipment to enable us to perform precision alignment and motor/transformer testing and trending. The predictive maintenance work I was doing at the plant attracted the attention of the global maintenance team based in Europe.
In September 2019, Henkel asked me to apply for a global maintenance position. I applied, was offered the position and gratefully accepted it. The original plan was for me to provide global maintenance support to various countries and regions where Henkel has a presence. Well, I went to Europe for two weeks in January 2020 – and shortly after that, the world drastically changed.
Right, COVID-19. So what did the new normal mean for you in a role originally meant for traveling?
Tyler: Henkel has adjusted their outlook for flexible working locations due to the global pandemic, so I spend some of my time in a home-based office. Now, I provide webinars and training to global locations. This means I help plan and manage air leak surveys, lubrication modifications, and the Augury implementation, amongst many other things.
I’ve always had an interest in maintenance and a strong drive for it, which has helped me get to where I’ve ended up in my career so far. I have also worked hard to expand my knowledge through classes and certifications. That’s why I have earned the CRL, CMRP, steam trap surveyor, ultrasound level 1, and ICML certifications. I am currently working toward becoming Vibration CAT II certified.
I’ve always had an interest in maintenance and a strong drive for it, which has helped me get to where I’ve ended up in my career so far.
That’s so inspiring. What accomplishments are you most proud of in your work with Augury?
Tyler: I am very grateful to be able to partner with Augury in advancing our condition-based monitoring capability at Henkel. I am also pleased that our initial success has blossomed into being able to recommend Augury to other Henkel plants that have a need and/or desire to increase their predictive maintenance capabilities.
What’s next on your roadmap at Henkel?
Tyler: As far as my future journey with Henkel, I plan to keep pushing forward implementing predictive maintenance technologies and increasing awareness about the benefits of condition-based monitoring. There is always room for improvement!
We’d like to thank Tyler for sharing his story.
The constant desire to reach the next level pushes people, and the companies they work for, to grow. But when established businesses like Henkel decide to invest in talent like Tyler, a kind of rare magic happens: the best of traditional brands harness innovation to get even better.
Interested in learning more about how Augury is impacting Machine Health at other manufacturers? Check out our case studies.