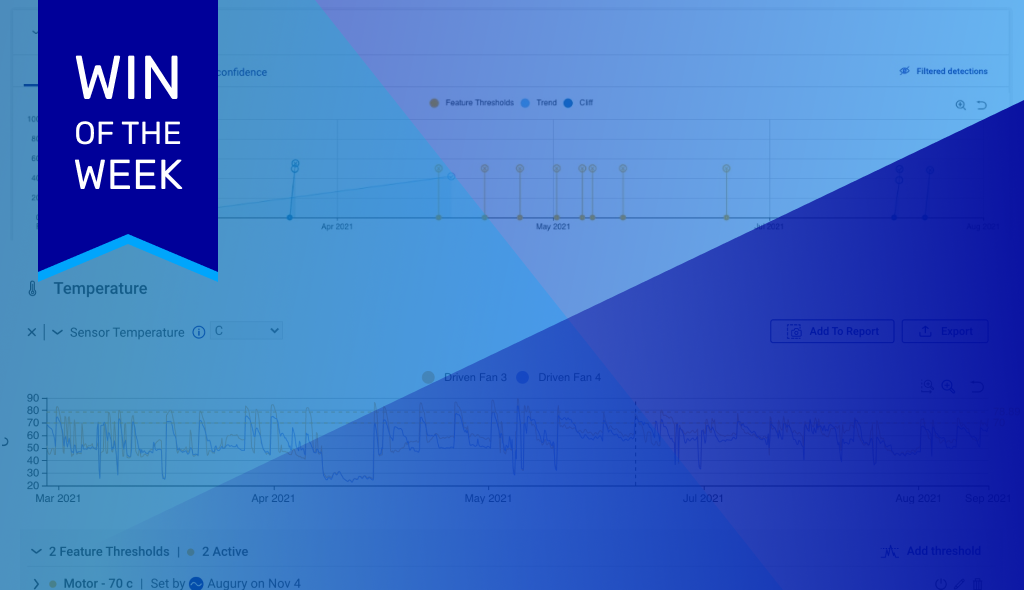
In addition to identifying the earliest possible signs that a mechanical fault may occur, findings from the Augury solution can also influence how a plant decides to perform its ongoing maintenance. This unique Win-of-the-Week highlights how Augury helped a global leader in plant-based ingredients and naturally-derived pharmaceutical excipients change the way it handles the weekly lubrication for one of its critical assets.
Industry – Food //
Machine – Exhaust Fan //
Fault Type – High Temperature //
Image 1:
Machine Health status, alerts, and communications between Augury vibration analysts and the onsite team are tracked and logged in the Augury platform as issues are detected and addressed.
In late May, Augury’s sensors detected increasing temperatures that were regularly surpassing the feature threshold assigned for the driven equipment, a dryer exhaust fan. While machine temperatures naturally increase during the summer months, Augury’s vibration analyst quickly recognized that a pattern had developed. Each Thursday, the temperature of the grease lubricated fan bearings on the fan was spiking to 193F — to the point where the grease could be burning. The vibration analyst set the Machine Health status to Alarm and alerted the onsite team, recommending that they check if the correct lubrication was being used on the lube routes.
Image 2:
Detections showing points in time when the asset temperature was regularly surpassing the feature threshold.
Upon further investigation, it was discovered that the temperature spikes correlated to the weekly lubrication schedule for greasing the fan. The lubrication technician then began experimenting with the amount and viscosity of lubricant, moving from ISO VG220 to ISO VG100. It took several weeks for the lighter weight lubricant to work its way down the grease tube, but the temperature decreased each week as the old lubricant was pushed out, ultimately reaching a stable, acceptable temperature of 171F.
Image 3:
Augury’s algorithms analyze over 840 unique feature sets. Changes in Temperature Sensor at time of the alert are shown below, as well as the subsequent downward trend once the lighter weight lubricant had been introduced.
The Machine Health status was adjusted to Monitor while the onsite team continued to fine-tune the amount and type of grease to reduce temperature spikes as a result of weekly maintenance. Given the successful change, the plant began applying the updated lubrication procedure to other dryer exhaust fans that could also benefit.
These temperature anomalies would never have been caught without Augury’s continuous monitoring and comparison to its vast database of machines in this category. Not only did Augury help prevent machine failure, the insights the customer gained from the solution enabled them to optimize the machine’s health, actually changing it for the better.