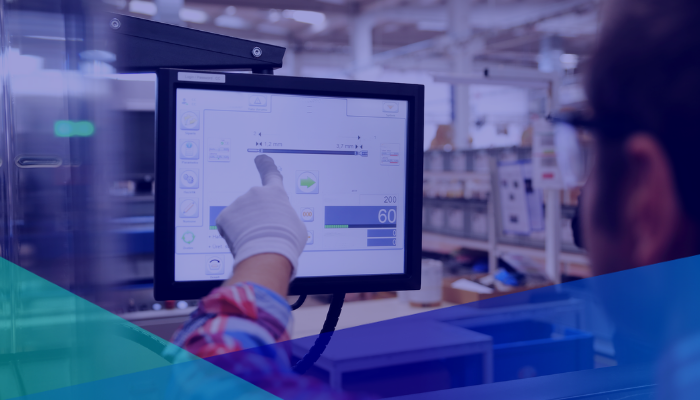
The modern world has seen machines transform every industry and nearly every aspect of developed nations’ economies. From effective production lines to speedy self-checkout registers in grocery stores and much more, people rely on technology so heavily that it has become second nature to them.
Yes, machines have become universal because they make human processes easier. However, they don’t eliminate the need for human interaction; after all, someone must still operate and maintain those machines. In most cases, it’s up to humans to determine whether a machine is performing under or over capacity and then devise a plan to optimize its behavior.
With manufacturing, in particular, machine optimization is about continuous incremental improvement. In fact, a single optimization goal might be as conservative as increasing output or reducing annual costs by just 1%. With that in mind, manufacturers must ask themselves this question: How can we make machine optimization as efficient as possible?
Most often, the answer is to use other advanced technologies and software — technology that provides precise, real-time machine health updates and operational data analysis.
Making the Most of Your Machinery Investments
Digitally driven machine health analysis is the logical evolution of our reliance on machines. Technology was always meant to maximize and speed up our own human capabilities. Ironically, a machine’s potential has traditionally been limited because it still depends on human input. After all, it can’t take care of or improve itself.
A company’s goal in investing in machines is to optimize as much as possible while limiting maintenance and repair costs and lost time. However, traditional methods of waiting to observe end-product quality or relying on human senses to identify root machine problems still cost more time and money than is often necessary.
On top of that, these metrics are only symptomatic indicators of poor machine health. They don’t necessarily identify the specific machine that needs to be maintained or what that maintenance should entail. Instead, companies should maintain machines based on fluctuations or changes in mechanical data (vibration, temperature, and magnetic) before the machine can significantly impact throughput and product quality.
Adding a layer of digital machine data analysis provides a deeper, more accurate understanding of how every machine operates and its overarching role in boosting your company’s performance. You can know what your risks are at any given moment in terms of asset availability and capacity or use that data to make instant adjustments to production.
Manufacturing Optimization Through Machine-Driven Data Analysis
With instant access to data across every machine and digital records of each machine’s health history, you can start being predictive about your machine optimization goals. This is where the value of digital machine health becomes transformative, as you can now tie actual machine health data back to operational or product quality metrics.
For example, you might notice emerging problems with a machine after you start producing a new product with different dimensions. By aligning production information and machine data analysis, you can identify and proactively address root machine issues to improve overall efficiency and the quality of the new product.
Augury’s digital machine health platform can tell you when your machines are performing below their peak performance in near real-time. With these predictive insights, process improvement that could take months to implement can now become a machine optimization process that you can complete in just weeks — or even days.
How Augury’s Platform Enables Predictive Manufacturing Optimization
Augury’s machine health platform takes the guesswork out of improving production by identifying which machines need your attention most and it informs you of maintenance tasks that will repair any malfunctions that are present. You can visualize machine performance and find optimal settings by pairing mechanical data with operational output data for each machine and see how each aspect of the process contributes to overall output.
One effective approach is to take an existing process within a production facility and learn why certain quality issues or downtime events keep recurring — and to learn how patterns in your operational procedures or product recipes can affect machine performance. Another tactic is to use digital machine health data to help alleviate manufacturing pain points like unplanned downtime and dealing with a remote or limited on-site workforce or to adapt to changes outside of your control.
Likewise, as demand for different products ebbs and flows, you can shift production between facilities, ramp up new production lines, or switch certain lines to meet the new demands. Visibility into machine health will help you be more flexible and understand what will work to avoid underperformance or machine failure.
Being equipped with this information allows you to make truly impactful decisions when it comes to manufacturing optimization and cost reduction. Instead of buying new machines and adding completely new lines, you can use machine health data to increase capacity in your existing lines. Without machine data analysis, you might not know just how much you’re able to push your machines to accomplish.
Want to learn more? Just reach out and contact us!