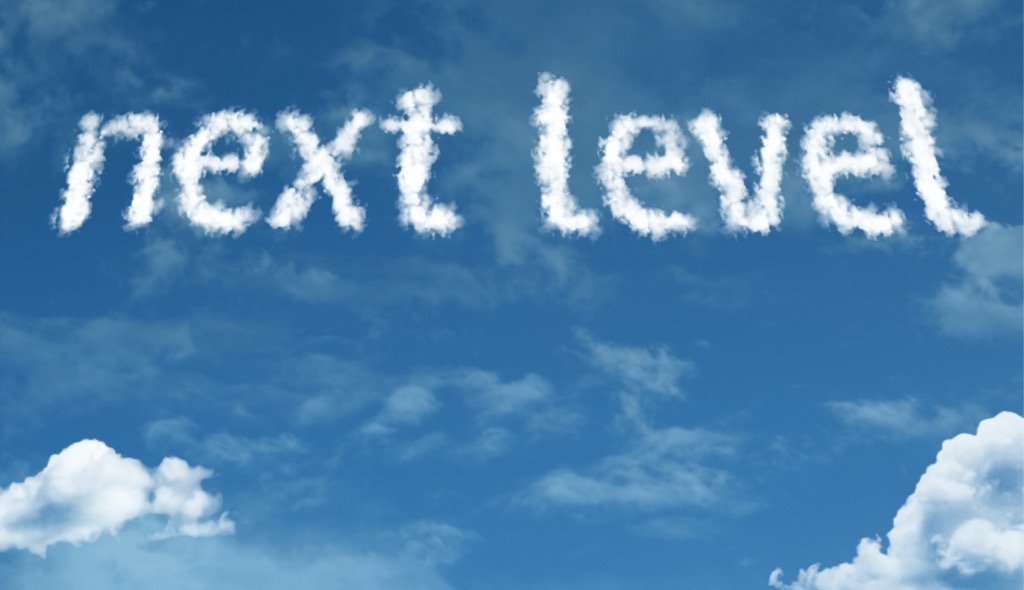
Traditional approaches to manufacturing process optimization rely mostly on human-led analysis and decision-making. This limits manufacturers and ultimately harms their bottom line. However, if you let Process Health take the lead, you will be able to really go after the often-complex root causes that make production less efficient and effective – and then deal with these problems for good.
Continuous production presents some of the most complex challenges faced by manufacturers today. With constant pressure from competitors, emissions laws, and the increasing demand for product quality and quantity, it’s clear why manufacturers need all the help they can get to stay ahead. For these reasons, AI is quickly gaining recognition as a vital tool in helping continuous manufacturing operations evolve.
By adopting AI, more and more process engineers are moving from a touch-and-go improvisational mindset to one that is deeply data-driven, focused, and agile, to meet the dynamic nature of continuous process manufacturing.
Despite that, most manufacturers are still conducting their root-cause analysis and process optimization efforts manually. This approach relies heavily on human experience, judgement and intuition – which is inherently limited.
Out with the Old:
4 Reasons Why Human-led Optimization Harms The Bottom Line Of Any Production Process
Of course, process experts aren’t working with a paper-and-pen. Most modern-day manufacturers utilize tried-and-tested statistical models and data visualization and analytics tools to conduct root-cause analysis. Some are also using generic machine learning algorithms for more advanced analysis.
But when measured over time, these traditional approaches struggle to reach targets when it comes to process-related challenges like yield, waste reduction, energy efficiency, emissions reduction, quality and throughput. Here’s why:
1) True Root Causes Are Hidden
Due to the complex nature of process manufacturing, the abundance of complex data also means an abundance of “noise” which clouds efforts to pinpoint the root cause. Manual analysis – even with the help of data visualization and self-serve analytics tools – simply won’t cut it. There’s just too much data, spread across a vast tangle of interrelated set points, for a human being to constantly consider.
2) Manufacturing Processes Are Dynamic
Variability of raw materials, humidity and temperature fluctuations, dynamic traceability, weather conditions and a slew of other factors, make it impossible to reach actionable conclusions that have value over time. This is true even when using generic machine learning, as these algorithms don’t take the complex, dynamic realities of the production process into account.
3) Production Teams Are Already Under Pressure
A human-led approach to process optimization can pile work onto already very busy teams – via hours of manual analysis, discussions and trial and error – often without yielding any benefits to the bottom line.
4) Human-Led Optimization Doesn’t Scale
Even if a root cause is determined using manual or human-led analytical methods, the solution cannot be replicated for use with another production line since each has its own set of performance values. That means starting from scratch every single time…
Embracing the New:
4 Ways Process Health Augments Your Human Expertise
In summary, the shortcomings of the human-led approach are clear: continuous process manufacturing is simply too complex and dynamic for manual calculations to provide actionable solutions.
The motivation behind Process Health, which uses real-time AI alerts and insights, is to help manufacturers solve process inefficiencies by revealing root causes and recommending the right actions.
This isn’t about replacing your human process experts and manufacturing teams – it’s about empowering them to transcend the limitations of what is humanly-possible, and ultimately master their manufacturing processes.
What is Process Health?
In a nutshell: Process Health takes advanced Machine Learning algorithms, and infuses them with deep process expertise from any given production line. This means that when the “AI” is analyzing your production line, it’s not just looking at the data – it’s also considering all the unique complexities of that production line, from dynamic traceability to loops, buffers, raw material variances, parallel processes, multiple SKUs and so on.
Process Health makes for more accurate, real-time analysis.
1) Process Health makes it easy for process experts and production teams
Apart from being able to determine the root cause of inefficiencies in even the most complex manufacturing processes, a process-based AI solution should be intuitive and provide straightforward user interfaces and solutions to investigate and prevent production losses.
2) Process Health constantly adapts to changes in your process
Process-based AI continuously works behind the scenes, instantly adapting to changes in your process to provide insights and recommendations that are always relevant.
3) Process Health can easily scale across production lines, and across plants
Traditional static algorithmic approaches just don’t scale. With the correct adoption strategy, process-based AI can be scaled across production lines and even multiple factories without significant disruption.
4) Process Health frees your people from endless data tasks, and empowers them to focus on processes optimization
“AI” in popular culture often conjures up images of machines replacing people. In reality, for manufacturers this could not be further from the truth. In fact, perhaps the greatest benefit of Process Healthis that it empowers your process experts and production teams to work more effectively and efficiently.
Process Health relieves your people from mundane, never-ending data crunching and theorizing, and delivers clear, timely insights and recommendations for them to act on. This starts them on the right foot, and enables them to focus on what they do best: optimizing production lines.
Do you want to learn more about how Process Health can lead to significant improvements across the board – from improving quality, throughput, energy efficiency and yield, to reducing CO2 emissions and waste? Reach out to speak to one of our experts.