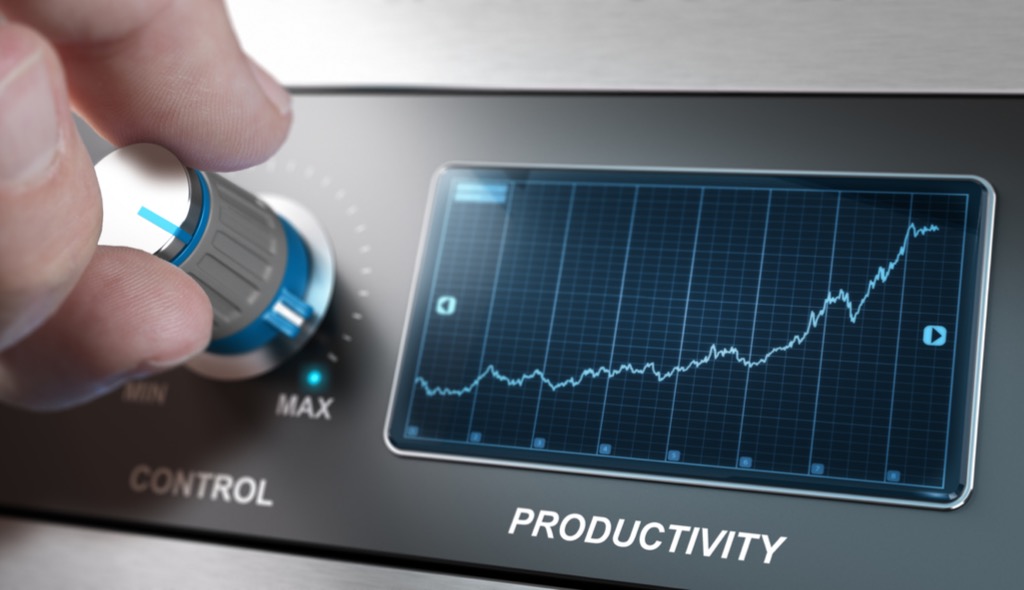
OEE has remained a valuable metric over the decades, but methods for improving equipment effectiveness have changed and advanced over time.
This article was originally published in Industry Today.
The overall equipment effectiveness metric was coined in the 1970s and continues to be one of the most widely used metrics in manufacturing. OEE is calculated from three components:
- Availability: Uptime divided by the total planned production time. That is, how much time the machine was in use as opposed to the total time it was planned to be used.
- Performance: Performance shows part rate (or flow rate for process as opposed to batch manufacturing) and is calculated by dividing the number of parts produced by the maximum part rate.
- Quality: This measures whether quality products are being created by the machine. This is determined by dividing good count parts by total parts. Good count parts meet quality requirements and can be sold.
OEE is certainly not the only metric manufacturing leaders should consider when determining the success of their organizations. They also need to look at a broader set of metrics to assess the full health of a business: metrics involving business operations, actual plant floor or facility operations, and asset performance or machine health, for example.
But OEE does play a critical role, and it’s still an important part of measuring productivity. On the operations side, for example, revenue is directly tied to the availability of machines at any given time to produce the goods that ultimately drive a company’s bottom line. Usually, the more efficient production is, the higher the revenue. Manufacturing leaders today must focus on the intersection of all these areas — that’s what’s driving business, and it’s all about increasing production volume while lowering costs.
However, manufacturing leaders must also consider that OEE was initially developed more than 40 years ago. Technology has advanced a lot since then.
How to Improve OEE in the Era of Industry 4.0
While OEE has remained a valuable metric through the decades, methods for improving it have changed and advanced over time. Today, innovative technologies leading manufacturers from industry 3.0 practices to industry 4.0 efficiency enable new ways of tracking and acting upon machine health data. In turn, manufacturers can make well-informed decisions based on precise information to improve OEE and drive overall success in the following ways:
1) Improving machine availability
New technology at the forefront of industry 4.0 can directly impact how maintenance teams approach downtime. For example, predictive and prescriptive analytics offer insights that weren’t available in the past. When you know in advance when and how a machine will likely fail, you can prevent costly unplanned and planned downtime by taking a condition-based approach to maintenance.
Instead of running planned maintenance on a time-based schedule, condition-based monitoring enabled by advanced analytics allows you to assess the true state of a machine and prolong the time between maintenance if it’s in a good state. This increases your total productive hours and eliminates unnecessary stoppage.
2) Improving performance by reducing changeover problems
Changeovers can cause machine problems that hinder performance. For example, say a mixing machine typically mixes a thin recipe and the machine’s blades spin through the mixture easily. When manufacturers shift the machine to a new recipe, however, the higher viscosity of the new mixture causes the machine to vibrate harder as the blades mix the thicker recipe. This excess vibration can place greater strain on the machine and lead to lower performance and eventual machine failure.
With machine health monitoring sensors installed on machines, however, manufacturers can immediately see in the data that the new recipe is causing higher vibrations. They can then make swift adjustments to properly optimize the machine for the changeover, avoiding lost productivity and potential unplanned downtime.
3) Reducing scrap and improving quality
A large portion of quality issues are rooted in poor performance of the actual machines. By using new predictive and prescriptive diagnostic technologies that provide deep, actionable insights into machine health, you can reduce scrap and quality issues by ensuring that assets are operating at their optimal levels. What’s more, you gain insight into why quality issues might occur and can adjust before production quality is actually hindered.
Time and innovation haven’t lowered the significance of OEE in manufacturing; they have just necessitated a change in how manufacturers think about, measure, and achieve equipment effectiveness. With the advanced tools available today, manufacturing leaders have more opportunity than ever to increase the effectiveness of their machines, improve production efficiency, and reduce downtime.
Read more about ‘Why Machine Health Monitoring Is the Key to Improving OEE in the New Era of Manufacturing‘.