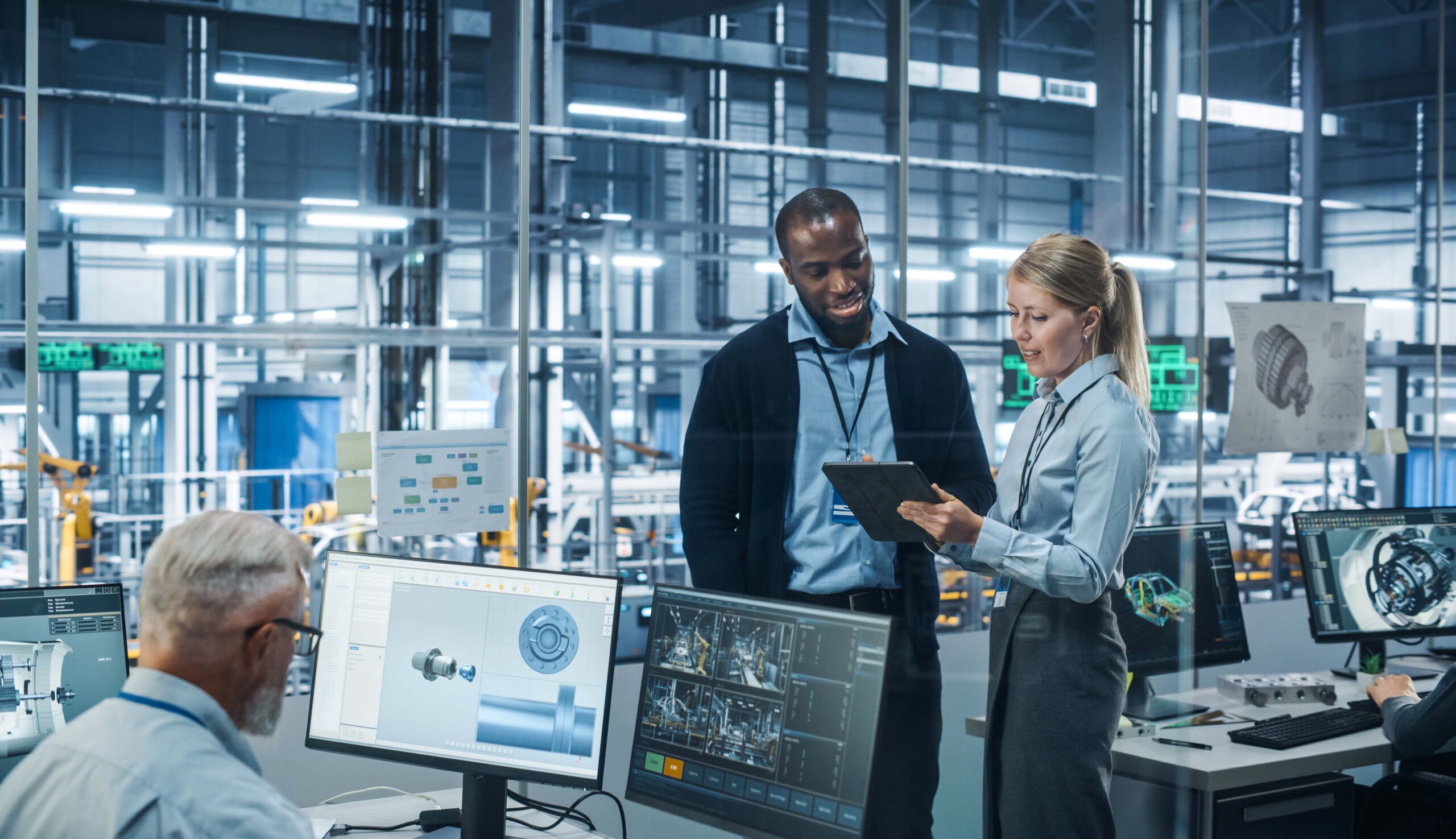
A lot of the hype surrounding artificial intelligence in manufacturing is focused on industrial automation, but this is just one aspect of the smart factory revolution — a natural next-step in the pursuit of efficiency. What artificial intelligence also brings to the manufacturing table is its capability to open up completely new avenues for business.
What is Industrial AI’s Impact on Manufacturing?
In this article we not only outline AI’s ability to drive industrial automation and open up new business opportunities as part of the emerging Industry 4.0 paradigm, we will also introduce how this powerful technology is already being used by manufacturers to drive efficiency, improve quality and better manage supply chains.
Basically, AI’s impact on manufacturing can be organized into 5 main areas:
1) Predictive Quality and Yield
2) Predictive Maintenance
3) Human-robot collaboration
4) Generative design
5) Market adaption/supply-chain
Now, let’s break these down individually.
1) Predictive Quality And Yield
Reducing production losses and preventing production process inefficiencies has always been a constant struggle for manufacturers of all stripes. Today, this is truer than ever, as growing demand meets increased competition.
On the one hand, consumers’ expectations are higher than ever before; global consumer habits are gradually “westernizing”, even as the population boom continues. According to numerous surveys in recent years, the global population will grow by 25% by 2050, equating to some 200,000 additional mouths to feed every day.
On the other hand, consumers have never had so many alternatives available to them, in almost every product imaginable. Recent surveys indicate that this wealth of options means consumers are increasingly likely to permanently ditch even their favorite brands if, for example, a product isn’t available on the shelf.
Prevent Losses Before They Happen
Against such a backdrop, manufacturers can no longer afford to take process inefficiencies, and their associated losses, in their stride. Every loss in terms of waste, yield, quality or throughput chips away at their bottom line and hands another inch to the competition — assuming their production processes are more efficient.
The challenge for many manufacturers — particularly those with complex processes — is that they eventually hit a glass ceiling in terms of process optimization. Some inefficiencies don’t have any obvious cause, and process experts are left at a loss to explain them.
Predictive Quality and Yield uses AI-driven Process Health Solutions to reveal the hidden causes of many of the perennial production losses manufacturers face on a daily basis. This is done via continuous, multivariate analysis, using Machine Learning algorithms that are uniquely trained to intimately understand each individual production process. The specific AI/Machine Learning technique used here is termed “supervised learning”, where the algorithm is trained to identify trends and patterns in the data.
Automated recommendations and alerts can then be generated to inform production teams and process engineers of an imminent problem, and seamlessly share important knowledge on how to prevent the losses before they happen.
2) Predictive Maintenance
Predictive maintenance is one of the most basic and well-known applications of Industrial AI. Instead of performing maintenance according to a predetermined schedule, predictive maintenance uses algorithms to predict the next failure of a component/machine/system and then alerts personnel to perform focused maintenance procedures to prevent the failure, but not too early so as to waste downtime unnecessarily.
Again, predictive maintenance systems rely on Machine Learning techniques to formulate their predictions (albeit a different category – unsupervised learning, rather than supervised). The advantages are numerous and can significantly reduce costs while eliminating the need for planned downtime in many cases.
By preempting a failure with a machine learning algorithm, systems can continue to function without unnecessary interruptions. When maintenance is needed, it’s very focused – technicians are informed of the components that need inspection, repair and replacement; which tools to use, and which methods to follow.
Predictive maintenance also leads to a longer Remaining Useful Life (RUL) of machinery and equipment since secondary damage is prevented while smaller labor forces are needed to perform maintenance procedures.
3) Human-Robot Collaboration
According to the International Federation of Robotics (IFR), as of the year 2020 an estimated 1.64 million industrial robots were in operation worldwide. The general approach as jobs get taken over by robots is that workers will be offered training for higher-level positions in programming, design, and maintenance. In the meantime, the efficiency of human-robot collaborative work is being improved as manufacturing robots are approved for work alongside humans.
As the adoption of robotics in manufacturing increases, AI will play a major part in ensuring the safety of human personnel as well as giving robots more responsibility to make decisions that can further optimize processes based on real-time data collected from the production floor.
4) Generative Design
Manufacturers can also make use of artificial intelligence in the design phase. With a clearly defined design brief as input, designers and engineers can make use of an AI algorithm, generally referred to as generative design software, to explore all the possible configurations of a solution.
The brief can include restrictions and definitions for material types, production methods, time constraints and budget limitations. The set of solutions generated by the algorithm can then be tested using machine learning. The testing phase provides additional information about which ideas/design decisions worked, and which did not. In this way, additional improvements can be made until an optimal solution is found.
5) Market Adaptation / Supply Chain
Artificial intelligence permeates the entire Industry 4.0 ecosystem and is not only limited to the production floor. One example of this is the use of AI algorithms to optimize the supply chain of manufacturing operations and to help them better respond to, and anticipate, changes in the market.
To construct estimations of market demand, an algorithm can take into account demand patterns categorized by date, location, socioeconomic attributes, macroeconomic behavior, political status, weather patterns and more.
This is groundbreaking for manufacturers who can use this information to optimize inventory control, staffing, energy consumption, raw materials, and make better financial decisions regarding the company’s strategy.
Industry 4.0 Demands Collaboration
The complexity of using artificial intelligence in industrial automation requires that manufacturers collaborate with specialists to reach customized solutions. Attempting to build the required technology is costly and most manufacturers don’t have the necessary skills and knowledge in-house.
An Industry 4.0 system consists of a number of elements/phases that need to be configured to suit the manufacturer’s needs:
- Historical data collection
- Live data capturing via sensors
- Data aggregation
- Connectivity via communication protocols, routing and gateway devices
- Integration with PLCs
- Dashboards for monitoring and analysis
- AI Applications: Machine Learning And Other Techniques
After many years of Industrial AI being a distant aspiration for most manufacturers, today these technologies are real and readily available. Of course, the most important principle to gaining true value from an Industrial AI solution is knowing which one is relevant for any given business challenge.
Interested in learning more about selecting the right industrial AI solution for your unique situation? Reach out!