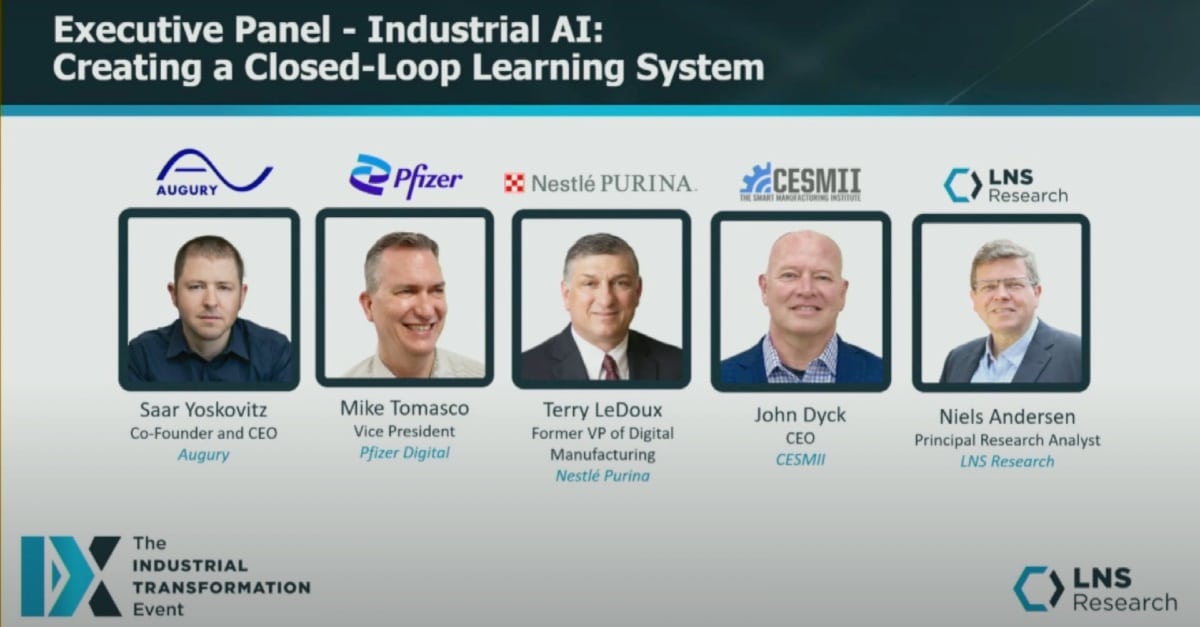
During the Executive Panel at IX Event 2023, top executives discussed how to lift US manufacturing to new heights of productivity. They all agreed: it doesn’t matter if you want to transform a workforce, a factory or an ecosystem, it’s all about expanding on trust.
Every year, LNS Research hosts The Industrial Transformation (IX) Event where C-Suite innovators gather to discuss and drive the future of manufacturing.
This year’s highlight was the Executive Panel Discussion, ‘Industrial AI: Creating A Closed-Loop Learning System’, which featured Augury Co-Founder and CEO Saar Yoskovitz, Principal Research Analyst at LNS Research Niels Andersen, VP of Pfizer Digital Mike Tomasco, retired VP of Digital Manufacturing at Nestlé Purina Terry LeDoux, and CEO at The Smart Manufacturing Institute John Dyck.
Moderated by LNS Research analyst Bob Francis, the panel explored how to successfully implement the latest AI-driven innovations and tools – including generative AI technologies such as ChatGPT. The discussion proved wide-ranging but one theme arose: trust is key across the board.
Building Trust, From AI To Partners
“When you look at deploying new technologies, it’s not about the technology,” says Augury’s own Saar Yoskovitz in his opening remarks. “It’s about cultural change you need to manage. And the moment the solution either gives too many false alarms or misses malfunctions, you lose trust.”
Terry LeDoux agrees. “At Purina, I had the opportunity to not just be part of industry 3.0 but really take off on industry 4.0 as an early adopter. And our focus has always been about enhancing human performance: driving emotional participation to build the trust that Saar talked about. You’ve got to trust the digital tools on the factory floor to succeed in lining those digital building blocks up to get us to generative AI.”
And unless you’re a Pfizer and big enough to have a large team of data scientists developing in-house solutions, you will need a trusted partner – one that knows not only the science but also the means to drive adoption.
And to find that partner, you will first need to ignore AI altogether and focus on your specific use case. “The question is: What’s the outcome you want to achieve? AI is a tool, it’s not the outcome,” says Saar. “So first, let’s identify the problem. Do you want to increase uptime and capacity? Do you want to reduce waste and meet sustainability targets? Only then, can you seek to select the right tool, and partner, for the job.”
Meanwhile, Back On The Floor…
You definitely need more than just reliable AI to build up the trust on the floor. You also need to convince operators that a particular solution is enhancing their job and not taking their job away.
“I don’t think the robots are going to come in and do everything,” says Terry. “But when we go out to the floor, we don’t talk about AI. We talk about having a new tool and asking people to help us figure out if it works to solve a particular problem. And people aren’t unhappy about trying something new,” says Terry.
“And this is how you develop trust: engaging the operator to participate in making a tool a new enhancement to their jobs.”
The Building Blocks To Drive Better Productivity
Today, in terms of the “new”, the whole panel sees the next big step change as the world of Generative AI and large language models (LLMs). “I see it becoming that copilot or personal digital assistant for the manufacturing operator on the floor,” says Terry. “It can learn to bring information to them when they need it, and in a way they work best. So, this becomes the new horizon for enhancing human performance. But this won’t happen tomorrow,” says Terry. “First, you need your basic building blocks in place to be able to move on these tools.”
As Pfizer’s Mike Tomasco said earlier: “We started with the foundational work of making sure you have your processes in a good state and these processes are going through a similar set of core systems to generate the data and hopefully manage that data in a good way.”
Building The Trust Across the Industry
The Smart Manufacturing Institute is out to inspire the building of these building blocks – while taking the full ecosystem for the ride. “We’re funded by the federal government to help us manufacturing become more competitive, and to accelerate the adoption of smart manufacturing. And we have been given roughly $200 million to accomplish our mission,” says CEO John Dyck.
“I think the word interoperability is the single most important idea behind how we can level or bring back up that productivity curve. It’s about culture, it’s about people. It’s about ideas. It’s about convening collaboration technology,” says John.
“The notion that we’re going to scale AI on the shop floor, in the enterprise, and in the supply chain, is going to take significant collaboration between every stakeholder in this ecosystem. And that’s part of our mandate: to raise the tide so all the boats float higher.”
Taking The Full Ecosystem Across The Digital Divide
And the idea is that the Fortune 1000 manufacturers – who are only 8% of the manufacturing companies in the US – can pave the way to make it easier for those small-medium enterprises (SMEs) that make up their supply chains.
“For a company like Pfizer, you want to be a good partner,” says Mike. “You want to be a partner that people want to work with. And often in our world, we want access to our suppliers’ data that then drives some of our processes. But the suppliers need an incentive to provide that.”
For instance: “You can help these SMEs with guidance and a framework to work in, so they see a path,” adds John.
And in turn, the SMEs can further drive the democratization of smart manufacturing. “I think the small medium manufacturers represent a huge opportunity for new business models and new ways of collaborating,” adds LNS Research’s Niels Andersen. “They don’t have a lot of the heavy processes and constraints that a lot of our big manufacturers have.”
Building A Trust-Based Supply Chain – Where Everyone Wins
A comparison was made to the development of the US interstate system. “That was something that no individual town, village, city or state could do,” says John. “And that’s the role we’re excited to play in this space around suppliers interchanging data with their manufacturers,” says John.
“But first you need a standard or a set of trusted regulatory frameworks so you’re not asking Manufacturer X to do something totally unique from what Johnson & Johnson is asking them.”
“And we’ve seen a lot of examples,” says Niels, “where a collaborative supply chain will beat a supply chain that competes every day.”