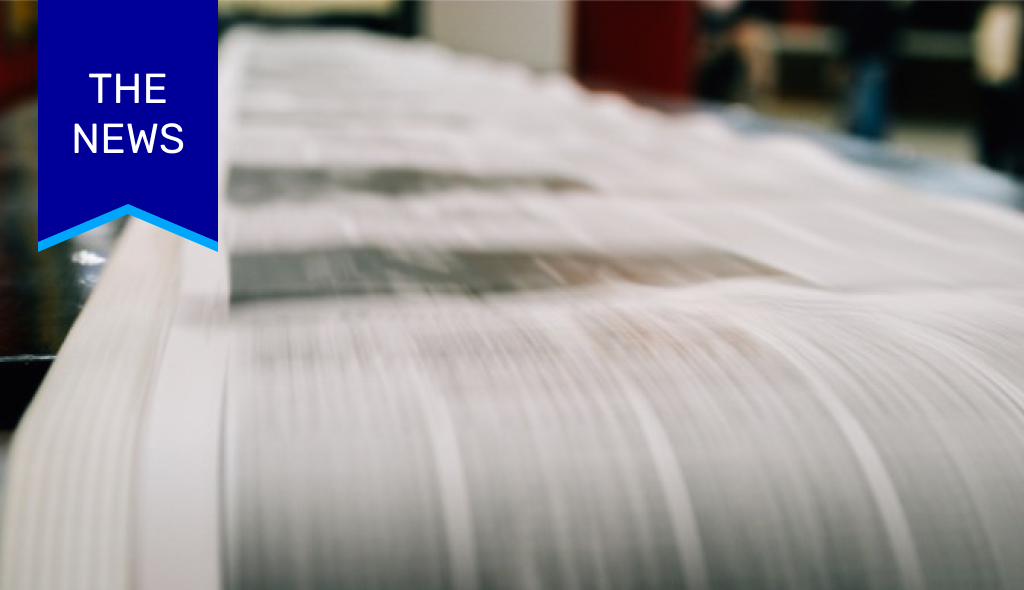
Augury listens to machines. But we also listen to the world. This helps us to better know our place in making it a better place. Here’s a round-up of some of the manufacturing-related press from this month that caught our eye – and why it mattered. From digital transformation, to disrupting supply chain disruptions, to the power of fish sticks…
We know we live in challenging times. As a result, many of us are scaling on our learning curves. Take artificial intelligence and manufacturing: many pundits say we are currently taking leaps over a year that would have otherwise have taken a decade.
That’s a lot of learning.
Making IKEA Furniture Without Instructions
Just look at the wild ambition behind the question: Is Launchpad “The Tesla of Manufacturing”?
“Manufacturing, long the forgotten Cinderella of software, may have found its prince. Launchpad […] is using artificial intelligence to take designs from blueprint to final production, automatically sourcing components and manufacturers, slashing time and costs for the limited runs and customized goods that customers increasingly want.”
If successful, “you could just say, ‘here are the design files, make it’.” And a couple of days later, it’s made. “It’s like coming up with a way to put together IKEA furniture without the instructions.”
Interesting. Tell us more.
How to Disrupt the Disrupted Supply Chains
“Long-distance supply chains hide costly risks — and those risks may help usher in a new stage of global commerce,” according to ‘The Stuck Container Ship on the Suez Canal Was a Metaphor’ – an article that offers a neat summary of the evolution of global trade.
Basically, cheap wages and massive scale (large and specialized factories) no longer make complete sense. It worked great for revenue for a while but COVID-19 and the Suez blockage worked to shift perceptions. Companies need to intimately understand and manage their supply chains – and not sub it out to third parties to do it for them.
“In globalization’s next stage, ships carrying metal boxes full of stuff will no longer be at the center of the story […] In its place, a new stage of globalization, in which factory production and foreign investment matter less than the flow of services and ideas.”
Time to go with the flow.
Think BIG. Invest BIGGER
“The president’s plan covers infrastructure improvements, climate change and manufacturing,” according to ‘Biden’s Infrastructure Plan Visualized: How the $2.3 Trillion Would Be Allocated’.
Now that’s a holy trinity we can get behind.
The ambitions seem to mirror the recommendations from the recent – and much covered – McKinsey Global Institute discussion paper ‘Building A More Competitive US Manufacturing Sector’.
The paper’s co-authors nicely summarized their findings in ‘Ensuring the Continued Resiliency of U.S. Manufacturing’: “Pandemic-related incidents have delivered a stark reminder that manufacturing capabilities matter – not only to fuel the economy in good times but to keep it functioning in crisis.”
And unfortunately, while more regional-based supply chains may offer part of the solution, too many links are missing. “Thousands of smaller manufacturers have shuttered in the past two decades, leaving gaps in domestic supply chains and capabilities.”
“Tiny chips illustrate the huge stakes. Advanced semiconductor chips power everything from your smartphone to advanced military aircraft, and the United States needs a steady supply at competitive prices. But a leading-edge semiconductor fab can cost $20 billion to build. Then it can take two to three years to ramp up production and longer to break even.”
But investment in US manufacturing holds promise. “Though manufacturing represents simply 11 per cent of gross home product and eight per cent of direct employment, it drives 20 per cent of the nation’s capital funding, 30 per cent of productiveness progress, 60 per cent of exports and 70 per cent of enterprise R&D.”
“For all of its pain, the pandemic might turn out to be the kind of watershed moment that grants permission to tear up the old rulebooks and try something new. It’s a now-or-never moment to regain capabilities and market share before they are lost forever.”
Get ripping.
Looking for A Scaling Challenge?
It’s a near-perfect title: ‘Vodka, Toothpaste, Yoga Mats … The New Technology Making Items Out of Thin Air’. The article covers an exhibition on carbon harvesting machines taking place at London’s Science Museum.
And indeed, we likely need to extract greenhouse gasses from the atmosphere and factory emissions. “Because it is unlikely that cutting greenhouse gas emissions alone can be achieved quickly enough to prevent global overheating this century,” says an expert.
Unfortunately, these machines are still highly inefficient and largely unscalable. But do you remember what mobile phones looked like 20 years ago? Can we make the same leap with these extraction machines in two years?
What Can Fish Stick Manufacturing Teach Us?
Now for a story to file under ‘This Month in Sustainable Manufacturing History’: ‘Fish Sticks Make No Sense – How A Weird 1950s Finger Food Made It Big’.
Once upon a time, someone decided to cut up frozen excess fish bricks into sticks before breading them and deep-frying them. “The hotdog of the ocean” was born. And these salty dogs are actually quite sustainable, rivalling “the climate impact of tofu”.
Meanwhile, in the UK where fish sticks are called fish fingers, “a survey revealed that one in five young adults believes they are actually the fingers of fish.”
Which only goes to prove that, yes, learning should indeed be embraced as a lifelong journey.
Interested in reading ‘Manufacturing – The News, March 2021’?