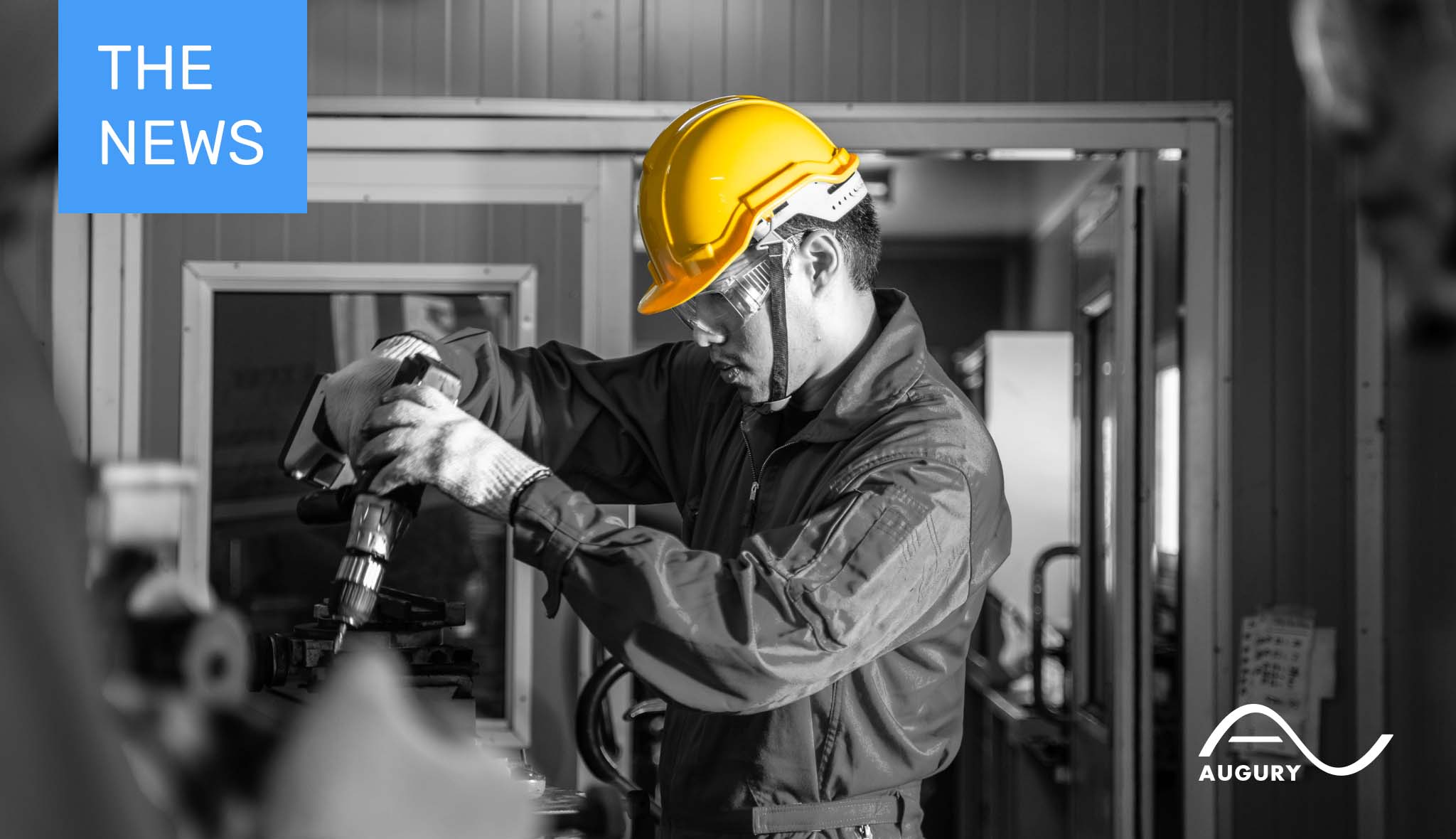
The headlines are full of stories about “The Robots Are Coming!” And for better and for worse, we will need them to face down our challenges. Meanwhile, we’ll also always have to loop in the humans into the equation… Read all about it in our monthly round-up of manufacturing-related news.
The Machines Are Coming… For A Reason
It is changing the face of warfare. Students are applying it to cheat on essays. Companies are using it to make expense reporting easier. Prime Ministers are regarding it as a political advisor. Judges are using it to make verdicts. And yes, you can now officially date a chatbot.
So, it’s safe to say the robots – or at least variants of AI – are coming.
Of course, the manufacturing industry have seen the robot armies massing for decades as a way to fight against a dwindling workforce. Take note of this recent headline: ‘Over Half of US Manufacturing Employees Plan to Leave Their Jobs in 2023’.
However, the same article came with more heartening news: “Another priority for survey respondents besides paid time off and flexible hours was the opportunity to work in high-tech or sustainable factories. About 60% of respondents affirming they would take a pay cut to do so.”
Embrace Talent With More Carrot And Less Stick
‘Why Talent Tops All In Manufacturers’ Year Ahead’ also has some depressing statistics. For instance, 10,000 workers in the US reach retirement age every day. Meanwhile, the manufacturing industry faces $1 trillion in lost revenue by 2030 due to unfilled manufacturing jobs.
But the article also gives solid advice on how to lure and keep talent: “Manufacturers need to engage employees with meaningful experiences that also increase productivity. For example, while AI-based data analytics tools can highlight any gaps or weaknesses in performance, this information should be used to improve the overall employee experience rather than to call out those perceived to be falling short. Offering more carrot, less stick in other words, with insights acting as the basis for helping staff – and, in turn, the company – can lead to enhanced productivity.”
“This means focusing on what workers want and need, then using that knowledge to create an environment where people don’t just work a job but stick around to build a diverse and rewarding long-term career.”
Upskill To Become A Robot Whisperer
In a rather optimistic interview with the CEO of Rockwell Automation, ‘How Does A Manufacturer For Manufacturers View Today’s Economy?’, there’s an interesting discussion on the “paradox of automation” where when a job is lost to automation, a better and more value-generating job is created.
“Upskilling is absolutely essential. And I’ll just start with an example. Rockwell is adding jobs, we’re significantly bigger in terms of total headcount than we were a few years ago, because we think the winning hand is trained people, highly-engaged and enabled people working alongside the technology. And the technology, in some ways, gives those people superpowers.”
Who doesn’t want a superpower?
The Many Revolutions Of The Industrial Revolution
‘Yet Another Industrial Revolution’ explains how daunting the challenges really are for manufacturers – and humanity as a whole. While the first Industrial Revolution improved the human condition immeasurably in terms of life expectancy, child survival, global population and the availability of food, it came with a dark side: the creation of greenhouse gases.
And while the first Industrial Revolution is often spoken of in terms of the big three industries – textiles, steel and coal – that emerged at the time, there were also countless other innovations. (Soda ash! Sanitation! Aluminum! Plate glass! Fertilizer! Microchips! Etcetera!)
“The reality is there have been a panoply of different revolutions in industrial production over the past few centuries. The cliched, Dickensian vision of the Industrial revolution somewhat underplays the diversity of innovation that happened then – but continued to happen well into the 20th century.”
But now we have to re-imagine all these countless processes from centuries of innovation from scratch. And we have to do it all in the space of a few decades.
“I wonder if this has quite dawned on most people yet – the scale of the task at hand, the depth of scientific challenge that faces us. And this is before you consider the fact that we will eventually have to do all of this while relying ever more on sources of energy which are less dense and more intermittent than the fossil fuels we built the industrial revolution on. It is certainly the biggest economic challenge of any of our lifetimes.”
“This is not easy. Not easy at all. Doable? Hopefully.”
Time To Get Along
In short, we need all brains and hands on deck – both carbon and silicon based – to face down these challenges. Machines and humans must start dancing more in tandem. A technology such as AI should do what it’s good at. And humans should do what they’re good at – while avoiding “underestimating the risks of new breakthroughs”.
It’s time to get to work. It’s time to get along.
Read: ‘Manufacturing – The News: Innovations In The World Of Innovation’.