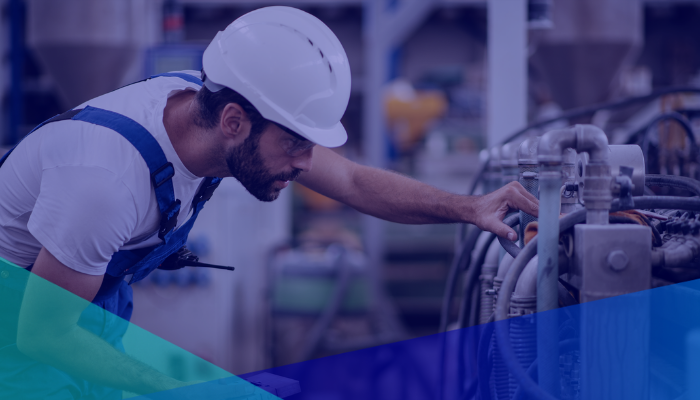
Much of my career experience comes from the time I spent at Procter & Gamble and PepsiCo working to improve efficiency and productivity within individual facilities and across entire regions. The experience taught me a lot about how to improve overall equipment effectiveness (OEE) metrics.
Facility managers should first consider three factors when looking at how to improve OEE: downtime, waste, and speed.
When these factors hurt OEE, it’s likely because facilities are taking a preventive maintenance approach that doesn’t offer enough visibility into true machine health.
With preventive maintenance, machines spend time out of commission. That time could be scheduled downtime (when machines reach assigned thresholds for maintenance and must shut down whether they actually need to or not), or it could be unscheduled downtime (when preventive maintenance fails to stop machine breakdowns). In either form, downtime disrupts production and, in some cases, disables it entirely. It must be minimized at all costs.
Waste/scrap is another consequence of conducting maintenance based on a schedule rather than on machine health insights. Machines might appear to be fully functional, but in reality, performance issues may be degrading the end product. Anything that doesn’t consistently meet strict quality standards shouldn’t go out to the customer (but it sometimes slips through). It ends up as costly waste or negative customer experiences. Worse, that happens despite a manufacturer making a serious effort to maintain machines. The preventive maintenance approach is the problem.
Speed suffers as well. When manufacturers ignore machine health, they unknowingly risk pushing machines past their breaking point. Rushing to fulfill an order ends up causing a major setback. Alternatively, ignorance about machine health may cause manufacturers to be overly cautious, scaling back production out of the mistaken belief that the machines can’t handle extra speed. The problem is the same in both cases: Manufactures can’t adjust the pace of the line to fit the needs of production without opening the door to risk.
I’ve seen these issues persist throughout my career in manufacturing. Each instance was a little different, but in many cases, the root cause was the same: a lack of machine health data. Luckily, I’ve also seen what a factory floor looks like with machine health monitoring and prescriptive insights in the mix. The difference is night and day.
Machine Health Data in Action
A machine health platform like Augury arms facility managers with real-time data on the condition of their machines. They can use this data to address the key factors above, improving OEE for production lines, facilities, and entire regions. Here are a few concrete examples of how a data-driven approach to maintenance solves some of the most pressing problems in manufacturing:
1. Machine health insights can help remove downtime altogether
Aside from detecting failure trends, which allows for maintenance action to prevent loss, machine health monitoring can also improve process efficiency and reliability.
Imagine a factory that makes products in massive mixing vats. When mixing recipe A, the mixer runs well within the normal parameters for the machine. However, recipe B calls for ingredients with a slightly higher viscosity that’s not detected by an operator. Recipe B causes the motors to run harder to sufficiently mix the second recipe, or perhaps the mixing is incomplete. Without a platform to monitor machine health data, the operator wouldn’t know the machine was under any strain to mix recipe B.
A machine health monitoring platform, however, would record and transmit the increased vibration from the motors running harder. Using this information, maintenance teams could then prescribe a set of actions to more closely monitor the machine during recipe B, potentially being able to fine-tune it to achieve a more sustainable run rate for both recipes and preventing the recipe from continuing to strain the machine, leading to eventual malfunction or failure.
In this and countless other ways, machine health monitoring helps manufacturers avoid unnecessary downtime by replacing preventive maintenance with predictive maintenance.
2. Machine health data can help create consistency in production lines, reducing waste
One specific problem we ran into at Pepsi was labeling. Getting a label to stick perfectly onto millions of bottles is no small feat. One particular issue we noticed is that the blades on the machine that cut the labels would go dull over time, leading to sloppy cuts on the labels and many wasted bottles.
A machine health platform, however, would have flagged differences in vibrations that signaled dulling blades. Manufacturers could have predicted when a blade would go dull based on that data and switched the blades before they created poor-quality products, reducing waste and negative consumer experiences with minimal downtime.
3. A full-line view can help maximize total output
While machine health data is beneficial for individual machines like the mixer or the labeler, it can also be beneficial when zoomed out to a full-line view. Maintenance teams can combine operational data, or the end products created by machines, with machine health data to determine how the optimization of individual machines actually impacts production of the line. It might seem counterintuitive, but sometimes optimizing one machine can pull down a production line’s efficiency overall.
For example, imagine a bottle-filling machine rated for 1,000 bottles a minute. There’s a two-minute accumulation time between the filler and the labeler, which is downstream from the filler. What if production needs are such that operators decide to speed up the filler to get more cases out? The line’s controls would automatically ramp up all the machine centers to keep up with the higher volume of bottles.
Many pieces of equipment have a “sweet spot” where they run their best; these settings are called centerlines. With machine health monitoring combined with output data, you may determine that the higher speed is resulting in fewer cases at the end of the line. That’s because you’re pushing individual machines out of their “sweet spot,” resulting in more stoppages and greater waste.
A line that runs consistently will always output more product than one that “sprints” at high speeds — only to shut down when downstream equipment can’t keep up. Slow, stable, and steady always beats fast and irregular in production equipment.
In my experience, there are few things relevant to OEE that aren’t relevant to machine health, too. If manufacturers are going to take one seriously, they must consider both.
Want to learn more? Just reach out and contact us!