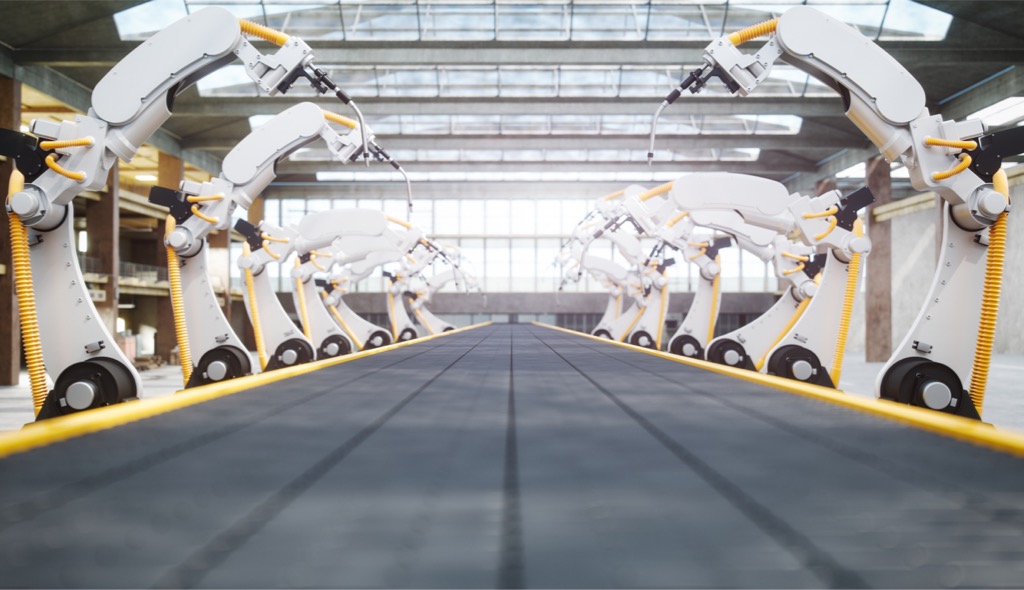
Reducing unplanned downtime can save manufacturers a lot of time and money, but planned downtime can be costly, too. Starting and stopping machines always introduces additional risk for malfunctions and breakdowns, and the longer a machine is down, the more money the company loses while it’s not producing.
Fortunately for manufacturers everywhere, the technology exists today to make planned downtime as quick and efficient as possible so machines can get back up and running faster than ever before. Machine health monitoring systems with advanced AI capabilities like Augury’s can diagnose machines in real time and provide predictive insights about what exactly needs to be fixed and when.
Manufacturers today can work faster and smarter by using machine health insights to reduce planned downtime in two key ways:
1) Prioritizing and Triaging Machine Repairs
Imagine a situation in which you have three different motors of the same size, each with its own unique problem. How do you determine which needs to be repaired or replaced during the next scheduled downtime event?
Without insights into the actual health of the machine, it’s nearly impossible to know which motors are in critical states and which are operating within acceptable parameters. Traditionally, the safest bet might be to just replace all three. But what if two motors could have remained in operation for months without needing a repair, and you needed to replace only one during downtime? You’d have wasted valuable time and money on unnecessary fixes.
With Augury’s machine health monitoring system, however, you can get a much clearer picture of the health of each machine component. Sensors on machines track machine health indicators such as vibration and power usage, and advanced AI algorithms analyze that data to determine diagnostics and predict necessary repairs. Essentially, you get a much better view of what is and is not acceptable in a machine’s current state, enabling you to prioritize repairs and keep downtime to a minimum.
2) Getting People and Parts in Order
Another factor that can prolong machine downtime is not having the right people, parts, or equipment in place before the shutdown. For example, say your on-site technicians begin repairs during scheduled downtime, but they soon discover that they need a technician from the original equipment manufacturer to complete the job. You call the manufacturer only to find out that they can’t make it until tomorrow. So the machine stays down for an extra day, costing the company valuable time and money. Now say the technician arrives only to discover they need a special part or different equipment to make the repair. The downtime event just gets longer and longer.
With a machine health monitoring system, on the other hand, technicians would have a much better idea of exactly what they would need to complete repairs. You could have ordered all necessary parts, acquired all the equipment, and scheduled the downtime event during a time frame of a few hours when all necessary technicians were available. And you’d be back up and running in no time.
3) Optimizing Operational Methodologies
The more you know, the more you can improve your operational flow. By providing the “big picture”, Machine Health data can be used to optimize operational methodologies. For example, if the Machine Health status drops off when a line operates at a certain speed, you can decide to adjust the speed so your assets can perform more efficiently and with less maintenance. In other words, insights can be continually applied to inform and optimize operational decisions — no matter the industry you are operating in. And everyone benefits from optimizing operations. It not only avoids downtime — both planned and unplanned — but also can work to increase safety. Knowledge is power!
The more you know about the health of your machines, the better you’ll be at fixing them quickly and efficiently. Thanks to Augury’s advanced machine health monitoring system, manufacturers today are able to plan downtime based on more telling insights than ever before.
To learn more about how Augury can help your business reduce downtime, get in touch today.