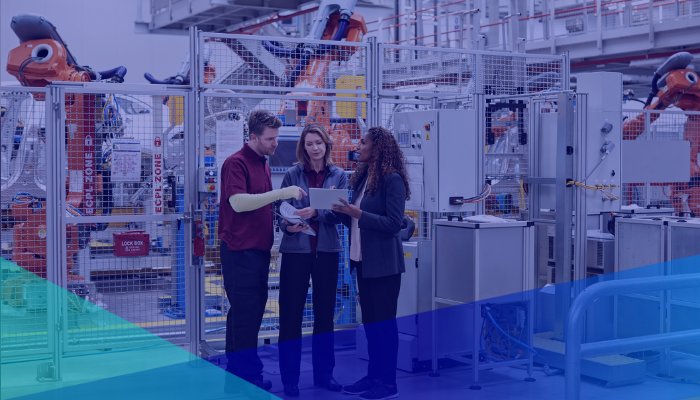
More and more, resilience and flexibility are the defining characteristics of successful manufacturing companies. In fact, the ability to be agile and adapt on the fly is paramount in any industry. Product demands change in a snap; the workforce is becoming increasingly more remote; and the capabilities of modern, AI-driven, and IoT-connected machines are growing exponentially.
A version of this article was originally published on July 1st, 2020.
What Is An Equipment Health Monitoring System?
The resilient operations you need will start with resilient machines. And machine resilience starts with healthy, predictable machines. The good news is that you don’t have to make a huge upfront investment to build that resiliency. A digital machine health monitoring solution offers continuous diagnostics of the equipment you already have and shows you exactly how to optimize it for maximum performance and manufacturing agility.
The system comes down to a continual loop of four basic actions:
- Monitoring (sensors capture data)
- Diagnosing (prescriptive AI does its magic)
- Acting (users acting to fix the problem)
- Guiding (AI insights and expert support help users prioritize and plan)
And now here are four use cases for implementing digital machine health to build resilient operations that can withstand the unexpected and thrive far into the future.
Solving the Equipment Downtime Problem
The first step is to use digital machine health to address machine downtime in individual machines. This happens at the ground level: on the factory floor where various machine configurations make up production lines.
Until recently, the most advanced way to prevent unplanned downtime in manufacturing was to use predictive models that track machine data — such as vibration, oil analysis, and thermography — to predict when machine malfunctions would occur. Most facilities, however, don’t monitor these machines continuously. It still takes a route-based employee or outside contractor doing preventive maintenance readings on a machine or seeing a flashing red light to know something must be addressed.
You can fix your machines long before they ever begin underperforming. This way, you can prevent costly unplanned downtime events and reduce the time machines are down for scheduled repairs.
So, what’s the missing link? Continuous monitoring, diagnostics, and automated alerts — in other words, a digital machine health framework. You can install IoT sensors on each asset in your production line, and a digital machine health solution will continuously monitor that machine and feed the data from each sensor into the cloud, where advanced algorithms detect and diagnose potential problems and recommend fixes — allowing you to correct the problem long before the machine ever breaks down.
By having real-time data at your fingertips to tell you exactly when something is amiss on a machine, you no longer have to rely on lagging indicators, such as low-quality output, to alert you of a problem. You can fix your machines long before they ever begin underperforming. This way, you can prevent costly unplanned downtime events and reduce the time machines are down for scheduled repairs.
How to Optimize the Performance of Your Assets
After you’ve addressed machine health on an individual maintenance level, you can advance your approach by optimizing the performance of your assets. Continuous machine health data helps manufacturers prevent unplanned downtime and gives them more than just visibility into how their machines are running. It also allows them to optimize the performance of those machines. This step elevates the role of machine health within your company from maintenance to machine optimization.
When you have data on each machine in your production line and digital records of the history of those machines, you can tie it to your output and product quality metrics to fully optimize your production lines.
For example, if the data records indicate that your machines only vibrate at a higher intensity while producing one specific version of a product, the algorithm can produce diagnostic insights that will help you identify the root cause and address it proactively — either by maintaining the asset, changing your processes, or even altering your product recipe. This will ensure that, down the line, correctable problems never lead to wear and tear on your machines or lower-quality output.
Ultimately, it’s about having the data to make informed decisions.
A digital machine health platform can give you real-time insights into how machine performance correlates to the quality of your outputs and the potential to maintain that quality down the line. Machine health data takes the guesswork out of which machines in your line you need to optimize, and predictive insights allow you to implement changes in production to maintain high-quality output standards in weeks or even days instead of the typical year-long implementation process.
Ultimately, it’s about having the data to make informed decisions. You must first have the real-time predictive insights to allow you to stop relying on lagging indicators and, instead, know exactly which machines need attention as soon as they do. Once the maintenance aspect is covered, you can use the data records from each machine to recognize patterns and make adjustments for machine optimization.
Increasing Manufacturing Efficiency at the Cross-Company Level
Once you’ve gained a deeper insight into your machines on the ground floor, it’s time to zoom out on the role of digital machine health and look at whole asset classes.
When experts on the factory floor implement machine health solutions, it creates a whole set of historical machine data to give regional directors a bird’s-eye view of machines companywide. When leaders can see this data alongside production quality and output and compare it among various facilities, they’re more easily able to prevent risk at scale and uncover further opportunities to increase productivity and efficiency in manufacturing.
For example, if a site manager uses insights from his machine health solution to correct a recurring mechanical issue, he can then relay the issue, and solution, to the regional director. The director can then look into the machine performance data from other facilities to see whether this issue occurs elsewhere.
It’s about pairing the real-time data with human intelligence and experience to find and fix problems at scale, eventually making every production line perform like your best production line. Maybe you realize that every facility lagging in production uses the same lubrication vendor, which is different from your most successful facilities. Then you know to look into switching that vendor for your underperforming facilities.
With machine health data, you can also see the true indicators of productivity and efficiency. You may currently say your most productive lines are those with the most output. But if you examine their machine health data and find that those machines are breaking down every few weeks or are all on the verge of breaking down and requiring costly repairs, then it becomes clear that it’s not your most efficient line.
Having deeper, more accurate insights about which are your best lines can help you make more informed decisions when necessary, such as shifting production to account for changes in demand. You’ll know which facilities will be best suited to handle products in high demand and which should focus on the lower-demand items.
Enabling Remote Collaboration
The on-demand capability to diagnose machine health issues, prevent machine failure, and enhance operations across multiple facilities makes equipment health monitoring vital to manufacturing agility. It also creates opportunity in one of the most challenging problems in the manufacturing industry today — giving employees the ability to work and collaborate with each other remotely.
People who are charged with operating and maintaining machines can use digital machine health monitoring platforms to fundamentally change how they work. The machine health data that the system collects and analyzes creates a single source of truth about how machines operate. The platform turns this data into actionable intelligence and, combined with collaborative technology, enables remote collaboration in manufacturing.
For example, Augury’s remote collaboration tool ensures that all stakeholders throughout the production process have access to relevant machine health data at any given time. This allows machine maintenance teams to monitor machine health remotely — but in real time — and to digitize up-to-date knowledge, such as newly enhanced machine maintenance programs. Machine operators can also collaborate with maintenance instantly if problems do occur.
From day-to-day operations to big-picture strategy changes, a company’s manufacturing agility relies on its ability to connect all stakeholders in the production process with relevant, trusted data.
Boosting Productivity… And Agility
The enhanced ability to collaborate remotely also opens the door for utilizing new areas of expertise to solve problems in the manufacturing industry. The demand for knowledge work within the industry has skyrocketed as manufacturers employ more advanced, digital, and automated machines. Applying that expertise to digital machine health data has significant implications for the future of knowledge work in manufacturing.
From day-to-day operations to big-picture strategy changes, a company’s manufacturing agility relies on its ability to connect all stakeholders in the production process with relevant, trusted data. A digital machine health platform makes this possible. Through data-driven collaboration, machine operators, maintenance teams, and higher-level executives can all make better, more insightful decisions that improve the company’s resilience and productivity.
Implement Machine Health With Augury
Implementing machine health monitoring helps frontline facility workers better understand the machines they rely on so heavily. However, aggregating and analyzing the data these devices collect — and combining it with remote collaboration software — is how companies unlock the full potential of digital machine health.
For more information about how Augury can help maximize your company’s efficiency and increase productivity in manufacturing, contact one of our experts today.