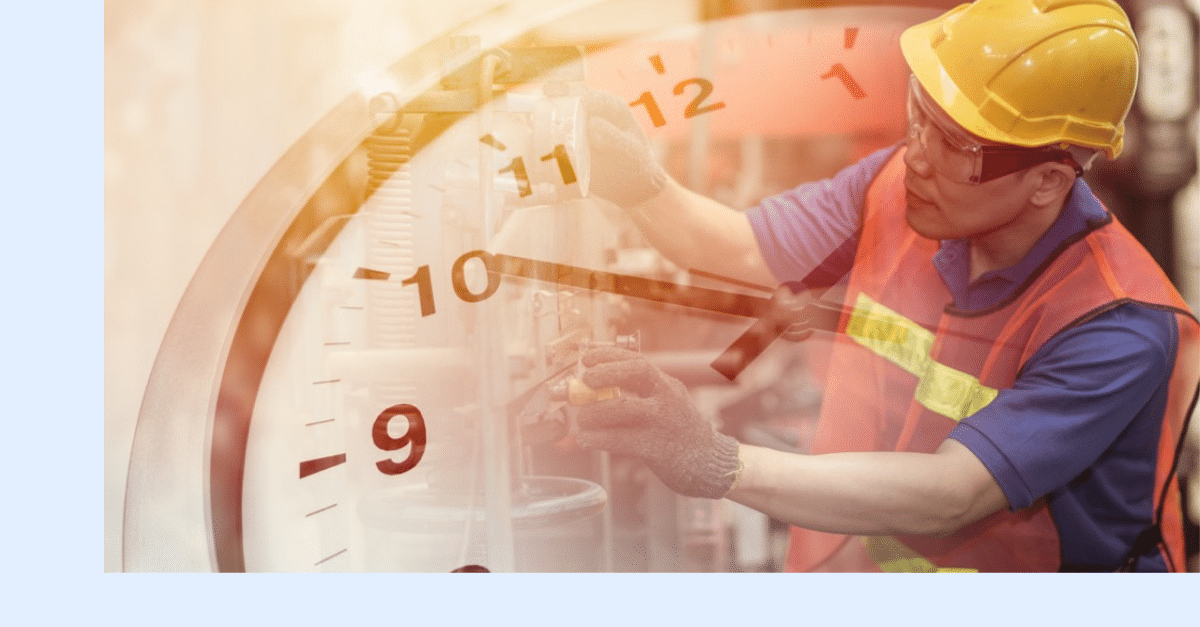
In today’s competitive industrial landscape, businesses constantly seek innovative strategies to optimize equipment performance, reduce downtime, and minimize maintenance costs. Predictive maintenance systems have emerged as a game-changing approach that revolutionizes how organizations manage their critical assets and infrastructure.
What is a Predictive Maintenance System?
A predictive maintenance system is an advanced AI-driven approach to equipment management that uses data analysis, sensor monitoring, and sophisticated algorithms to predict potential machinery failures before they occur. Unlike traditional reactive or even preventive maintenance methods, predictive maintenance provides real-time insights into equipment condition, allowing you to:
- Anticipate potential mechanical issues
- Schedule maintenance precisely when needed
- Prevent unexpected equipment breakdowns
- Optimize maintenance resources
- Extend the operational lifespan of critical machinery
This approach transforms maintenance from reactive and panicky “fire-fighting” into a strategy h that directly impacts operational efficiency and bottom-line performance.
Read ‘Why The Confusion? Prescriptive Maintenance Vs Predictive Vs Preventative’.
How Does Predictive Maintenance Work?
Predictive maintenance operates through a sophisticated combination of technologies and analytical processes:
- Data Collection
- Advanced sensors are installed on critical equipment
- These sensors continuously monitor various parameters such as:
- Vibration
- Temperature
- Acoustic emissions
- Electrical currents
- Lubricant condition
- Real-Time Monitoring
- Collected data is transmitted to centralized monitoring systems
- Machine learning algorithms identify patterns and anomalies
- Predictive Analysis
- Sophisticated models predict potential failure points
- Maintenance teams receive actionable insights and recommendations
- Required maintenance work is prioritized based on actual equipment condition. Edge AI solutions are now appearing to deal with problems that are time-sensitive – such as safety
Read: ‘The Evolution of Predictive Maintenance Toward Prescriptive Solutions’
Benefits of a Predictive Maintenance Solution
Implementing a predictive maintenance solution can offer you numerous advantages:
Cost Optimization
- Reduce unexpected equipment downtime
- Minimize emergency repair expenses
- Optimize maintenance scheduling
- Extend the equipment life cycle
- Significantly lower overall maintenance costs
- Improved spare parts strategy
Operational Efficiency
- Maximize equipment performance
- Reduce production interruptions
- Improve overall equipment effectiveness (OEE)
- Enable data-driven decision-making
- Enhance production planning and scheduling
Safety Improvements
- Identify potential equipment failures before they become safety risks
- Reduce workplace accidents related to equipment malfunction – and by minimizing human-machine interaction
- Ensure compliance with safety regulations
- Protect workforce and infrastructure
Strategic Advantages
- Gain a competitive edge
- Improve asset management strategies
- Enable more accurate budgeting and resource allocation
Environmental Benefits
- Reduce waste from premature equipment replacement
- Optimize energy consumption
- Minimize unnecessary resource utilization
- Reduce waste caused by machine malfunction
Conclusion: Predictive Is Just The Beginning
Predictive maintenance represents a transformative approach to equipment management, offering organizations unprecedented insights into their operational infrastructure. By leveraging advanced technologies, manufacturers can unlock new levels of efficiency, reliability, and strategic performance.
As industries evolve, predictive maintenance will become essential for those seeking a competitive edge in an increasingly complex and technology-driven global marketplace.
Predictive Maintenance is a great start. But to go next-level, go prescriptive. Reach out to learn more.