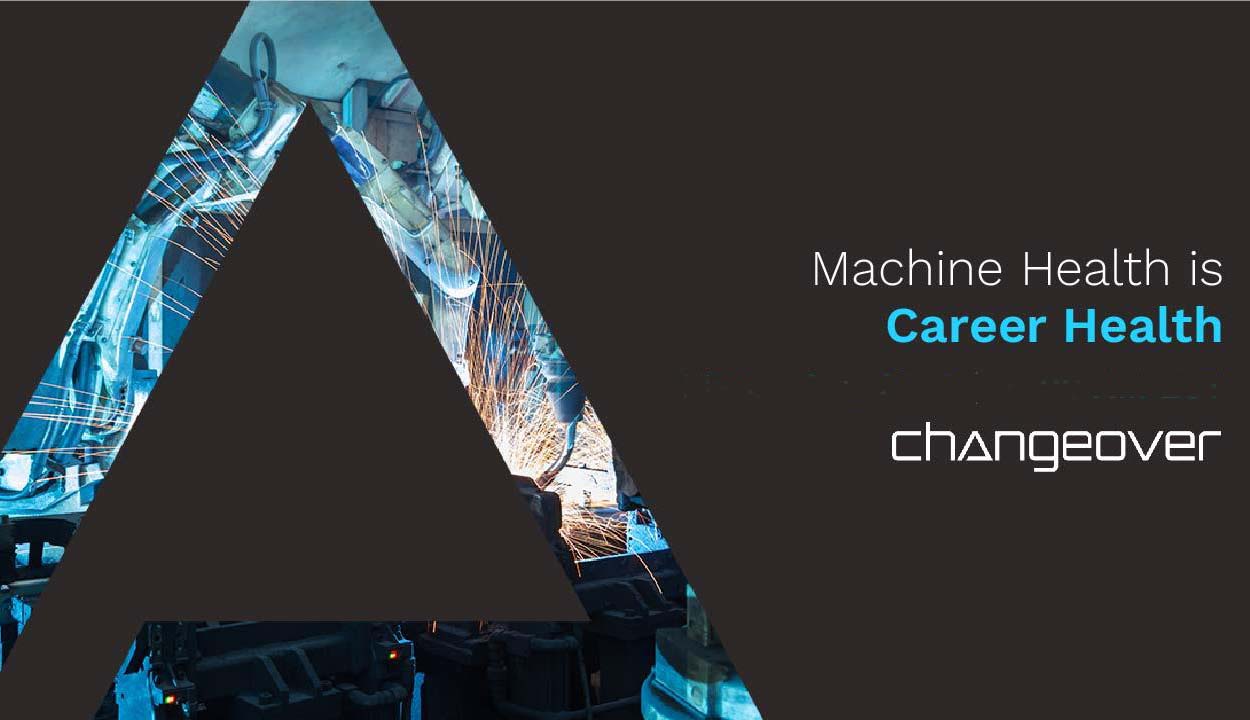
The second episode of ChangeOver – the home to the Machine Health Movement – deep dives into the state of Career Health. Expert guests include a legendary former VP of Manufacturing, his sons following in his footsteps, a MIT social scientist and the ‘Manufacturing Millennial’. Together, they chart out how current technologies not only improve operations but also work to create meaningful and lucrative career opportunities.
Manufacturing As Attractive Career Choice
Today, manufacturers face dual questions:
1) How can we fight the perfect storm of worker and skills shortages?
2) How can we inspire young people to join the manufacturing workforce – and make them as adept with a tablet as with a toolbox?
The answer for both is technology, according to ChangeOver host Jason Silva of National Geographic’s ‘Brain Games!’ fame.
“Technologies like machine health, AI and IIoT give frontline workers higher value and more interesting work, while supplementing overstretched and under-skilled teams and improving the quality of life on the factory floor,” says Jason. “New tech also allows manufacturing workers to gain digital skills that open up entirely new career paths. In other words, machine health really is career health.”
And such digital transformations are proving effective: “A recent survey of Gen Z manufacturing workers showed that 92% were satisfied with their jobs, and said those jobs pay well and have a strong technology focus.”
Watch the full episode on-demand now!
Home of The Machine Health Movement
The second episode of ChangeOver took place on 3 March 2022 with the title ‘Boots on the Ground, Heads in the Cloud: High-Tech Manufacturing Workforce’. While the first edition was a general overview on how machine health contributes to improving careers, businesses and supply chains, this 35-minute episode focuses on the current challenges related to the manufacturing workforce.
Industry legend Eduardo (Ed) Ballina and his two sons who followed in his footsteps are on hand to share their insights, along with MIT social scientist Ben Armstrong and ‘The Manufacturing Millennial’ Jake Hall. They all agree: with the right technologies backed by the right training, the future of manufacturing looks bright – for both manufacturers and workers.
A huge shout-out for all the folks that work in supply chain. They really are the heroes.
The Flying Ballina Family
It’s educational and entertaining to witness former PepsiCo VP for Manufacturing and Warehousing Ed Ballina talk shop with his two sons Eddie and David. In fact, they deserve their own reality show.
The two brothers followed their dad into manufacturing but only after taking their own circuitous routes – routes that were obviously not stress-free for their parents. “Actually, I think I committed an injustice,” says Ed, “pushing the idea that to be successful, you have to go to college, get a degree and run up mountains of debt.”
In the end, while many young people are lured by the simpler work and similar starting pay offered by the Amazons and Walmarts, the brothers were attracted to the challenges and salary potential of manufacturing. “At the end of the tunnel, you can make six figures a year as a mechanic in aviation. But yes, the startup is a little rough,” says Eddie.
Today, all three Ballinas are champions of machine health, with Ed bringing in the historical perspective. “I remember following around this guy, Bob Bauer. He would grab a broomstick and put one end on the bearing block and the other against his muffs. I realized he was using it as a stethoscope! It was vibration analysis, but the old-fashioned way. Now fast forward to today, we have sensors that can pick that information up, along with a lot of other info, and with a much higher degree of accuracy,” says Ed. “And now with all these Bob Bauers retiring, machine health is only going to be more important.”
The Ballina Family panel concludes with “a huge shout-out for all the folks that work in supply chain. They really are the heroes,” says Ed. “They work long hours with a lot of stress to get products on the shelves day-in-day-out. And they can’t Zoom it in.” The sons agree vigorously.
Getting Creative With Training and Upskilling
Ben Armstrong is a research scientist and interim executive director at MIT’s Industrial Performance Center, where he examines how manufacturing workers, firms and regions adapt to technological change.
Ben notes how manufacturing wages have not adjusted to inflation since the 1980s – and this is the main reason why the industry is largely “no longer upwardly mobile, stable, a path to the middle class”. He believes investment into new technologies, backed by the proper training, as the way to reestablish this upward mobility – while also working to replenish the workforce.
You can learn while you earn.
Traditionally, manufacturers have tried to minimize training their workers out of fear they’d be poached by competitors. However, Ben points to new forms of apprenticeships that may offer a workaround. For instance, the Alliance For Working Together in Ohio brings together mostly SMEs to share expertise and learning sessions to cut investment costs. It also stops poachers since “it essentially leads to them being ostracized from this community of manufacturers,” says Ben.
Ben also sees a lot of potential in Manufacturing USA, which links innovation institutes across the country. “It builds on American strengths,” says Ben. “Because it tries to mix the US competitiveness in R&D with manufacturing.”
The Light At The End Of The Tunnel: Manufacturing
“There is a lot of opportunity in manufacturing,” says Jake Hall – aka ‘The Manufacturing Millennial’ – during his rallying-cry conclusion. “You can learn while you earn. Meanwhile, manufacturers need to better communicate their purpose. No longer is it just this dark, dirty, dangerous and dull environment. The industry is in fact full of opportunity.”
The above article only touches on a few of the many offered insights during this edition of ChangeOver. So watch the full 35-minute episode on-demand.
And please follow ChangeOver where we will continue to chart out the Machine Health Movement.