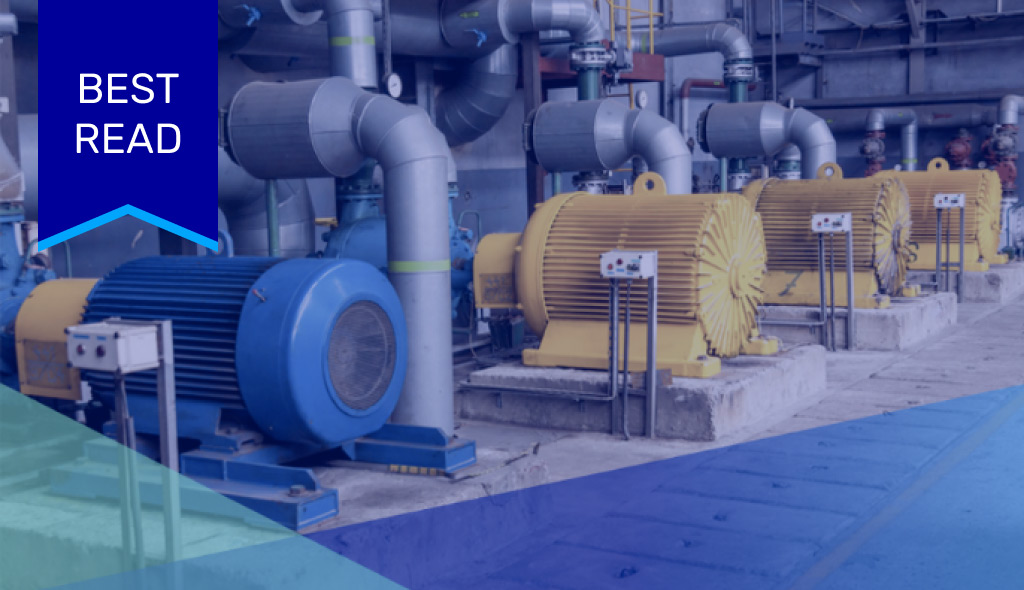
Machine downtime is a widespread problem in the industrial world — 82% of organizations have reported experiencing at least one unplanned outage each year and 45% of which were unable to provide products or services to customers as a result. Today, Machine Health solutions can be applied to make this problem go away.
This article was originally published on Jun 15, 2020.
If machine downtime is such a drawback on revenue and productivity, why is it still so prevalent? The issue lies in traditional means of machine maintenance. Facilities have relied primarily on two methods in the past.
Reactive Maintenance: Too Little, Too Late
The first is reactive maintenance. When workers notice symptoms of machine problems (such as poor quality outputs or machines breaking altogether), they reactively investigate the issue.
This reactive model is problematic because once workers know that a problem exists, the machines have already failed and product/output has already been affected. Downtime to repair failed or underperforming machines means stalled or halted production lines, reduced revenue, and an overall hit to productivity.
Preventative Maintenance: Too Much, Too Early
The second traditional maintenance method takes a more proactive approach. However it still fails to significantly reduce machine downtime. Preventive maintenance aims to catch problems sooner as workers perform maintenance tasks on a time-based schedule. But most machine failures are difficult to predict using solely operating hours or life cycles as a determining factor of when they need maintenance.
This preventative approach can also mean longer periods of downtime. If a machine begins underperforming shortly after its scheduled maintenance, it’s likely to continue underperforming — and perhaps even fail — before its next scheduled check.
Machine Health as the Key to Reducing Machine Downtime
What’s more, both of the above maintenance methods have been traditionally focused on responding to symptoms of machine underperformance or failure. Instead the focus should be on detecting potential issues before they arise.
In recent years, however, the industrial world has seen an increase in a third type of maintenance focused more on catching problems ahead of time: predictive maintenance. Predictive models use many different methods (including vibration, oil analysis, thermography, and ultrasound data) to predict and prevent failures by early indicators of machine malfunctions.
Predictive Maintenance: Right Amount, Right Time
Predictive maintenance gets us one step closer to solving the downtime problem. However, most facilities are still missing one link that can make the biggest difference: an approach emphasizing machine health. Route based predictive maintenance tools can alert workers of a problem at an early stage. And without continuous monitoring, workers must still come around to check the machines periodically to notice that something has gone amiss.
Even if you have sensors mounted on a machine, if they aren’t advanced enough, they may not automatically diagnose the issue. Hence, these sensors won’t provide maintenance teams the root of the issue, or suggest ways to fix it. So in the end, they’re more like a check engine light.
Confronting The Three Core Causes of Downtime
Machine health, on the other hand, is a framework that elevates predictive maintenance with continuous machine health monitoring. Powered by the IoT and artificial intelligence, this framework can alert workers at the exact moment when issues are detected. It can also provide facility teams prescriptive diagnostics of what’s been detected, and how to fix it.
To get a sense of how machine health could fit into your operation, consider how it addresses the following core causes of machine downtime to keep factories firing on all cylinders:
- Mechanical problems: Sensors perform continuous machine health monitoring to track temperature, vibration, and magnetic data. AI-based algorithms analyze the data and automatically diagnose malfunctions based on changes in this data. Workers are immediately notified of any changes in a machine’s health status with alerts telling them not only why the machine is malfunctioning, but also how to correct the root cause behind the problem.
- Design problems: Continuous machine health monitoring can reveal when individual machines undergo extra amounts of stress due to inefficiencies within the production facility’s design. Smoothing out those points of friction starts by identifying where they are and why they exist, which then leads to facilities that experience fewer issues of all kinds. As a result, facilities can avoid unplanned downtime, delays, bottlenecks and inconsistent product quality.
- Operational problems: Your machine design might be perfect, but humans never will be. As people make modifications to machines, they can unknowingly create additional issues. Machine health technology can create an archive of changes and modifications so you can verify or validate which activities lead to disruptions.
Seize the Day
Unplanned downtime in manufacturing is an inevitable phenomenon. But even planned downtime can hinder your productivity. Nothing can stop these issues altogether, but taking steps to reduce downtime now can have a big impact on your revenue and productivity in the future.
So stop solving problems after they’ve already happened, and start taking a real-time approach to keeping your machines healthy.
Read more about Industry 4.0 Use Cases Enabled by Machine Health.