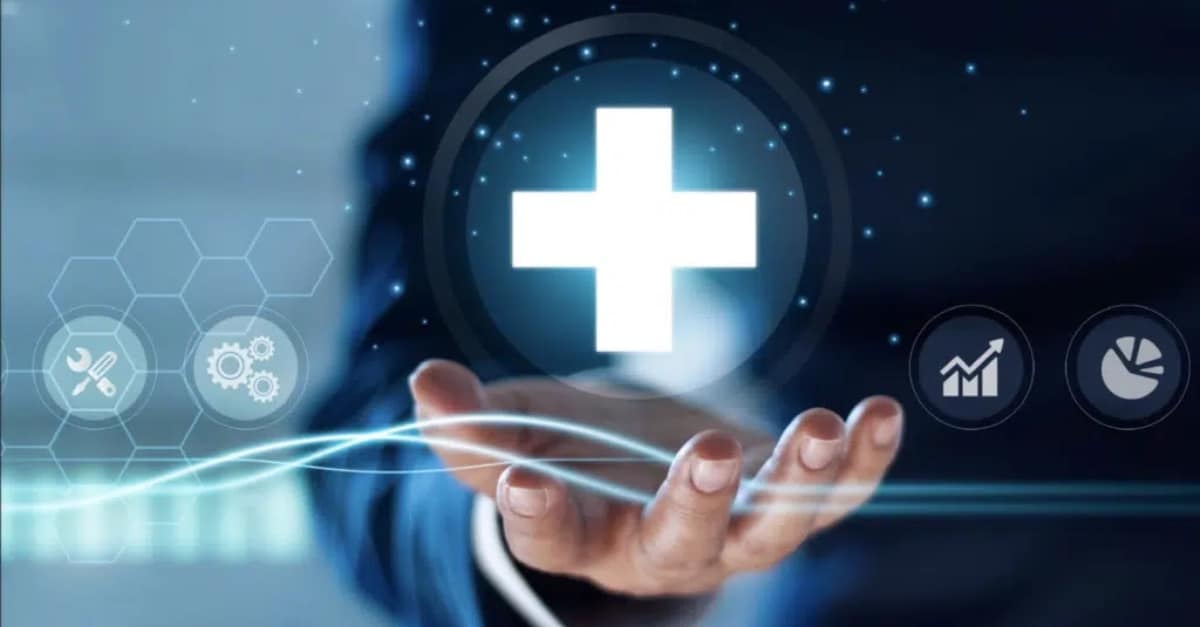
More manufacturers are investing in advanced tech to confront challenges around workforce, downtime and fluctuating demand, according to a new report from Plant Services. “The technology is there and it works,” says one industry pundit. “The work now is more about bringing your people and culture up to speed. And at one point, the benefits will go exponential.”
How Healthy Is Your Machine Health Program?
“Manufacturing leaders faced with workforce and economic challenges are leveraging advanced monitoring technologies to manage plant health,” opens the recently released report ‘2023 Machine Health Is Business Health’.
These findings arose earlier this year, when Plant Services surveyed 171 corporate and plant-floor managers about what they’re doing in 2023 to face down the current economic landscape. Questions included:
- What are your peers most concerned about for the rest of the year?
- What tools and strategies are they deploying to optimize machine health and overcome skills gaps?
- How does your team compare?
Download report: ‘2023 Machine Health Is Business Health’.
Plant Services editor-in-chief Thomas Wilk hosted a roundtable webinar to explore the report’s findings. To discuss the industry’s biggest pain points and the technology strategies being used to address them, he was joined by two industry veterans backed by decades of experience bringing innovation to the factory floor: Alvaro Cuba Simons (Strategic Business Consultant & Advisor, Operations & Supply Chain) and Terry LeDoux (Former VP of Digital Manufacturing at Nestle Purina Pet Care).
‘Think Big, Start Small, Scale Quickly’
Predictably, supply chain breakdowns and workforce gaps led the report’s list of headaches – with the fear of unplanned downtime and recession always lurking in the background. What’s more surprising about this report is how manufacturers seem more ready to invest in technology to deal with these challenges.
Wow, I can do this in 90 days in one factory and then scale to 21 sites in 12 months.
“The problem is actually solved,” says Alvaro. In other words, manufacturers no longer have to accept unplanned downtime as the price for doing business. And happily, more manufacturers are becoming aware of this fact. Unfortunately, there’s still a lot of implementation to be done: only 11% of the report’s respondents say they experience unplanned downtime rarely or never.
“Ten years ago, there were already a lot of tools out there,” says Terry. “But they were hard to implement, very expensive and took a long time to have an impact. Now we’re like ‘Wow, I can do this in 90 days in one factory and then scale to 21 sites in 12 months.’ So, my advice is: ‘Think big, start small and scale quickly’.”
Connected Workforce
Meanwhile, tech and workforce remain intrinsically linked. “I can have all the machines in the world but I still need people to take care of them,” says Terry. And many manufacturers are currently feeling both a worker shortage and a skills shortage.
One way to alleviate the pressure of recruiting new talent is by retraining those people you already have. “We can do more with less people by enabling them with digital tools. If you give workers a mobile platform that gives them access to information and knowledge while they are anywhere in the factory, they will use it,” says Terry. “So, my first investment is the connected workforce. That’s my go-to. As for the workforce itself, it’s not either/or. You will also have to think about the new talent you are bringing in.”
It’s not just turning wrenches all the time. It’s about getting more done with less effort and winning every day.
“And I think that the technology can also work as a recruitment tool,” says Alvaro. “As the older generation is retiring, the younger generation is coming in and they are born with that technology – and they want that technology!”
“It’s not just turning wrenches all the time,” says Terry. “It’s about getting more done with less effort and winning every day.”
Picking The Right Partners
Alvaro and Terry both emphasize the importance of picking the right partner when bringing in a machine health solution. “Pet food is my specialty,” says Terry. “I’m not an AI guy. It’s not my job to create a team of 100 people to be able to do that. So, you need to bring in the right partner.”
ROI is so fast, it actually becomes an operating cost.
“We’re talking thousands of sensors, deployed and immediately reading and providing information,” says Terry. “And having this information turned into something actionable: getting prescriptive actions you can take when there’s a problem and before it becomes a downtime event. So, it would be crazy to do it alone in today’s environment with the technology that’s available.”
“Plus, you don’t even have to look at it as capital expenditure,” adds Alvaro. “ROI is so fast, it actually becomes an operating cost,” adds Alvaro. “And if it makes my life easier, why not?
Beyond Eradicating Unplanned Downtime: Exponential Payback
“You should always start in machine health,” says Terry. “It’s here you need to change the mindset of your people. And from there as you branch out into process health and beyond.”
“The real magic will happen when I get my machine health data and my process health data into the same data lake,” says Alvaro. “There are huge wins waiting when you start to understand the problems in different ways. It’s an enormous opportunity. Once again: the technology is there and it works.”
Download the report: ‘2023 Machine Health is Business Health’.
Watch on-demand: ‘Roundtable: Results from “2023 Machine Health is Business Health” report’.