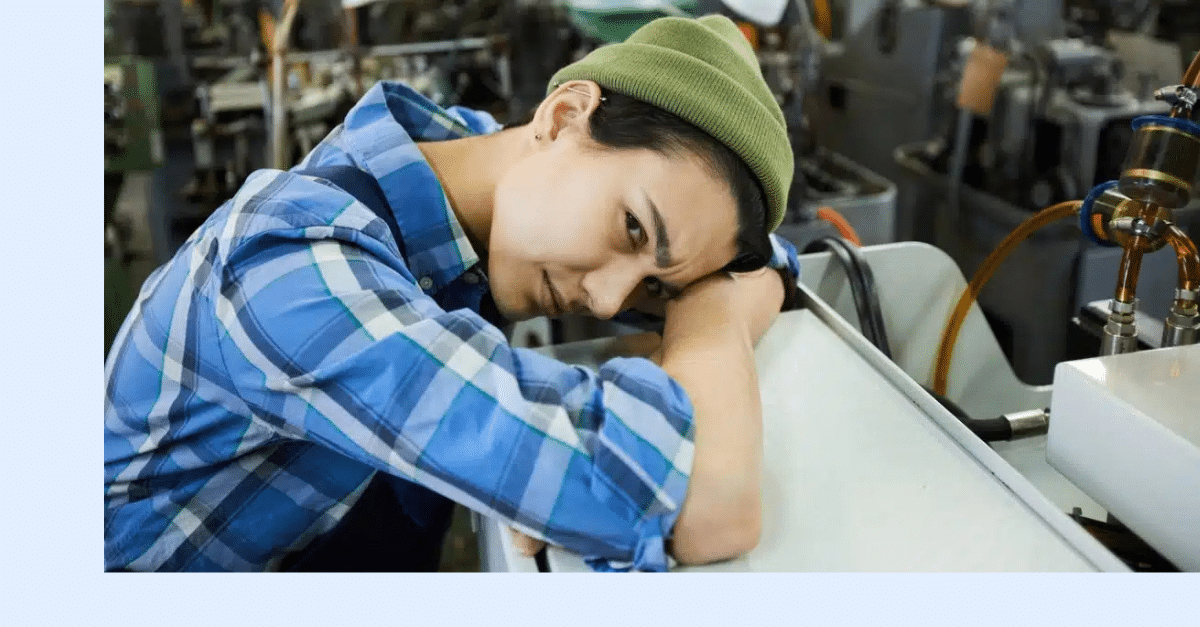
Reactive maintenance remains a surprisingly common approach for many organizations in industrial maintenance. This comprehensive guide explores the intricacies of reactive maintenance, providing insights into its potential benefits and significant limitations.
Reactive maintenance is most often described as “fire-fighting”: when something goes wrong, you try to fix it quickly. While it’s great that it’s being fixed, it’s less great that productivity has ground to a halt in the meantime, and workers often have to perform riskier, dangerous work. But thanks to emerging—and many more established—technologies, reactive maintenance can be thrown in the dustbin of history.
Unfortunately, it’s still a very common maintenance strategy across industries. Why?
What are the Advantages of Reactive Maintenance?
Despite its limitations, reactive maintenance does offer some short-term benefits:
- Lower Initial Costs
- Minimal upfront investment in maintenance infrastructure
- No need for advanced monitoring systems
- Reduced initial technology and training expenses
- Straightforward Implementation
- Easy to understand and execute
- No complex planning or predictive analysis is required
- Minimal training needed for maintenance staff
- An option for non-critical or low-impact equipment
- Minimal Administrative Overhead
- Reduced paperwork and documentation
- No need for complex maintenance scheduling
- Limited planning resources required
What are the Disadvantages of Reactive Maintenance?
While seemingly convenient, reactive maintenance presents significant challenges:
- Increased Long-Term Costs
- Higher emergency repair expenses
- Unexpected equipment downtime
- More extensive damage from delayed repairs
- Significantly higher total cost of ownership
- Potential for catastrophic equipment failure
- Operational Disruptions
- Unpredictable production interruptions
- Extended equipment recovery times
- Reduced overall operational efficiency (OEE)
- Negative impact on production schedules
- Potential loss of customer confidence
- Safety Risks
- Higher probability of workplace accidents
- Increased risk of equipment-related injuries
- Potential non-compliance with safety regulations
- Compromised worker protection
- Higher insurance and liability risks
- Equipment Reliability
- Accelerated equipment degradation
- Shortened equipment lifecycle
- Increased wear and tear
- Reduced overall equipment performance
- Higher replacement frequency
Read: ‘Predictive Analytics No Longer Cuts It. Long Live Prescriptive’.
What are Alternatives to Reactive Maintenance?
Organizations have many different, more advanced maintenance strategies, which are also becoming increasingly blended depending on the criticality of a particular machine and the specific use cases the manufacturer is going after.
- Preventive Maintenance means more regularly scheduled inspections and systematic equipment serving. Benefits include:
- Proactive component replacement
- Reduced unexpected failures
- Lower long-term maintenance costs
- Predictive Maintenance includes advanced sensor monitor and real-time machine monitoring to generate AI analytics. Benefits include:
- Precise maintenance scheduling
- Minimal unnecessary interventions
- Condition-Based Maintenance requires continuous monitoring for data-driven maintenance decisions. Benefits include:
- Immediate issue detection
- Optimized maintenance resources
- Enhanced equipment reliability
- Reliability-Centered Maintenance includes comprehensive system analysis and strategic maintenance prioritization to manage equipment. Benefits include:
- Holistic performance optimization
- Advanced risk management
- Prescriptive Maintenance is the next stage of predictive maintenance, with AI insights that instruct what to fix and when. Benefits include:
- Reduces Downtime
- Optimizes Maintenance Costs
- Improves Equipment Performance
- Enhances Safety
Conclusion: Reactive Maintenance Should Go The Way Of The Dodo
While reactive maintenance might seem convenient, it represents a short-sighted approach that can significantly impact an organization’s performance, safety, and financial health.
By transitioning to more advanced maintenance strategies, businesses can transform maintenance from a cost center into a strategic value generator, driving innovation, efficiency, and sustainable growth.
Read ‘Why The Confusion? Prescriptive Maintenance Vs Predictive Vs Preventative’.
Or reach out and contact us.