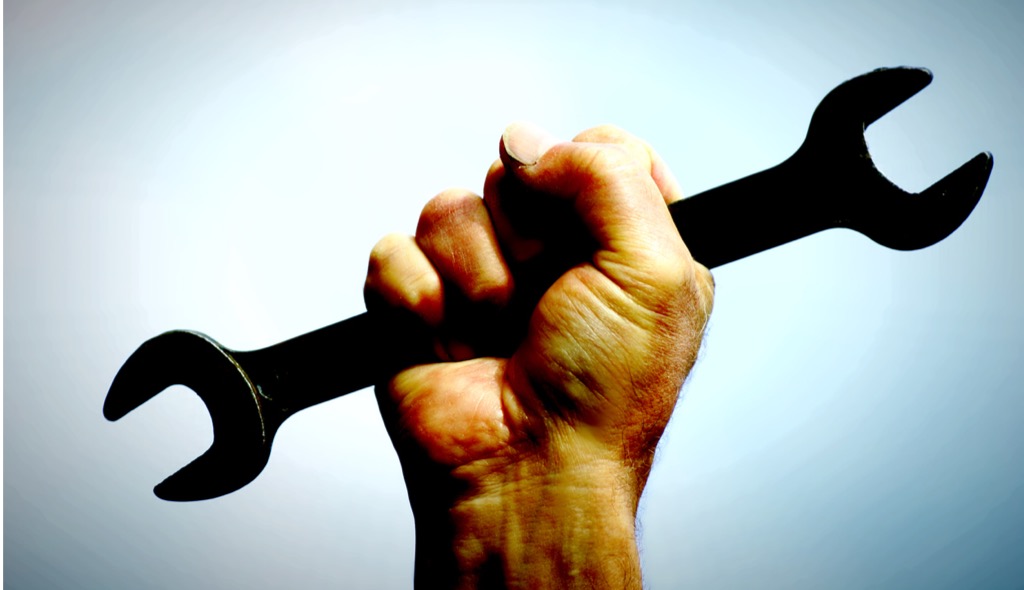
Augury not only listens to the machines that matter, but also the maintenance teams that keep these machines healthy 24-7-365. Their input has helped streamline our user experience. As a result, they can use our prescriptive diagnostics platform quickly and intuitively to understand what’s wrong and how to best fix it. A year of UI enhancements later, we’ve hit 90% engagement rates for factory floor workers – whether they’re in the plant or working remotely.
A Search for Clarity: From Data to Action
“With supply chains destabilized and increased remote working, there were enough variables at play,” recalled one maintenance manager from a major manufacturer. “We needed to focus on our job: keeping those machines that matter running.”
Indeed.
It was March 2020. Like most companies at the time, Augury was out for a rethink: we had to find new ways to help our clients keep their machines going. As we engaged with our customers to dig deeper for their true needs, we realized they were – like all of us – looking for clarity.
Our sensors and AI were already producing out-of-the-box diagnostics for any number of machines. However, making this information available in the most intuitive and actionable ways possible had now only become more urgent.
A 90% Engagement Rate
With a clean user interface making it clear what to do next, the results have been dramatic. By actively collaborating with our users over the past year, we have streamlined and enhanced our platform with UI releases. This has resulted in reliability and maintenance managers responding to a record-breaking 90% of Machine Health alerts and notifications.
Since we can provide insights within a day of deployment and often see maintenance teams make the first machine improvements based on these insights within a week, users quickly realize they have a new and powerful array of tools to help them do their job. Customers often achieve full ROI within three months.
“Augury isn’t a program. Programs end,” observed an operations manager at NEFCO Biosolids. “Augury is a culture. And this culture is saving downtime, money, and negative environmental impact at scale.”
Get The Right Information in The Right Format
As the Augury team dove deep into our users’ needs in the face of challenges both old and new, we saw our own challenge more clearly. “How can we better empower those on site – or across sites, or even remotely – with the right information and in the right format so they could do their jobs as efficiently as possible?”
Answering this question is now part of our process, with four key focus areas:
- Making the UI features more streamlined and intuitive
- Enhancing real-time machine health insights, features and tools to make maintenance jobs easier to plan and execute and more predictable and successful
- Increasing knowledge sharing and best practices through in-app collaboration tools
- Supporting a global customer base
Sharing is Caring
An enterprise-level view is paramount – particularly in times of crisis. “When machines are having issues, we can share those learnings between our facilities. This assures that they’re taking those learnings and applying for greater expertise and autonomy at the plant level,” observed Warren Pruitt, Vice President of Global Engineering Services for Colgate-Palmolive.
“Augury allows for better collaboration. Team members can be in different locations but still looking at the same data. It feels like we are all there looking at the same machine,” said a plant manager.
Made for Humans by Humans
We at Augury will continue to invest in new platform tools and capabilities based on users’ feedback that empower them to act, improve, plan, make informed decisions and prevent failures.
“You can log in from anywhere and review the health status of all your connected machines to really get a good overview,” said one of our clients. “It’s not just an alarm. They actually point us where we need to look for our problems – instead of just showing a red/yellow/green state.
We are indeed very much more than a condition-based machine monitoring platform. We’re a real-time Machine Health action platform providing fault diagnosis and remediation insights – and backed by our easily accessible Success and Reliability team.
And we say this: we’ve only just begun…
Learn more about empowering your team with Augury’s Machine Health as a Service platform by reading our white paper Driving Machine Health Adoption Through an Empowering User Experience. Sign up here to view our on-demand webinar and platform demo.