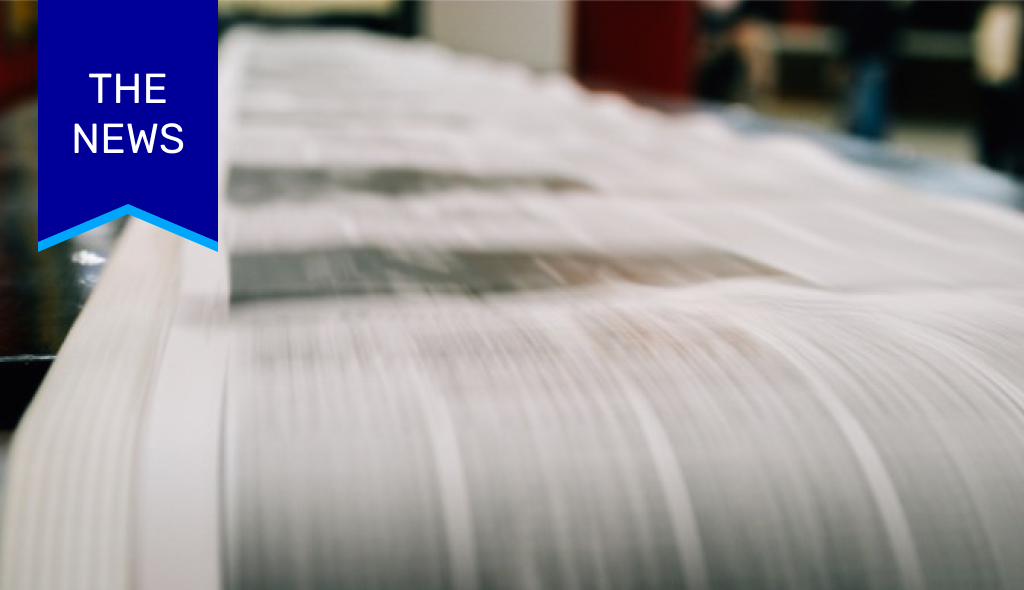
You may have already heard about ‘levelling up’ and ‘the manufacturing gap’, but what about ‘robot wranglers’ and ‘4D printing’? Recently, many new catchphrases seem to be appearing in manufacturing-related news. Here’s a round-up of some arising concepts that caught our eye – and why they (might) matter.
You may have already heard about ‘levelling up’ and ‘the manufacturing gap’, but what about ‘robot wranglers’ and ‘4D printing’? Recently, many new catchphrases seem to be appearing in manufacturing-related news. Here’s a round-up of some arising concepts that caught our eye – and why they (might) matter.
‘Levelling Up’ / ‘Robot Wranglers’
In a recent speech, UK PM Boris Johnson announced: “This government is obsessed with skilling up our population.” By “levelling up” vocational education in the areas that most need it, he hopes to build a larger high-skill work force. And as a result, the country can better compete with more established rivals such as Germany and Japan.
“Unfortunately, the world is moving on. In the factories of the future, the role of skills will be dramatically different. We are in the early stages of what is known as industry 4.0: digital manufacturing that attempts to automate and regulate every aspect of production, including the human. There is little sign that the UK government is thinking about this,” according to ‘Factories Of The Future: We’re Spending Heavily To Give Workers Skills They Won’t Need By 2030’.
In other words, the levelling up will be more about infrastructure than people. “Of course, there will still be opportunities for workers who can work with the new technology – ‘robot wranglers’ as they’re being described. New jobs may be created in these areas, and those who are able to fit the criteria stored in skills clouds may be able to fill them.”
Robot wranglers?!? Now that sounds like a much more enduring catchphrase than “levelling up”.
Seriously: Yeehaw!
‘Systems of Systems (SoS)’
It may have an unfortunate acronym – SoS – but Systems of Systems technologies seem set to have a large impact on healthcare, retail, autonomous driving and – yes – manufacturing, according to ‘Systems Of Systems: The Next Big Step For Edge AI’.
“Leveraging the growing power and ubiquity of CPUs and neural processing units, edge AI can process growing haystacks of data right where they’re being created, finding their needles quickly for local or remote processing.”
The end goal is to have all involved digital parties chatting with each other using a single language. The SoS will serve as the superstructure that “uses AI to coordinate and aggregate data processed at the edge from these different systems.”
While opportunities abound, challenges remain. Those applying AI to healthcare are very familiar with two of the main problems: how do you standardize information while ensuring trust and privacy? There’s also the difficulty in then harmonizing the local data with the big data to produce useful actions.
But yes: early days.
‘Shared Manufacturing’ versus ‘IP Leakage’
Research institutes are already regularly sharing access to high-cost machines, so why not manufacturers? And indeed some companies are already doing it, according to ‘Manufacturing In The Sharing Economy’.
“This ‘try before you buy’ model is gaining traction in other areas of manufacturing, especially as the pace of innovation and automation accelerates, thanks to the growing adoption of digital manufacturing. Let’s face it: Keeping up with groundbreaking manufacturing advancements in materials science, 3-D printing and flexible hybrid electronics, just to name a few, is a CapEx-intensive endeavor. In most instances, it’s far easier and less risky to adopt a shared-cost usage model.”
But yes, more efforts are needed to avoid “inadvertent IP leakage”.
‘The Manufacturing Gap’
Why is Tesla the only major tech manufacturing company to emerge from the U.S. in the past decade or so? Why have politicians been trying and failing since the Clinton administration to turn the U.S. into a powerhouse of clean-energy exports?
“The culprit is a frustrating and persistent shortcoming of the American economy. You could call it ‘the manufacturing gap’,” according to ‘The Bill That Could Truly, Actually Bring Back U.S. Manufacturing. And Help The Climate, Too’.
“New technologies fall into a ‘valley of death’ between conventional R&D and commercialization. Their inventors either license the technology abroad or go bankrupt.” In other words, “the U.S. financial system isn’t very good at funding things that have very modest returns and take a long time for those returns to be realized.”
So why did Tesla succeed? Elon Musk came in with his own money.
But there’s good news: Congress may be set to pass a bill that would establish an Industrial Finance Corporation. This bank could bridge the gap and in the process accelerate American decarbonization efforts.
“Many of the biggest improvements to a given technology happen not in a university lab, but on the factory floor, in an exchange of knowledge between engineers and machinists called ‘learning by doing’. The U.S. lost its lead in the solar-panel industry not because it was outspent on R&D (it wasn’t), but because it outsourced solar production abroad and failed to build up expert ecosystems of inventors, designers, and workers. The same dynamic has played out in the semiconductor industry.”
‘4D Printing’
3D printing had decades of hype cycles as “the next big thing” before it actually had market impact. Now a whole new hype is arising. Welcome to the fourth dimension: time.
“This means that the printed material, once ready, will be able to modify, transform or move autonomously due to its intrinsic properties that respond to environmental stimuli,” according to ‘4D Printing? Bridging Additive Manufacturing with Smart Materials’.
MIT is currently collaborating with Stratasys (the 3D printer and systems manufacturer who are coincidentally promoting their own evocative catchphrase ‘Mindful Manufacturing’). They seek to go beyond “passive, inanimate materials like brick, steel and glass” to “so-called ‘smart materials’ which move autonomously – swelling, shrinking or bending in reaction to a stimulus”.
Think: pinecone. This naturally intelligent material only opens when the time is favorable for seed germination.
“If history shows that it’s not the strongest that survives, but the one that adapts best to change, 4D printing with smart materials seems like something to consider.”
Tune in next month when we explore the ultimate catchphrase: ‘The Manufacturing Metaverse’.
Meanwhile, you can read ‘Manufacturing – The News, July 2021’.