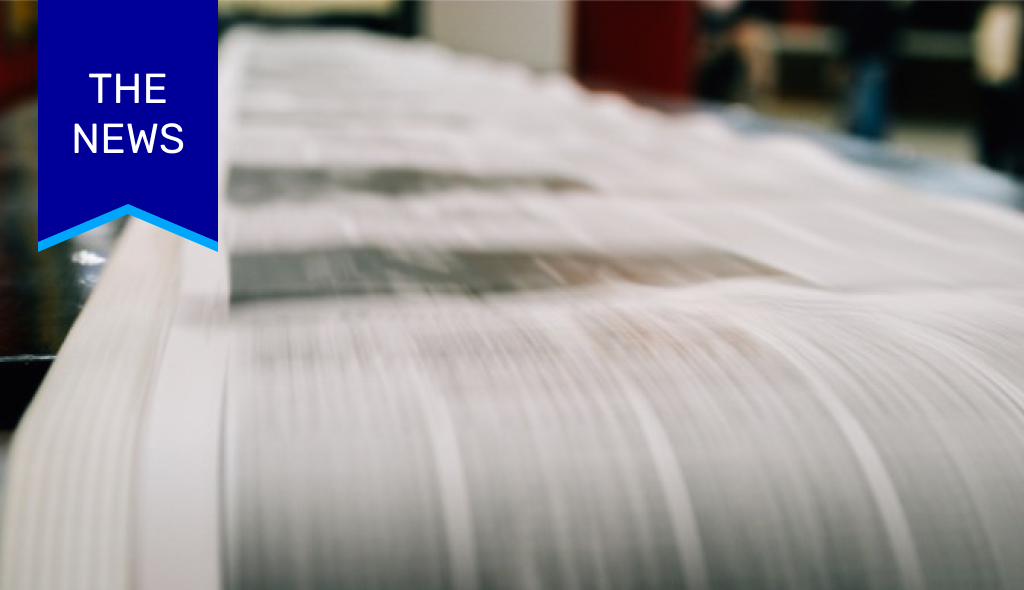
Manufacturers already had to rethink their supply chains in response to COVID-19. Now, many must start over in the face of the Russian invasion of Ukraine. Read all about it…
The Many Costs of War
Many lives will be lost or changed forever by the Russian invasion of Ukraine. The long-term impacts of the invasion on businesses, markets, and supply chains outside the region are harder to judge.
But that hasn’t stopped the experts from trying. Gartner has already published ‘How to Manage Ukraine’s Effect on Your Supply Chains’, which is now being referenced in the endless stream of current ‘What now?’ articles.
In short, we can expect severe shortages of hydrocarbon, critical minerals, metals and energy. And the prices for these will likely spike and in turn impact manufacturing operations up- and downstream. Logistics will need rethinking as sea, rail, road and air routes are disrupted. Cyberattacks on strategic supply chains and infrastructure will increase. Russia may even try to weaponize food supply chains since together with Ukraine it controls one-third of the world’s wheat exports, 16 percent of the world’s corn exports, three quarters of the world’s sunflower oil exports, etcetera…
Indeed: it’s all still too huge and too soon to fathom.
True Words That Only Ring Truer
Until the news of the invasion, we had collected some inspiring articles on how manufacturers can best deal with their current pain points. For instance, ‘Opinion: Why manufacturing workers are voluntarily leaving jobs at rates never seen before’ argues workforce challenges could be met by not only increasing wages and training opportunities, but also through actively showing flexibility and respect.
Meanwhile in ‘Balancing the Manufacturing Ecosystem in a Globalized World’, the World Economic Forum explains how diversifying risk can rebalance supply chains to be more resilient, sustainable, cost-cutting and inclusive.
And ‘The 10 Biggest Future Trends In Manufacturing’ gives a rather savvy rundown of the technologies – from IIoT to predictive maintenance to digital twinning – that can help manufacturers become more future-resistant.
With current geopolitical realities, these articles will likely prove to be only truer as we move forward. After all, the pandemic did work to push through many innovations that may have otherwise taken years or decades instead of months.
So, do we just need to double-down?
The End of Lean?
One story keeps resonating: ‘Auto Industry Considers Tearing Up Manufacturing Playbook After Border Protests’.
The article covered the dilemma of US auto manufacturers as they evaluated the impact of the border blockades related to the Canadian trucker protests. Some car manufacturing leaders are now considering overhauling the iconic “lean manufacturing” approach.
“Over the past three decades, manufacturers have adopted ‘lean’ manufacturing. Largely lifted from the Toyota production system, the complex strategy relies heavily on things like automation and other labor-saving steps. But the centerpiece is a system known as ‘just-in-time’, or ‘JIT’, production, which has sharply reduced the amount of inventory maintained at automotive factories. That approach, it turns out, is extremely vulnerable to disruptions that can quickly bring factories to a halt.”
“Until recently, JIT and lean manufacturing appeared to be the most effective way to produce goods since Henry Ford switched on the first moving assembly line in 1913 […] Now, with everything that’s happened, including COVID, the semiconductor shortage, geopolitical risks and other events,” many believe it’s time for a radical rethink.
And to think: this rethink was inspired by a few blocked bridges. Imagine the rethink required now that countless bridges are burning.
Meanwhile, let’s get to work building bridges towards each other.
People first.
Read: ‘Manufacturing – The News: Welcome to The Age of Paradigm Shifts’.