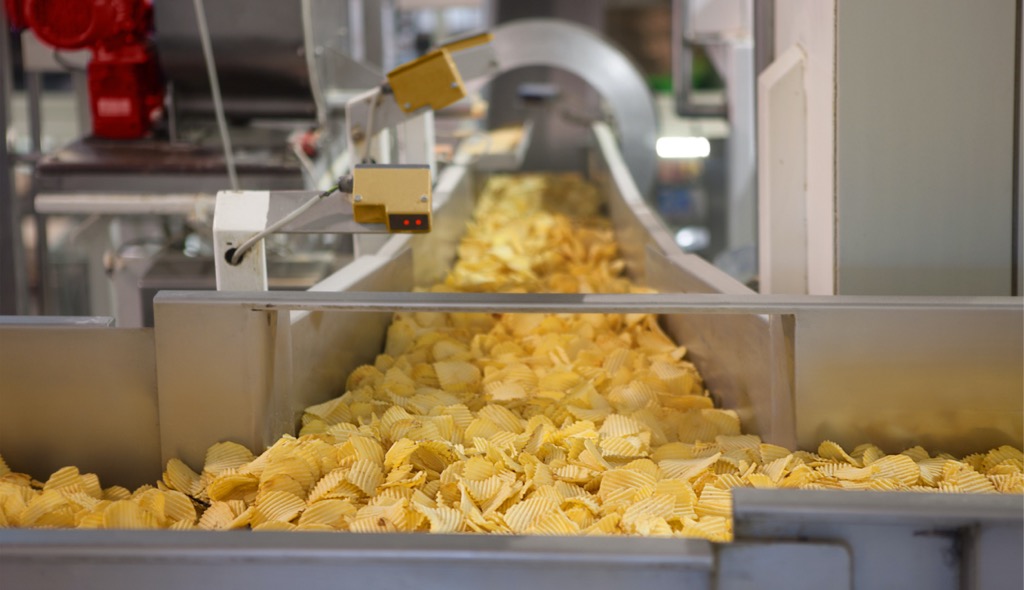
Food manufacturers can now use Industry 4.0 technologies such as Predictive Quality to anticipate and proactively address problems before they arise – boosting yield, efficiency and revenue in the process.
The Case For Predictive Quality
Food quality has always been a critical factor in the food production process. Food manufacturers are required to abide by stringent quality regulations, inspections and statistical quality control methods.
The impact of poor food quality is severe, with direct bottom-line consequences. Poor product quality reduces production yield, can damage the company’s brand and reputation. More immediately, quality issues are one of the most common causes of production losses for food manufacturers, together with other, largely process-driven losses such as waste. These losses translate into a significant dent in yearly revenues.
Conversely, meeting high-quality standards can reduce manufacturing costs – internally and externally. Internal costs emerge from problems associated with the product before it is delivered (e.g., shortages, waste, and delays). External costs arise post-delivery – through recalls, lawsuits and warranty costs – and constitute a major expense for the food industry, resulting in a staggering $7 billion loss annually.
Food manufacturing operations turn to processes and tools to sustain high-quality production in addressing regulatory compliance, risk prevention, and product traceability. While tools such as statistical quality control (SPC) have been used since the early 1920s to identify issues as early in the manufacturing process as possible, they deal with problems that have already occurred.
Predictive Quality is an emerging category of Industrial Artificial Intelligence solutions, that provide manufacturers with the means to significantly reduce process-driven losses in quality and waste, by pinpointing the root cause quickly and with a high degree of confidence, and preventing those losses before they next occur.
Defining The “Quality” In “Predictive Quality”
In the food industry in particular, “quality” can mean a number of things. For example, there are laws governing food quality in many countries. There are also international regulations which are important regarding globalization and the increasingly complex food supply chains. These laws and regulations assure food safety and a minimum level of quality for the health and overall benefit of consumers.
While certainly a very important topic, this is not the quality challenge that Predictive Quality addresses. Rather, Predictive Quality tackles production losses caused by inefficiencies in the process itself (rather than due to individual assets, for example).
In fact, Predictive Quality isn’t limited to quality-related losses, but also addresses other common process-based production losses. In the case of the food industry that typically includes waste and yield. In other industries, Predictive Quality addresses anything from throughput, to emissions levels to energy consumption. The common thread is that these are all losses which – like the consistent quality and waste losses experienced in food manufacturing – are caused by process inefficiencies.
Industry 4.0 and Predictive Quality To The Rescue
Fortunately, food factories can overcome many of these quality control hurdles with the use of Industry 4.0 technology, specifically predictive quality.
Predictive quality technology provides manufacturers with 3 key capabilities to optimize their processes, thereby minimizing losses due to quality issues, as well as other process-driven losses (waste, yield, etcetera).
- Automated root cause analysis
Predictive Quality provides the process engineer with the tools to reveal previously unknown root causes of quality issues in the production line, via automated root cause analysis. Most food production lines have certain recurring losses that can’t seem to be traced to any specific visible cause. This is particularly true for more complex food production processes. That’s because with so much complex data to analyze, process engineers and experts are largely left to follow their intuition in selecting which of the hundreds, even thousands, of data tags to investigate.
Naturally there will always be a blind spot – and the more complex the inefficiency, the less likely even the most eagle-eyed process expert is to find it. By contrast, a predictive quality solution uses Artificial Intelligence to do what human beings can’t: continuously analyze all the relevant data (ERP, MES, Quality systems, data lakes, etcetera) at scale – including complex interrelationships between the different data tags. This provides process experts with the ability to pinpoint the precise combination of factors that are causing a particular quality problem, no matter how complex.
- Predictive recommendations
A key component of Predictive Quality is predictive recommendations. Predictive recommendations use the insights from root cause analysis to identify the optimal process setting. This will enable manufacturing teams to minimize quality issues as much as possible.
Through continuous, multivariate analysis of production data, predictive recommendations will provide the precise optimal range of values for any given combination of tags. - Proactive Alerts For Real-Time Action
Of course, all of this intelligence must be translated into timely action to provide real value. Proactive alerts are delivered directly to production teams in real-time, as soon as a process inefficiency emerges – i.e. a problematic combination of tag behaviors, as identified by the predictive recommendations. This enables front-line manufacturing staff to act to prevent losses before they occur. Ideally, the alert should include as much actionable information – for example, not only identifying the problem, but also providing clear Standard Operating Procedures for addressing them.
Predictive Quality empowers quality teams to anticipate and proactively address quality problems before they arise – making sense of complex data patterns to determine areas of greatest quality risk and assign production floor resources before risk becomes reality.
The business gains of Predictive Quality are clear and compelling, providing food manufacturers with a competitive edge in an era where every last drop of efficiency counts.
Want to learn more about how food manufacturers are succeeding in drastically reducing quality and waste losses? Reach out.