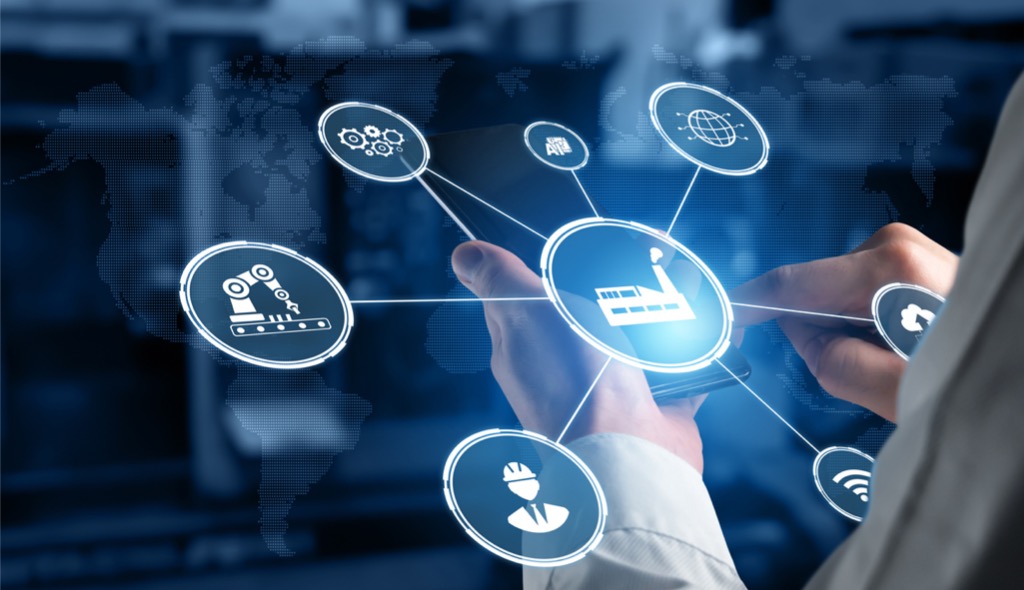
Innovation is often driven by a singular use case — one invention so revolutionary that widespread adoption is inevitable. Production Health is here to drive that change. It combines AI-driven insights across machines, processes, and operations to create a more holistic view of production lines than ever before.
The first American Industrial Revolution was defined by the invention of the cotton gin in the late 18th century. It was a tipping point in manufacturing as cotton mills began to spring up throughout the Northeast and farther south along rivers and streams. Infrastructure followed, creating transportation systems like railways and canals as commerce and trade proliferated. Then we had the Edison light bulb, which drove electrification, and then the electric motor pushed industrial adoption. With each industrial revolution iteration, a singular use case — the gin, the lightbulb, the motor — forever changed the landscape of manufacturing.
What’s starting the next industrial revolution?
So, what is the metaphorical cotton gin of today?
The answer is in artificial intelligence (AI) — more specifically, the Production Health that AI enables. AI in manufacturing has led the way through Industry 4.0, but reaching the horizon, where Industry 5.0 awaits, hinges upon using predictive maintenance technology to continuously monitor machine health, both historically and in real time. These provide both holistic and in-depth views across the entire production line to optimize the manufacturing process.
Leveraging these insights, manufacturing leadership can reduce overhead and increase profitability. Then, they can work on Process Health: reducing waste, increasing throughput and yield, and improving the sustainability of the production line. Combined with Machine Health, we call this process Production Health — an innovative combination of AI-driven insights into the interdependence of machines, processes, and operations.
Related: Learn more about driving digital transformation in manufacturing.
Why is Production Health so essential to reach Industry 5.0? Consider the environment today’s manufacturers operate in. The industry also suffers from worker shortage, which is overall holding things back as manufacturing surpasses pre-pandemic levels with an expected 4.1% GDP growth for 2022. On top of that, there are more people in the world than ever before — meaning manufacturers must meet greater demand. Unfortunately, this also means more waste, both in terms of defective products and pollution.
Production Health can drive major improvements to solve these problems. With a holistic view into multiple aspects of your production, process-driven objectives can be met while also cutting down downtime and maintenance costs. And all that optimization leads to higher quality and yield and reduced waste and emissions.
How Production Health Leads to Industry 5.0
Manufacturing processes 20–30 years from now will be so refined that it’ll be unthinkable not to have the process sub-optimized to report exactly what’s needed based on raw materials, demand, equipment reliability, and other variables. But the greatest change is that unlike 4.0, which is marked by efficiency and automation, 5.0 adds another pillar: the human touch. As repetitive tasks are increasingly left to automation, people have more time to focus on higher-level work, personalization, and thinking outside the box.
This collaboration between human expertise and machines — hybrid intelligence — will completely change the industry. Processes will become more intelligent, and our ability to optimize machine life and resource usage will minimize the environmental impact of what we do while maximizing profitability. And processes will adjust with more ease to changing business targets.
How AI Insights Unlock Unheard-Of Manufacturing Optimization
Today, there are still manufacturers who think they need to rip out old machines and build new production plants to meet consumer demand and produce new iterations of products. That is neither efficient nor cost-effective, and the application of prescriptive maintenance technology can resolve that problem as well.
Related: Learn more about production health in our on-demand webinar.
AI-enabled machines run by a small team of highly sophisticated workers can unlock shadow capacity in existing plants. Companies have specific production problems, and when AI is targeted at those particular issues, teams can gain the valuable data and insights needed to improve them and then move on to address their next business concerns.
This is the future, today: We can combine the AI insights from process health and machine health, enabling a level of manufacturing optimization previously unheard of. Production Health means $1 trillion in added productivity and 16 billion tons of reduced emissions. Once hybrid intelligence achieves that, who knows what else we will change.
The Augury Way of Production Health
Augury provides end-to-end solutions that help eliminate production downtime, improve process efficiency, maximize yield, and reduce waste and emissions. We empower our customers with prescriptive insights into their processes and machines through AI-driven technology and industry-specific expertise that helps transform how they work.
For more information on how we can help you reach toward Industry 5.0, contact us today.