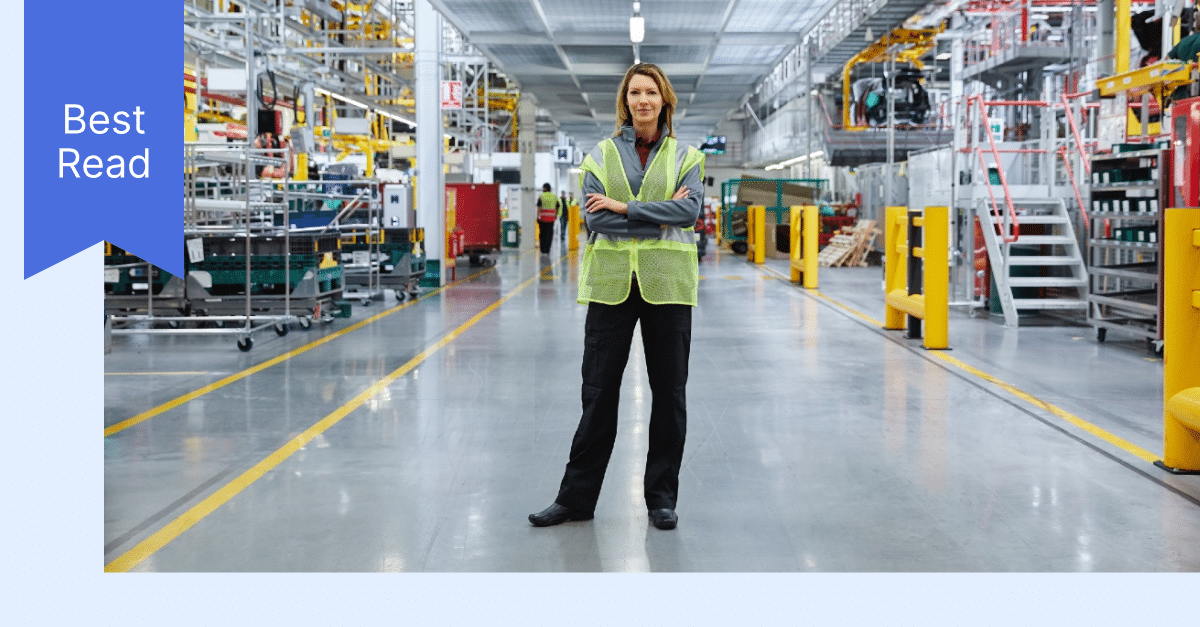
For factories out to improve their Total Productive Maintenance culture, IIoT-based tools can empower their workers to make data-driven decisions to help drive better Overall Equipment Effectiveness.
This article was originally published March 4, 2019 and updated in October 10, 2024.
Wired Magazine Founder Kevin Kelly once said: “Productivity is the wrong thing to care about in the new economy. Productivity is for robots [and machines].”
But in today’s modern factory, he’s only partly right. Yes, productivity matters for machines, but it’s also the primary concern for many people who manage, maintain, and optimize machine productivity.
Total Productive Maintenance and Overall Equipment Effectiveness
In many factories, Total Productive Maintenance (TPM), is used to measure and manage productivity through a human and organizational culture lens. TPM is a process-improvement-based methodology concerned with continuously optimizing machine and factory productivity.
One of the primary objectives of TPM is to increase Overall Equipment Effectiveness (OEE). OEE is a widespread standard for measuring and managing machine productivity in factories. It is generally calculated as: OEE = Availability x Performance x Quality and is measured from 0-100% (the higher, the better).
OEE = Availability x Performance x Quality
IIoT-powered predictive maintenance (PdM) technologies can make a major contribution to improving OEE by immediately decreasing downtime in factories. We have found that, depending on the industry and equipment, continuous monitoring solutions can improve OEE.
Getting More Machine Visibility with PdM
An IIoT-based predictive maintenance solution goes beyond just reducing downtime for machines. It also amplifies the effectiveness of TPM-based continuous improvement projects. It does this by:
- making the entire operation more visible
- making data associated with symptoms and root causes more accessible
- offering up new modes of operational analytics and mechanical analysis
One example is an Augury customer that produces a consumer packaged goods item that you can find in local convenience stores. Prior to installing Augury, the manufacturer needed to take down an important machine each day for half an hour to do a manual inspection and determine if the machine parameters needed to be optimized for improved performance.
Saving Human Hours For Higher Value Work
After installing IIoT sensors on the machine, maintenance staff decided that this daily inspection was no longer required. They realized that the machine could be remotely monitored using Augury’s rich, cloud-based data and analytics. They began to take the machine down only when optimizations were required, which was determined based on trend data of anomalies detected by the sensors.
This saved the factory about 50 hours per month of human time, increasing OEE. The factory workers’ time could then be more focused on higher order TPM activities, including data-driven searches for new waste reduction opportunities on the shop floor.
The solution is turnkey and automated, so factories don’t need to collect any new data. With Augury’s Machine Health Solutions, there are no required manual vibration recording “routes” once the sensors are installed. Data can be easily integrated with existing software systems already being used onsite.
Unifying Teams Around Common Goals
IIoT-based PdM even improves team culture. There is often an inherent tension between operators (in charge of running machines), and maintenance staff (in charge of taking machines offline to repair and maintain them). Operators are focused on meeting production quotas and are not primarily focused on reducing machine failures. Maintenance and reliability staff are focused on reducing total downtime, which sometimes means proactively scheduling planned downtime to lower the risk of failure in the future.
IIoT-based continuous machine monitoring reduces the potential for conflicting opinions between opposing roles and objectives on the shop floor. The decision regarding if or when to take machines offline becomes data-driven, less subjective, and more actionable. After an IIoT installation, these roles can now collaborate more effectively.
Being Proactive Around Continual Improvement
Overall, this kind of on-demand, predictive maintenance is what the best manufacturers want. They don’t want to follow an instruction book blindly, or feel obliged to do any maintenance task that doesn’t increase overall productivity. They live and breathe TPM and the mantra of continuous improvement.
In this spirit, predictive maintenance technologies from the IIoT empower them to find new, previously inaccessible solutions to factory waste.
For factories looking to improve their TPM culture, and add new tools to empower their workers, the IIoT has a lot to offer. While it won’t solve problems on its own, it will make TPM processes easier, and OEE optimizations more obvious, while also improving data-driven decision-making and reducing guesswork.
See how Augury has helped other organizations rally around TPM.