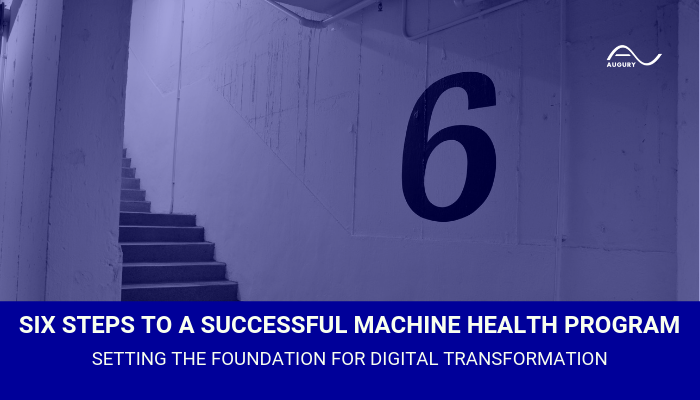
Machine Health digitizes the assets at the heart of a manufacturer’s supply chain and automates machine condition monitoring and diagnostics. And thereby, such a programs lays the foundation for the larger and long-term goal: complete digital transformation.
As a successful digital transformation use case, Machine Health does double duty: It provides fast time-to-value by making manufacturing assets more reliable and predictable but also lays the foundation for higher-level digital transformation use cases like optimizing automated machine monitoring performance and lights out facilities.
So how can you roll out a successful Machine Health initiative? Augury has supported dozens of rollouts and we have identified six key steps to success.
1.Define the problem
What is the most important problem that Machine Health should address at the plant level? Should it reduce downtime, improve agility, lower throughput time, or improve on-time delivery (OTD)? Interview a range of employees from mechanics on the shop floor to the plant manager and corporate reliability stakeholders. Which pain point is most prominent? The rollout must be structured to deliver rapid time to value for that specific problem. Next, choose the specific assets, components and production lines which will be used to attack the problem. Defining the problem up front takes time, but will save effort later.
To justify scaling up after a successful initial rollout, you must demonstrate that results can be replicated across multiple plants. We recommend that you rollout automated machine monitoring on production lines in at least two different plants simultaneously to compare results in different operating environments. Augury’s web app makes it easy to compare results across plants.
2. Choose your metrics
The metrics you choose should allow you to measure machine health and digital transformation success. Downtime, OEE, and emergency overtime work hours are some typical metrics. It’s important to collaborate both with senior management and with the stakeholders who will be responsible for carrying out the digital transformation process at the plant level. Alignment and buy-in from both groups are critical for adoption. If the stakeholders cannot agree on the metrics to track, this will significantly impede the effectiveness of your rollout. Benchmark the current values of the chosen metrics at your target plant(s) to use as the starting point of your rollout.
3. Map your data flows
Where is the data you need to address your problem? Do you even have enough data to understand the source of the problem, i.e. what’s causing OEE to suffer? Do you have sufficiently granular data to understand the root causes of downtime? Is the data accurate? It’s not enough to know that you had downtime at 3 pm on Wednesday; you need to know which machine downtime occurred on and why. The good news is that even if you are not confident in the quality of your current data, implementing a Machine Health program allows you to start collecting the data you need.
If the data resides in multiple systems, can you integrate them? Create a process flow map of how information flows within the plant and where disparate data sources need to come together. Augury routinely integrates our Machine Health solution with software already in use on-site, thereby reducing friction later.
4. Assign responsibilities
The owner of the Machine Health rollout within the digital transformation process should work with a site-level owner who is responsible for execution. List all of the tasks which must be completed and decide who is accountable and responsible for each task. Who will react to condition monitoring diagnostics or specific recommendations? Who actually is “turning the wrench”? Who will track the results? Who is responsible for training? Does the team understand how and whom to ask for help?
5. Execute rapid sprints
Once the Machine Health technology is installed and collecting data, the rollout should use a test-and-learn approach executed in weekly sprints. At the end of each sprint, check metrics, identify any obstacles and quickly resolve them. A sprint checkpoint meeting is not a project update but instead must focus on removing any major barriers to progress.
During a sprint checkpoint meeting, review levels of adoption by operators, changes in metrics and human resources issues. Is the Machine Health system being adopted at the plant level? According to a study from Harvard Business Review, “Nearly 90% of the companies that engaged in successful scaling practices had spent more than half of their analytics budgets on activities that drove adoption…” Take a look at whether the reliability team is reacting to diagnostics and the number of daily users. Are your chosen metrics improving or not? If not, determine why and refine your execution strategy in the next sprint. Are human issues blocking progress? Plant-level staff may be working on the initial rollout on top of their day jobs. A key staff member might need time dedicated to working on the program, operators might need additional training or to be incentivized in a new way.
6. Communicate results
It’s better to communicate too much and too often, rather than too little and too late. Plant-level employees are closest to the machines being digitized and the problem being addressed. They need to understand how the new technology benefits them and how the program is progressing. Get their feedback. Continuously highlight progress. Have an operator present a win to fellow operators. The first wins help build team confidence in the effectiveness of a new program and prove that it’s not just another ‘management fad’ that will go away in a few months.
Machine Health does more than deliver quick value at the plant level. By digitizing your machines, it lays the foundation for a digital transformation process. A successful Machine Health program is the first step in that long and exciting journey.
Want to talk about implementing a Machine Health program?