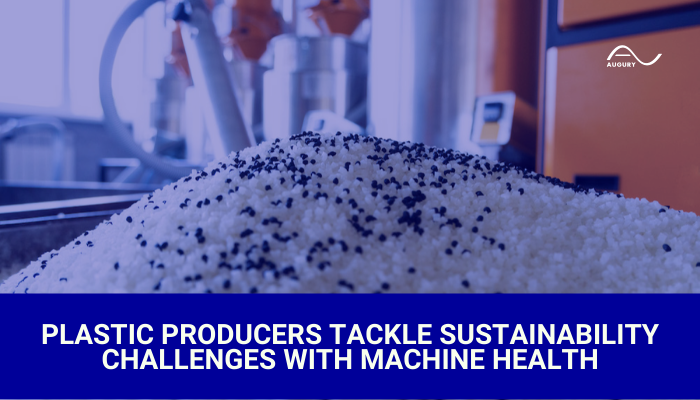
Everyone knows that sustainability is changing the manufacturing game – it really doesn’t matter what industry you’re in. One example is automobile manufacturing, where an increased focus on improving energy efficiency has made the shift from metals and alloys to lighter-weight plastic components into the new common sense. This is great news for the plastic industry, which is expected to reach a value of $721.14 billion USD by 2025.
But in the era of sustainability, growth brings specific challenges for plastic manufacturers. Consumers are increasingly concerned about the impact of single-use plastic waste in the environment, especially as China and other southeast Asian countries are no longer importing the quantities of plastic for recycling that they once did. Meanwhile, fluctuating oil prices are making it more and more important for manufacturers to sustainably source raw materials, and use them as efficiently as possible to maximize throughput. And while recycled plastic is now in high demand, not all recycled resins meet consistent standards.
Taken together, these new realities mean that plastic manufacturers looking for an edge must get creative, and find novel ways to increase efficiency, reduce costs, and respond to sustainability demands.
So what can plastic manufacturers do to meet these challenges?
While there are no straightforward answers to one of the biggest questions of the 21st century, forward-thinking plastic manufacturers are tackling the challenge with machine health solutions.
Using recycled components is perhaps the most obvious of these. Recycling helps reduce dependence on raw petroleum products, thereby increasing efficiency, improving sustainability, and reducing critical perceptions of the industry. The problem, however, is maintaining consistently high quality in recycled materials. When firms are buying recycled pellets from off-shore plastic recyclers, quality can be a crapshoot–and no manufacturer wants to gamble on sub-par materials.
In response to this problem, the most innovative plastic manufacturers are getting ahead of the curve by moving toward vertical integration of their production processes. By getting into the recycling game, plastic manufacturers can exert more direct control over efficiency and sustainability throughout the manufacturing chain from raw inputs through to finished products. However, it also presents many points at which quality can be compromised–and this is where machine health becomes more important than ever.
Organizations monitoring machine health are applying lessons of sustainability to their operations and internal resources – becoming more efficient while saving money and time. Firms that pay attention to the optimal operation of the machines used in their manufacturing process can identify potential trouble spots and anticipate machine failures before they happen, avoiding costly unanticipated downtime and increasing overall production efficiency. This translates directly into dollars saved and less waste.
Consider the thermoplastics manufacturing process and its range of machine-assisted processing techniques. Facilities that perform extrusion, slow-molding, and injection molding processes depend on machines like single- and twin-screw extruders, dust and fume collectors, pelletizers, vacuum pumps, and chilled water pumps to work effectively whenever the line is running. If any one of these machines fail, or even functions below their optimal efficiency, the entire facility risks under-performance and production delays.
For example, a leading rigid plastic manufacturer recently turned to Augury’s continuous monitoring solution after a series of mechanical failures caused them to lose shelf space and market share to their competition. With Augury’s help, they determined the most critical assets needed to keep their lines running efficiently and to meet their production demands.
Within months Augury diagnosed early-stage bearing wear within their twin-screw extruder, an expensive asset highly critical to their production process. Given the advance notice, the plant was able to schedule the necessary repairs during their next planned downtime. Equipped with a clear understanding of the issue and best maintenance practices for fixing it, the team was able to optimize their technician’s wrench time during the planned downtime and had the extruder up and running swiftly.
While no one wants to discover faults developing within their machines, it’s far worse to not find out until it’s too late. The good news is that by investing in machine health monitoring and identifying faults at their earliest signs, teams discover problems well before their equipment fails — keeping them on target to meet their efficiency and sustainability commitments.
In 2020, we know that corporate social and environmental responsibility have to be more than just buzzwords. Rather, companies must demonstrate their sustainability commitment by becoming as effective and efficient as possible in their manufacturing processes. It’s certainly a bonus when these sustainability measures simultaneously drive competitive edge. By focusing on machine health, plastic companies can improve their business while also tackling sustainability challenges head on.