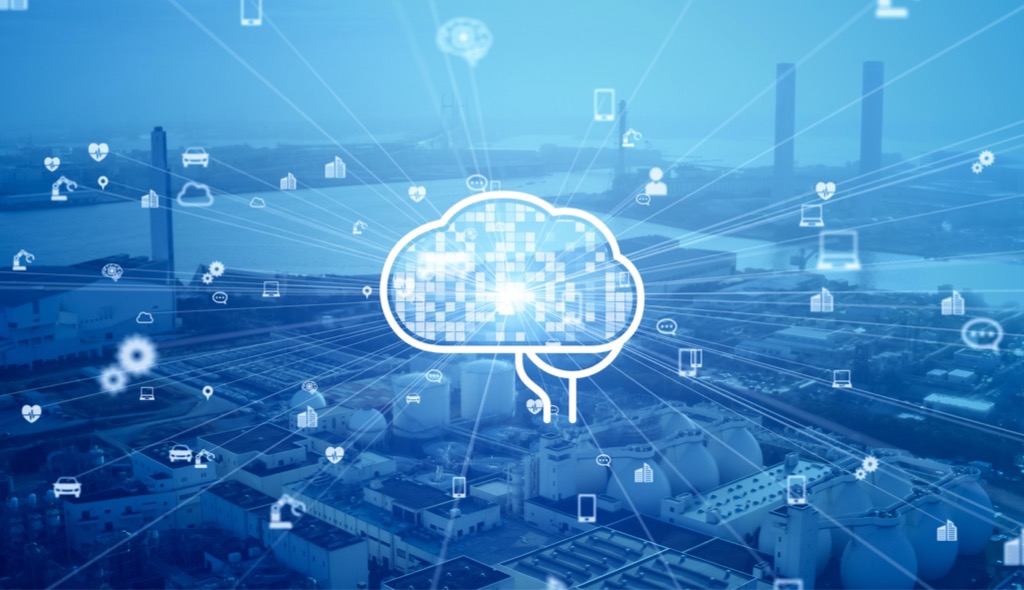
Every day, digital transformation in manufacturing becomes a bigger priority. With new machine capabilities come rethinking the role of maintenance technicians.
This article was originally published in Global Trade Magazine.
Machines are at the heart of manufacturing. They affect every aspect of production — efficiency, output, quality, consistency — and form the basis of manufacturing performance. So it comes as no surprise that many use cases for digital transformation in manufacturing focus on machinery. It’s where the transformation manifests itself.
How it manifests itself is more complicated than it seems, however. Some may think that the primary goal of digital transformation in manufacturing is to make machines better at their intended purposes — by using digital technology to help them run faster, longer, or with greater precision. This is one goal, but digital transformation is also about much more than that. Another crucial component is giving machines new capabilities and greater purpose.
Here’s an example: When machines are equipped with internet-connected sensors that can collect machine health data and send it to a centralized platform, then each machine becomes an indicator of the overall health of the production line. Studying the parts reveals the condition of the whole, whether that’s a single production line, an entire factory, or a global supply chain.
This wasn’t possible prior to the new technologies of industry 4.0 because manufacturers had no way to monitor machine health remotely and comprehensively. But it’s possible now, and it’s changing expectations around digital transformation in manufacturing.
Driving Digital Transformation of Machine Maintenance
With additional machine capabilities should also come a rethinking of the role of maintenance technicians. They’re not just the on-site problem-solvers anymore — they’re the ones who move digital transformation forward as they keep machines up, running, and evolving. Technicians may not be the architects of digital transformation in manufacturing, but they are the drivers of it.
In that context, it’s time to consider upgrading the roles of the technicians closest to the machines. The maintenance of the past isn’t appropriate for the factories of the future. Technicians need new skills, tools, and processes to leverage the advanced capabilities being added to machines. They also need a new mindset, mission, and role within the factory. To put it differently, maintenance technicians need to transform as much as the machines they work on. Here’s how manufacturing leaders can help:
1. Change Your Mindset From Maintenance to Risk Avoidance
In the past, when technicians serviced machines because of a breakdown or because of a service schedule, the entire focus was on minimizing machine downtime. Fewer failures and faster fixes meant the maintenance department was doing its job.
Instead of focusing on solving problems after they occur, however, maintenance teams should focus on preventing them. When maintenance sees its primary purpose as risk avoidance, it puts everything technicians do into a new perspective. The team is focused on intervening early and effectively so that minor issues don’t develop into downtime.
Risk avoidance (rather than minimization) is possible when maintenance teams shift from reactive and preventive maintenance, which lag behind problems, to predictive and prescriptive maintenance, which lead ahead of them. Machine health monitoring sensors make that possible while also showing the maintenance team where, when, why, and how their agile efforts helped to prevent disasters.
2. Think About Digitizing Maintenance as a Skill Set Upgrade, Not Just Another Tool
Digital transformation in manufacturing is about more than just adding a bunch of new digital tools to your technicians’ tool belts. If you just give them better ways to do what they were already doing, you won’t see dramatic improvements from digital transformation efforts.
Instead, think of digitization as more than a bonus tool. Think of it holistically as a whole skill set upgrade for your team. Digital tools will allow maintenance technicians to spend less time on menial, repeatable tasks and transition that energy instead to higher-value knowledge work like prescriptive maintenance that can keep machines running better for longer.
3. Improve Your Collaboration Capabilities
Digital transformation in manufacturing maintenance is largely about improving collaboration capabilities. Maintenance teams are using technology to help them spread their resources around as quickly, widely, and effectively as possible. All three of those depend on maintenance teams working collaboratively.
In practice, that means each technician, team, and site has access to the same data and alerts. Everyone works from a single source of truth so that wires don’t get crossed, warnings never get ignored, and resources move everywhere efficiently. However digital transformation affects maintenance, increased collaboration should be the goal.
Every day, digital transformation in manufacturing becomes a bigger priority. Many manufacturers will discover that in their race to digitize, they forgot to update maintenance at the same pace. Those that do the opposite will discover something as well: Digitizing maintenance propels the broader transformation effort forward because it allows machines to do more than they ever have.
Learn more about how Augury offers shortcuts to digital transformation.