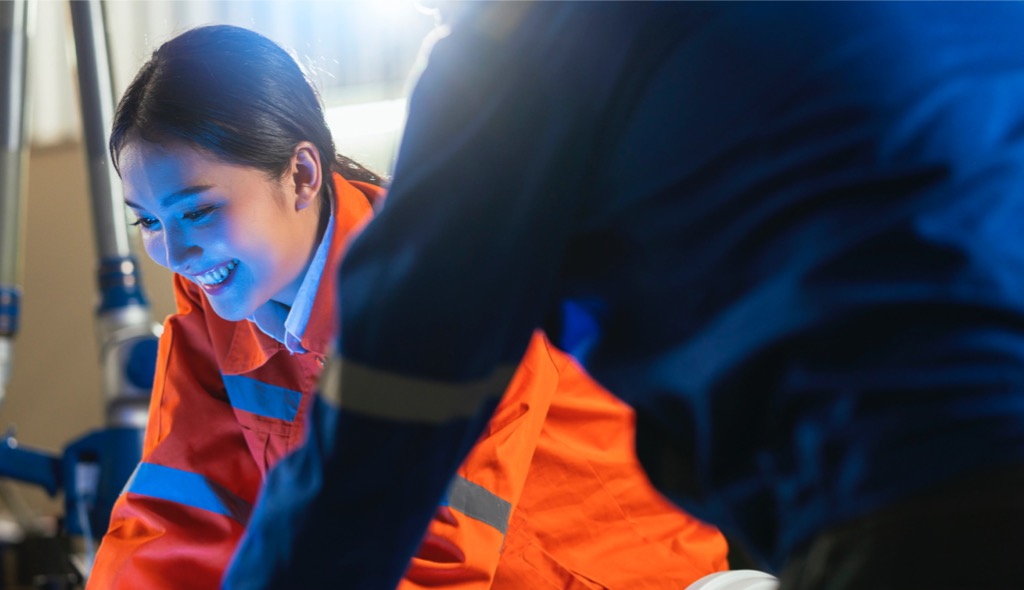
As manufacturing organizations embark on journeys in digital transformation, they must rethink old roles. The integration of new tools and technologies opens up the space for new skills aimed at driving innovation into the future.
Digital transformation in manufacturing is upon us. Advanced tools and technologies allow workers to make smarter, faster decisions. But reaping the full benefits will mean shutting down the divide that has long persisted in manufacturing: the separation of leadership teams from frontline workers.
Traditionally, leadership makes the decisions, and those on the production floor carry out the tasks in response. This model might have worked fine for years, but it is now a barrier to realizing the full potential of industry 4.0.
Breaking down the barrier means creating new hybrid workers trained to make the same decisions management has for years. It also means equipping them with the tools they need to back those decisions with data in real time. These new roles will blur the lines between traditional areas of expertise to drive new value, innovation, and growth:
1. Machine Ops Specialists
With total productive maintenance, the goal is to take a more holistic manufacturing and machine health monitoring approach. It works under the principle that the people closest to the production line should have some skills to operate and maintain equipment.
Enter machine ops specialists, who serve as a bridge between the worlds of operations and maintenance. They bring an understanding of the equipment’s operational context and the mechanical components of those machines, combining responsibilities for maintaining machine health and equipment performance.
Machine ops specialists do more than merely report malfunctions or check for mechanical issues. They utilize AI in manufacturing, applying predictive insights to drive work based on the equipment’s condition and intended operational outcome. Machine ops specialists can turn to tools like Augury for the clear machine data and insights they need to drive outcomes.
Find out how Augury can help you optimize your assets.
2. Cultural Translators
The manufacturing industry has long been at odds with the modern ways of working. It has held onto a strict hierarchy in terms of decision-making capabilities, which now leads to less agility, a loss of knowledge transfer, and even a stifling of innovation.
While manufacturing change management can help, it’s no small feat. Such a task requires a collective shift in mindset where it’s everyone’s job to be part of the change. But without the proper infrastructure in place, people remain unaware of how to contribute to that initiative.
At some operations, that responsibility falls to the cultural translator, a manufacturing change management role focused on changing the way people work at all levels of an organization. Think of it as transforming the workforce through different tools, processes, and structures — not necessarily just training or upskilling. This role should help create cross-functional collaboration and facilitate the right tools for people to work in meaningful ways. This doesn’t mean hiring some expert from the outside. Instead, develop talent internally to take up the helm.
3. Virtual Shift Champions
Digital transformation in manufacturing extends beyond machines alone. It also holds the potential to transform and enhance communication. Already, some manufacturing companies have control towers or centers of excellence tasked with supporting the production shift to a virtual environment. Such a move can bring value to people on the production floor, providing remote expertise to enable digital transformation in manufacturing facilities.
No longer does enhancing operations mean transporting experts from site to site. Instead, data and expertise can be exchanged remotely — a massive improvement in scalability.
This virtual shift also takes AI in manufacturing to the next level, synthesizing insights across hundreds of thousands of machines into a single source. No one is left analyzing data all day. Instead, experts can focus on pressing issues and offer in-context communication through video, like with Augury’s Threads tool, to people on the production floor. It combines actionable data insights with remote collaboration capabilities among employees, original equipment manufacturers, services providers, and so on.
Learn more about Augury Threads.
Organizations that want to see digital transformation in manufacturing meet its fullest potential must prioritize their workforces in the transformation. As you integrate new tools and technologies into your operations, consider how old roles may change to give way for innovation.
Want to learn more? Just reach out and contact us!