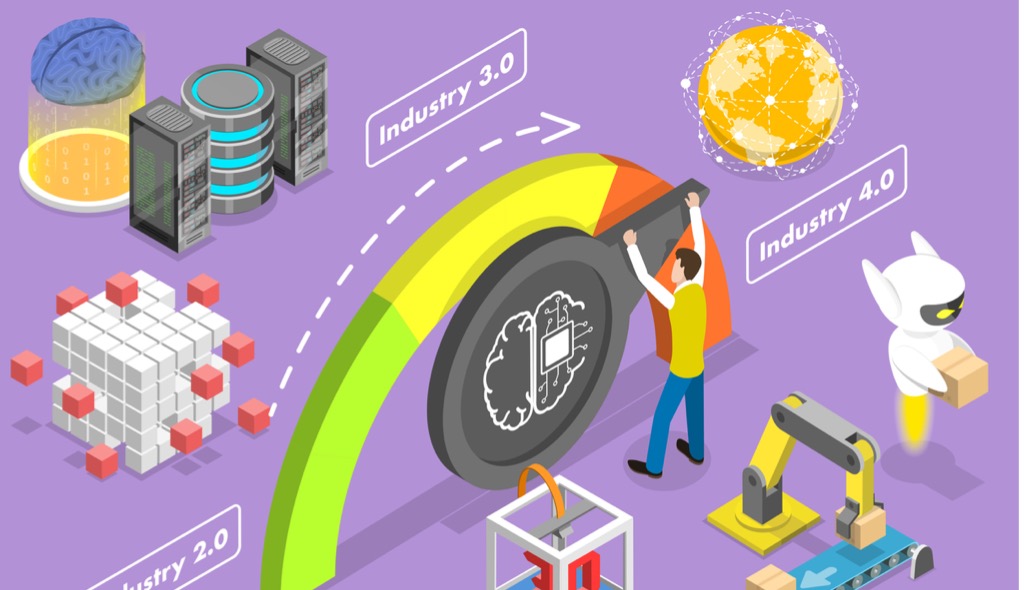
Making industry 4.0 a reality requires more than just buying new technology. A technology that is not being used won’t deliver value. Machine health is an industry 4.0 use case that promises to transform expectations around machine maintenance. Driving adoption at the plant level has proved to be the key when it comes to getting value from machine health fast and at scale.
A proper onboarding process is essential for manufacturers to reap the benefits of predictive and prescriptive maintenance practices enabled by machine health. Leaders must consider that onboarding the new solution involves more than initial installation — it’s also about helping teams understand how the solution works and why it’s important.
Start by rolling out at one or two sites to begin showing your teams how to derive value from machine health, then take those insights and scale them across your organization to facilitate widespread adoption.
Careful consideration at this stage will save you time, money, and frustration down the line.
As digital transformation in manufacturing continues to accelerate rapidly, it’s understandable that some leaders might be concerned with moving too slowly. But a proper onboarding process is key to the long-term success of new technology implementation. Careful consideration at this stage will save you time, money, and frustration down the line.
Important Steps in Machine Health Onboarding
Begin the onboarding process by identifying your key performance indicators for machine health. Demonstrate and quantify how much the use case will impact bottom-line metrics. Think of how machine health will further the overall corporate strategy by cutting costs, increasing efficiency and productivity, accelerating digital transformation, etc. If your KPIs reflect these goals, any improvement toward them will count as a win.
Augury facilitates the onboarding process through our customer success team, which acts as a consultant, technician, and motivator: everything necessary to make the earliest machine health rollouts go exactly as intended. The customer success team shows a maintenance crew how to gain value from machine health monitoring by using early warnings to proactively perform machine maintenance.
There may be some bumps along the way — missed alerts, slow responses, ineffective repairs, etc. — but the customer success team is there to make these mistakes into learning opportunities. Most maintenance teams learn how to handle the alert-investigate-repair cycle after three to five full machine improvement cycles.
Tracking Onboarding Success
Because predictive maintenance is all about early intervention, it’s important for maintenance teams to investigate after receiving an alert; otherwise, preventable issues could still escalate into major problems.
One goal of onboarding should be to have maintenance teams responding to at least 75% of the alerts they receive. This number will increase as teams grow more familiar with the technology and perfect their processes, but 75% is a great place to start.
Technicians under the guidance of the customer success team should learn how to interpret these signals during the onboarding phase and how to provision their resources where it matters most.
Another related goal of onboarding is that teams should learn to prioritize which alerts they do respond to. Machine health data reveals which machines require urgent attention and which can wait until later. Technicians under the guidance of the customer success team should learn how to interpret these signals during the onboarding phase and how to provision their resources where it matters most.
Above all, onboarding an effective use case lays the groundwork for a broader deployment of machine health technology. And just like the onboarding phase, the larger-scale adoption phase that follows requires a careful approach.
Moving Into Adoption
Provided that the onboarding phase went as planned, there should be momentum and enthusiasm around machine health at sites where it has been deployed. Maintain that momentum into the adoption phase by quantifying wins: How much downtime did predictive machine maintenance prevent, and how much money did that save?
Seeing the impact of this technology in hard numbers and real-world settings makes it easier for stakeholders at all levels to buy into adopting machine health monitoring across an organization.
Make sure that KPI improvements are captured and quantified at every opportunity by designating someone for this job. Whatever successes this person discovers should be communicated and celebrated, not just recorded.
Tracking Adoption Success
The adoption phase should also improve on the skills learned during onboarding. Maintenance teams should be addressing 85% of alerts and responding within 10 days by the end of the adoption phase.
It’s also about building on that success to make machine health monitoring so viable and beneficial that there’s no objection to a bigger rollout.
To reach those targets, maintenance will need to start addressing issues that aren’t imminent but still require attention, which will require the further refinement of prioritization skills beyond the onboarding phase. In that way, the adoption phase isn’t just about replicating the success of the onboarding phase on a wider scale; it’s also about building on that success to make machine health monitoring so viable and beneficial that there’s no objection to a bigger rollout.
To carry out successful digital transformation initiatives, you have to build from a strong foundation. Overlooking the importance of thoughtful onboarding and adoption practices will only slow you down in the long run. Dedicate time and attention to earning stakeholder buy-in and demonstrating early and often how machine health can transform machine maintenance for the better, however, and you’ll be well on your way to success.
Learn more about ‘The Road Map to Value for Digital Transformation of Maintenance in Manufacturing‘.