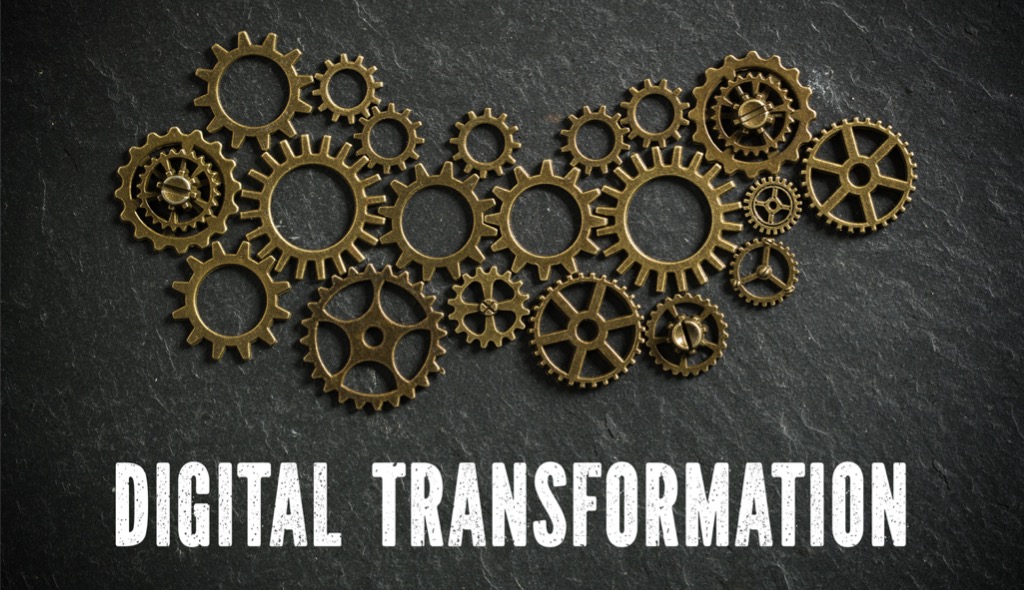
The next era of manufacturing has arrived. Factories are undergoing digital transformation from top to bottom and using data-driven technologies to integrate every facet of production, both inside and across facilities.
Courage And Caution
Realizing the full potential of industry 4.0 manufacturing will require equal amounts of courage and caution. Manufacturers need to try new things, but they can’t commit to the wrong technologies. That’s why use cases will be critical for making digital transformation successful.
Experimenting with new technologies and processes on a small scale and learning what works first will make it much simpler to deploy those same changes to all corners of the enterprise. Start small, scale smart.
Use cases have been particularly helpful for exploring applications of new technology in machine maintenance. Manufacturers need to prevent breakdowns and minimize downtime, but the reactive and preventive approaches they currently use for manufacturing maintenance don’t excel at either of those goals.
The emergence of IoT sensors installed on equipment to collect machine health data promises to revolutionize maintenance practices to make industry 4.0 a reality.
Advanced Warning: Predicting And Preventing Problems
Consider one common use case for machine health monitoring sensors: Data flows into an analytics platform that looks for changes in key machine health metrics. If anything indicates an issue that could evolve into something worse, the maintenance team receives a notification. They know where the issue exists and have insight into what’s going wrong.
The maintenance team also has enough advanced warning to intervene long before a machine breaks. It’s a completely different paradigm for maintenance: one focused on predicting and preventing problems rather than mitigating them after they occur.
Improving Collaboration
Another use case involves using machine health data and predictive maintenance capabilities to improve collaboration between technicians. Equipping technicians with clear insights into machine performance makes it easier for them to collaborate with each other from remote locations and enlist third-party experts from anywhere around the world when necessary.
No one has to be in front of the machine to explore its performance. This will introduce another new paradigm: a virtual shift that prioritizes remote monitoring above on-site checkups.
Embracing Change
As these use cases demonstrate, machine maintenance is ripe for digital transformation, and the technology is available now. Maintenance can be the starting point of a larger change throughout the factory – and digital transformation isn’t complete until maintenance updates itself for industry 4.0.
In this post, we will outline how to embrace this change and turn it into lasting value for maintenance and manufacturing as a whole.
Seeing Value From A Machine Health Monitoring System
Once a manufacturer has sensors that can monitor machine health data and a platform that can ingest and analyze that data to predict performance issues, the easy part is done. Much harder than investing in technologies is putting them to productive use inside manufacturing environments with a set way of doing things. That’s where a change management strategy comes in.
Working through change strategically and systematically ensures that it’s an improvement rather than a disruption. Without some sort of strategy in place, it’s difficult or even impossible for manufacturers to generate quantitative or qualitative value from use cases with machine health sensors. They become a lost opportunity.
Setting Up The Value Team
Setting and guiding an effective strategy, however, takes a value team: a group of stakeholders from different departments who act as change agents within the organization. It’s their responsibility to create buy-in around new ways of doing things and make the transition from one approach to another as seamless as possible.
The value team is central to the whole effort; they’re the ones pushing digital transformation forward while devising how to turn promising technologies into practical solutions.
The ideal value team includes diverse perspectives and skill sets along with a shared commitment to acting according to data, using machine health data to the fullest, and spreading enthusiasm about industry 4.0. These are the evangelists, and they should be divided into the following roles:
- Corporate champion — This person contributes a C-suite perspective and takes responsibility for delivering enterprise-level results.
- Corporate enabler — This person provides subject matter expertise on whatever business unit the machine health use case affects: production, QA, etc.
- Site leader — This person leads the site where the sensors will be deployed and serves as both champion and supervisor of the use case.
- Problem solver — This person is a technician working with machine health data to practice predictive and prescriptive maintenance.
- Planner — This person coordinates when machines shut down for maintenance to minimize downtime and limit the impact on production.
With the value team up and running, it’s time to address the technology itself and start answering the hardest question of all: How exactly will we transform maintenance to meet the demands of industry 4.0 manufacturing?
Taking The First Steps With Sensors
Every value team will look different, as will every use case. That said, the team’s first initiative should always be to drive adoption at the plant level: where the importance of maintenance and the challenges are most apparent.
Beyond the implementation, rolling out a machine health monitoring system requires an extensive onboarding process . It should help teams understand how these systems work and why they’re an important upgrade. Onboarding should also emphasize how machine health data makes life easier on the maintenance team by replacing frantic repair situations with an orderly process of preemptive maintenance. People should feel excited to do things differently.
Keeping An Eye On The KPIs
Develop a set of KPIs to measure the performance of the use case. Tie those KPIs to the broader corporate strategy — for example, if the goal is to lower downtime costs, set a high quota for the number of alerts maintenance teams should respond to (75% is a good place to start).
Being proactive about early intervention helps prevent breakdowns and the lengthy downtime that comes with them.
When the onboarding process runs effectively, it lays the groundwork for a broader introduction of predictive and prescriptive maintenance based on machine health monitoring. That’s the best case for onboarding: It turns a use case into a permanent part of digital transformation.
Maintaining Momentum After Onboarding
After the onboarding phase comes the adoption phase: when machine health monitoring becomes a permanent and growing feature of the factory. This is when use cases transition into lasting changes because they’ve proved to be valuable and viable. Keeping up the momentum around new technology and preventing a drift back into the status quo takes a conscious effort.
The value team should keep evangelizing for machine health data by highlighting what it does for the company. Use stats about how much downtime the company avoided and how much money that saved to help prove the technology merits wider adoption.
Framing things in quantitative terms helps emphasize that the benefits of machine health monitoring are neither hypothetical nor abstract.
Celebrating The Wins
Toward that end, designate someone to collect and quantify KPIs related to maintenance wherever they’re available. Look for wins in any form, and celebrate them instead of just recording them. It’s also important to start raising standards as technicians become more comfortable with predictive maintenance. By the end of the adoption phase, technicians should be responding to at least 85% of alerts within 10 days.
The goal of the adoption phase is to apply the lessons learned during the onboarding phase to create a use case that can scale out of one factory and into another, eventually encompassing and integrating everywhere that industrial equipment exists.
The steps that come after onboarding and adoption are when things truly get exciting, but that potential depends entirely on going through these two phases first.
Scaling The Use Of Sensors
Digital transformation into industry 4.0 manufacturing becomes a reality once machine health data drives all aspects of maintenance. Scaling the technology across sites means repeating the onboarding and adoption phases at each location. Being thorough is important, but scale demands speed. Here are a few ways to (quickly) replicate the success of one use case at other sites:
- Make a playbook — Take lessons, best practices, and troubleshooting tips learned from the early use cases and turn them into a playbook for future adopters to follow.
- Recruit influencers — Have employees who have been through the onboarding and adoption process help champion it at the next sites to adopt machine health monitoring.
- Extend skills — Use machine health data to understand what skills are missing from the maintenance team, then train someone in those skills who can assist technicians across sites.
- Invent value — Let maintenance teams discover new ways of using machine health data to their advantage rather than dictating limited ways they can use the technology.
When manufacturers focus on early onboarding and adoption and continue thoughtfully from there, new technologies scale seamlessly and digital transformation happens organically. Start with a machine health monitoring system to transform maintenance and, in the process, open the door to industry 4.0.
How much can Augury save you? Crunch the numbers with our value calculator and discover how much time and money you can save with our proven approach to machine health.